Precision Sand Casting A Deep Dive into an Essential Manufacturing Process
Precision sand casting is a widely utilized manufacturing technique known for its capability to produce intricate metal components with high dimensional accuracy and excellent surface finish. This method is popular across various industries, including automotive, aerospace, and heavy machinery, primarily due to its adaptability and cost-effectiveness in creating complex shapes and sizable parts.
The Fundamentals of Sand Casting
At its core, sand casting involves creating a mold from a sand-based mixture. The process begins with the preparation of a mold, which typically consists of two halves the cope (upper half) and the drag (lower half). The sand is mixed with a binding agent, usually clay, and water to facilitate shape retention. This mixture is then packed into a mold box, where it is compacted around a pattern that embodies the final component's shape.
Once the mold is formed, the pattern is removed, creating a cavity into which molten metal will be poured. The type of sand used plays a crucial role in the process. Silica sand is the most common, but there are various other types that can be used to achieve desired properties such as permeability and strength.
Advantages of Precision Sand Casting
Precision sand casting offers several advantages over other manufacturing processes. One of the most significant benefits is its versatility; complex geometries can be produced without the need for expensive tooling, making it an attractive option for both small and large production runs. The method is particularly advantageous when producing large parts, as it can accommodate varying sizes and weights efficiently.
Another key advantage is the cost-effectiveness of sand casting. The materials required for molds—mainly sand—are relatively inexpensive compared to other casting materials. This leads to lower overall production costs, especially for low-to-medium volume runs. Furthermore, the ability to reuse the sand after casting reduces material waste and contributes to sustainability initiatives within manufacturing.
Precision in sand casting is achieved through advanced techniques such as the use of computer-aided design (CAD) and computer-aided manufacturing (CAM). These technologies allow manufacturers to create highly detailed patterns that translate into precision mold making, resulting in components that meet specific tolerances and intricate details.
precision sand casting
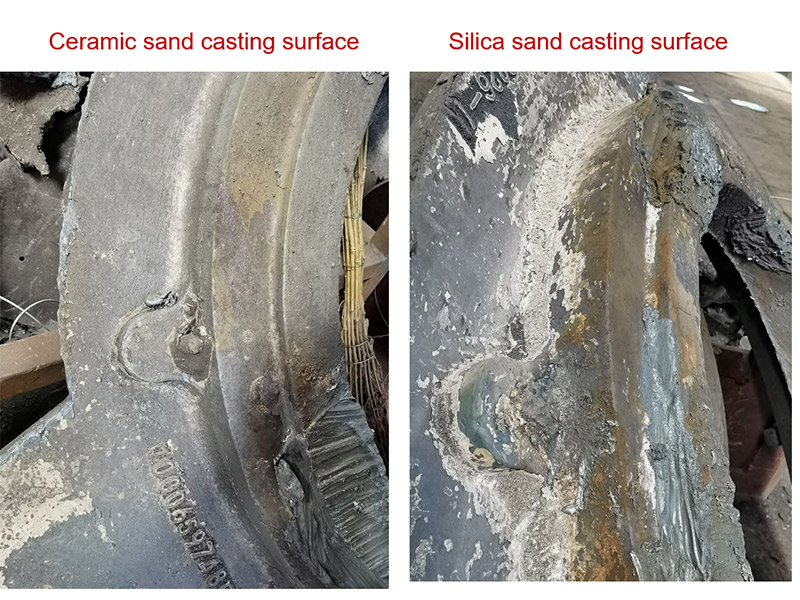
The Role of Technology
The evolution of technology has significantly enhanced the accuracy and efficiency of precision sand casting
. Innovations such as 3D printing have introduced new possibilities for creating mold cores and patterns, which can significantly reduce lead times and improve the overall quality of the final product. Additionally, automated sand casting processes leverage robotics and artificial intelligence, which help in minimizing human error and maximizing production speed.Moreover, implementing real-time monitoring systems during the casting process ensures better control over variables such as temperature and pressure. This leads to higher yield rates and reduces the likelihood of defects in the finished products.
Challenges Faced in Precision Sand Casting
Despite its many advantages, precision sand casting does come with challenges. The quality of the final product is heavily influenced by the quality of the sand and the precision with which the mold is created. Sand that is too coarse may result in a rough surface finish, while excessive moisture can lead to defects such as sand inclusions. Furthermore, achieving the desired metallurgical properties requires careful selection and preparation of the metal alloys used in the casting process.
There are also concerns regarding environmental impact. While sand is plentiful, the extraction and processing of sand can lead to ecological disruption if not managed responsibly. Manufacturers are increasingly looking toward sustainable practices to mitigate these impacts.
Conclusion
In conclusion, precision sand casting remains a cornerstone of modern manufacturing, offering a combination of flexibility, cost-effectiveness, and precision that few other methods can match. As technology continues to advance, the capabilities of precision sand casting will undoubtedly expand, making it an even more valuable technique for producing high-quality components in an array of industries. Embracing innovation while addressing the challenges will ensure that this time-tested process will thrive in the years to come, meeting the demands of an ever-evolving marketplace.
Post time:Nov . 14, 2024 16:42
Next:resin with sand