Advantages and Disadvantages of Sand Casting
Sand casting, one of the oldest manufacturing processes, involves the use of sand as the primary material for creating molds in which metal is poured to form various components. This technique has been utilized for centuries due to its versatility and simplicity. However, like any manufacturing method, it comes with its own set of advantages and disadvantages.
Advantages of Sand Casting
1. Cost-Effective One of the primary advantages of sand casting is its low cost. The materials required—sand, binder, and metal—are relatively inexpensive. Moreover, the setup costs are lower compared to other casting methods like investment casting. This makes sand casting an appealing option for producing large quantities of parts without substantial upfront investment.
2. Versatility Sand casting can be used to create a wide variety of metal components, making it highly versatile. It can accommodate a range of alloys, including iron, aluminum, and bronze. Additionally, the process is suitable for manufacturing small and large parts alike, as well as complex geometries that might be challenging for other casting techniques.
3. Large-Scale Production Sand casting is particularly effective for mass production, allowing manufacturers to produce large quantities of identical parts. This is especially beneficial in industries such as automotive and aerospace, where consistent quality and rapid production rates are paramount.
4. Recyclability The sand used in the casting process can be reused multiple times, which not only reduces waste but also minimizes the environmental impact of the manufacturing process. After casting, the sand can be reclaimed and treated for future use, making it a sustainable option in many cases.
5. Flexibility in Design Designers have greater flexibility when it comes to the shapes and sizes of parts they can create using sand casting. Since the molds are generally made from two or more halves, intricate designs and patterns can easily be achieved.
advantages and disadvantages of sand casting
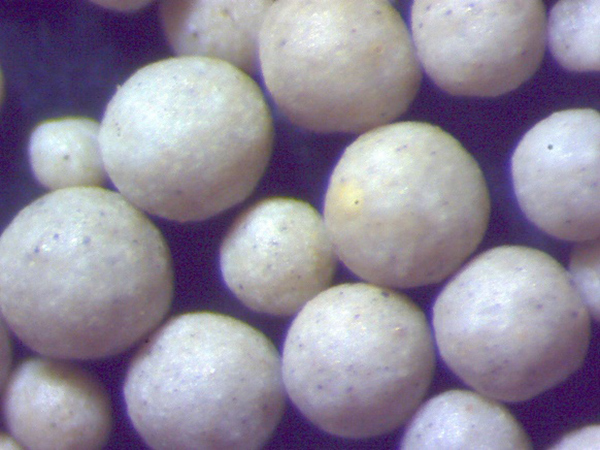
Disadvantages of Sand Casting
1. Surface Finish One of the notable disadvantages of sand casting is the surface finish of the final product. Parts made through this process typically have a rough exterior that may require additional machining or finishing processes to achieve the desired surface quality. This can increase production time and costs, especially for components that must meet tight tolerances.
2. Dimensional Accuracy While sand casting is suitable for creating complex shapes, it often falls short in terms of dimensional accuracy. The molds can change shape during the casting process due to thermal expansion, which can lead to variations in the final dimensions of the cast part. This may necessitate further adjustments in subsequent processes.
3. Labor-Intensive Sand casting can be labor-intensive, especially for small production runs. The process of preparing the molds and ensuring the right metal temperatures can require skilled labor, which adds to the overall cost and time of production.
4. Internal Defects Defects such as porosity and gas inclusions can occur during the sand casting process. These internal defects can compromise the mechanical properties of the finished part, leading to potential failures in critical applications.
5. Environmental Concerns While the sand itself is recyclable, the use of chemical binders and additives in the casting process can raise environmental concerns. Proper handling and disposal of these materials are crucial to mitigating any potential negative impact on the environment.
Conclusion
In summary, sand casting offers a number of advantages, including cost-effectiveness, versatility, and the ability to produce large quantities of complex parts. However, it also has its drawbacks, such as inferior surface finish, dimensional inaccuracies, and environmental concerns. Understanding these aspects is crucial for manufacturers when deciding whether sand casting is the right method for their specific needs and production requirements. Ultimately, sand casting remains a vital process in the manufacturing industry, continually adapting to meet modern demands.
Post time:Aug . 16, 2024 10:41
Next:Exploring the Benefits of Sanded Resin in Various Applications and Industries