The Importance of Resin Coated Sand Plants in Modern Foundries
In the world of foundry operations, the pursuit of quality and efficiency has led to the increasing adoption of resin coated sand (RCS) technology. Resin coated sand plants play a vital role in producing high-performance sand that meets the rigorous demands of metal casting processes. This article explores the significance of resin coated sand plants, their operational processes, and the advantages they offer to foundries.
Understanding Resin Coated Sand
Resin coated sand involves the coating of sand grains with thermosetting resins. This process enhances the sand's properties, making it more suitable for precise casting applications. RCS not only improves the surface finish of castings but also significantly increases the dimensional accuracy and mechanical strength of the final products.
The Process of Resin Coated Sand Production
The production of resin coated sand generally involves several key steps
1. Sand Selection High-quality silica sand is chosen as the primary raw material. The sand is screened and classified to achieve the desired grain size distribution, which is crucial for the casting process.
2. Coating Application The selected sand is then mixed with a specially formulated resin, usually a phenolic resin, under controlled conditions. This mixture is processed in a high-efficiency coating plant where the sand grains are evenly coated with resin. The application of heat may be involved to promote the curing of resin onto the sand grains.
3. Curing Process The coated sand undergoes a curing phase, which ensures that the resin hardens and bonds effectively to the sand. This step is critical as it determines the performance characteristics of the sand during the casting process.
4. Quality Control After the curing process, the resin coated sand is subjected to rigorous quality control measures. Tests for thermal stability, strength, and flowability are conducted to ensure that the product meets industry standards.
resin coated sand plant
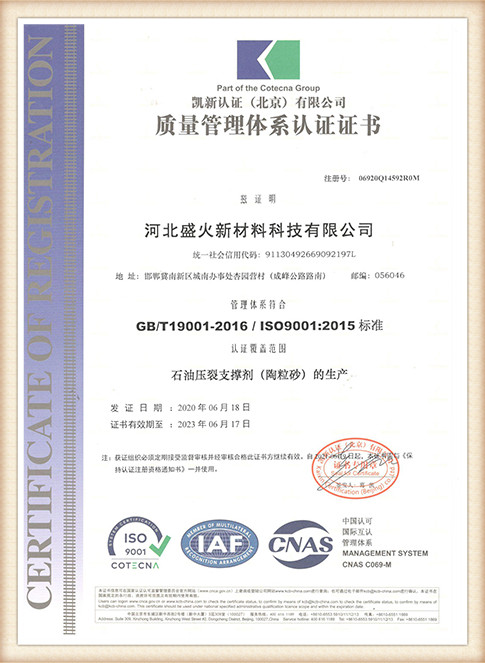
Advantages of Resin Coated Sand
The utilization of resin coated sand offers several advantages over traditional sand casting methods.
1. Enhanced Casting Quality The resin coating improves the surface finish of castings, reducing defects such as rough surfaces and dimensional inaccuracies. This results in less machining and finishing work, thereby saving time and costs.
2. Increased Strength and Durability RCS exhibits greater strength compared to uncoated sands, enabling the production of intricate and detailed castings that maintain their integrity during the casting process.
3. Improved Flow Properties The coating enhances the flowability of the sand, allowing for easier and more efficient filling of molds. This property is particularly beneficial for complex molds, where improved flow can lead to better filling and reduced risks of air entrapment.
4. Thermal Resistance Resin coated sands possess high thermal stability, which is crucial for withstanding the high temperatures involved in metal casting. This characteristic helps in minimizing sand erosion, ensuring longer mold life and better reclamation capabilities.
5. Sustainability Advanced RCS plants are increasingly designed to be environmentally friendly. Innovations in the production process aim to reduce waste and energy consumption, contributing to sustainable manufacturing practices.
Conclusion
Resin coated sand plants are integral to the modern foundry industry, providing essential materials that enhance the quality, efficiency, and sustainability of metal casting processes. As the demand for high-performance castings continues to grow, the role of RCS technology will undoubtedly become more prominent, driving further innovations and advancements in casting practices. Foundries that invest in resin coated sand will reap the benefits of improved product quality and operational efficiencies, positioning themselves competitively in the market.
Post time:Aug . 17, 2024 03:43
Next:Exploring the Growth and Vision of Golden Sands Development Initiatives