The Manufacturing Process of Resin-Coated Sand
Resin-coated sand has gained significant popularity in the foundry industry due to its superior performance in molding applications. It offers excellent strength, hardness, and surface finish, making it ideal for various casting processes. Understanding the manufacturing process of resin-coated sand is essential for appreciating its role in modern foundry operations.
The manufacturing process begins with the selection of high-quality base sand, typically silica sand. The chosen sand must meet specific criteria, including particle size, shape, and cleanliness, to ensure optimal performance in the final product. This base sand is then subjected to rigorous cleaning processes to remove any impurities that could compromise the quality of the resin coating.
Once the base sand is prepared, it is introduced to the resin application stage. In this phase, a thermosetting resin, such as phenolic or furan resin, is uniformly mixed with the sand. This mixing process is crucial as it determines the even distribution of the resin across the sand particles. Commonly, the sand and resin mixture is achieved through a combination of mechanical mixers and hot air drying, which helps in ensuring that the resin adheres properly to each sand grain.
The curing process is another critical stage in the production of resin-coated sand. After the resin has been applied, the mixture undergoes a curing phase where heat is applied, typically using hot air or infrared radiation. This heating causes the resin to cure and form a strong bond between the sand grains, significantly enhancing the strength and durability of the resulting material. Cured resin-coated sand exhibits excellent collapse characteristics, making it well-suited for complex mold shapes.
resin coated sand manufacturing process
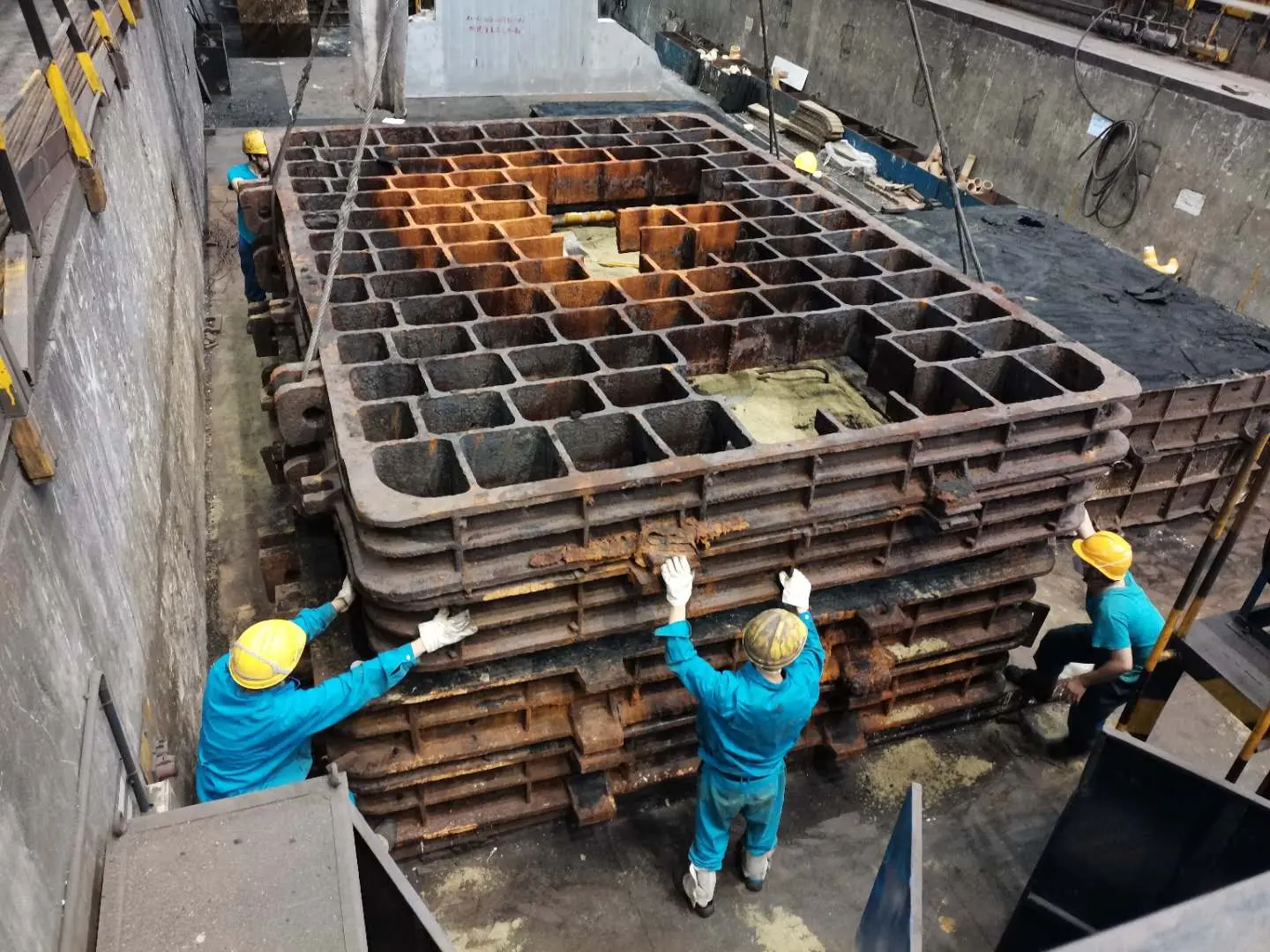
Following curing, the resin-coated sand is cooled and undergoes further processing, which may include screening and quality control checks to ensure it meets industry specifications. Screening is essential to eliminate any oversized particles and ensure a consistent grain size distribution. Quality control checks verify the physical and chemical properties of the sand to ensure it meets the required standards for casting applications.
The final stage involves packaging and distributing the resin-coated sand to customers. It is typically stored in bulk bags or containers, ready for delivery to foundries across various sectors, including automotive, aerospace, and construction.
Resin-coated sand provides several advantages over traditional molding materials. Its compatibility with automated molding processes allows for increased efficiency and precision in casting operations. Additionally, the enhanced surface finish and minimal defects in castings lead to improved product quality and reduced machining requirements.
In conclusion, the manufacturing process of resin-coated sand is a complex yet well-defined procedure that requires careful selection of materials, meticulous mixing, precise curing, and stringent quality control. The result is a high-performance product that has revolutionized the foundry industry. As demand for advanced casting solutions continues to grow, resin-coated sand remains an essential component in the quest for improved casting efficiency and quality. This innovative material not only contributes to the advancement of manufacturing technologies but also plays a pivotal role in shaping the future of castings across various industries.
Post time:Aug . 17, 2024 09:58
Next:Explore the Timeless Elegance of Heath Ceramics Sand Collection in Contemporary Design