Sand Casting Iron A Foundational Technique in Metalworking
Sand casting is a time-honored manufacturing process that has played a pivotal role in the production of iron components for centuries. This technique offers a versatile method for producing complex shapes and intricate designs, making it a staple in the metalworking industry. The process involves creating a mold from sand and then pouring molten iron into that mold to form various iron products.
The Process of Sand Casting
At the heart of sand casting is the creation of a mold. The first step involves creating a pattern, typically made from wood, metal, or plastic, which represents the final product. The pattern is placed in a sand mixture, often composed of silica sand, clay, and water, which binds the particles together. The sand is packed around the pattern, forming a mold cavity when the pattern is removed.
After the mold is prepared, the molten iron, usually heated to around 1,500 degrees Celsius, is poured into the mold cavity. The iron fills the voids, taking the shape of the pattern. Once the metal cools and solidifies, the sand mold is broken apart, and the final iron casting is revealed. This casting can then undergo various post-processing techniques, such as machining, grinding, or polishing, to achieve the desired finish and tolerances.
Benefits of Sand Casting Iron
sand casting iron
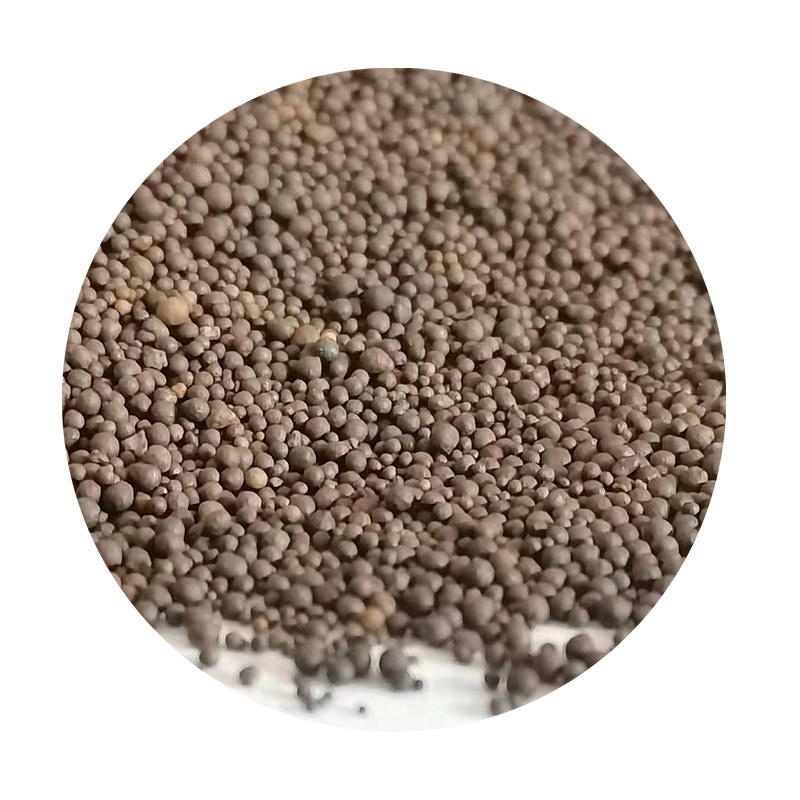
One of the most significant advantages of sand casting is its adaptability. It can produce both small and large components, making it suitable for a wide range of applications. Additionally, the sand mold can be reused multiple times, which helps reduce material costs and waste. Sand casting is particularly advantageous for producing intricate designs and complex geometries, as the mold can easily accommodate various shapes.
Moreover, the process allows for a wide range of metals to be cast, although iron remains one of the most common materials used. Different types of iron, such as cast iron and ductile iron, can be used depending on the desired properties of the final product. Cast iron is favored for its excellent castability, wear resistance, and good machinability, while ductile iron offers greater tensile strength and ductility.
Applications of Sand Cast Iron
Sand cast iron has a vast array of applications across diverse industries. It is commonly used in automotive manufacturing for engine blocks, transmission cases, and various other components. In the construction industry, sand cast iron is utilized for manhole covers, sewer gratings, and decorative architectural elements. Furthermore, the process is important in producing machinery parts, farm equipment, and even artistic sculptures.
In conclusion, sand casting iron is a foundational technique in the field of metalworking, characterized by its versatility, cost-effectiveness, and ability to produce intricate designs. As industries continue to evolve, the relevance and application of sand casting remain significant, underpinning the creation of robust and reliable iron components essential for modern engineering and manufacturing. Whether for industrial, artistic, or functional purposes, sand cast iron continues to make its mark in the world of metallurgy.
Post time:Aug . 27, 2024 18:23
Next:सैंड कास्टिंग स्टेनलेस स्टील - सर्वोत्तम गुणवत्ता और टिकाऊ उत्पाद