Molding Sand for Metal Casting A Comprehensive Overview
Molding sand is a fundamental material used in the metal casting industry, playing a crucial role in shaping and forming metallic components. This article delves into the various types of molding sand, their properties, applications, and the advantages they offer in the metal casting process.
What is Molding Sand?
Molding sand, also known as foundry sand, is a mixture of sand, clay, and water, used to create molds for casting metals. Its primary purpose is to form a cavity into which molten metal is poured to create the desired shape. The composition of molding sand can vary significantly depending on the desired properties and the casting method being employed.
Types of Molding Sand
There are several types of molding sand, each designed for specific casting processes and requirements
1. Green Sand This is the most common type of molding sand, made from a mixture of silica sand, clay, and water. It retains moisture, which gives it its name. Green sand is popular due to its excellent molding qualities, ease of use, and cost-effectiveness.
2. Dry Sand Unlike green sand, dry sand has a lower moisture content, making it more rigid. This type is often used for casting high-precision components since it provides a smoother surface finish, but it requires more complex preparation and handling.
3. Synthetic Sand This type of sand is engineered using various industrial materials to enhance specific properties, such as strength and thermal stability. Synthetic sands can be tailored to meet the requirements of various casting processes, ensuring consistent quality.
4. Shell Sand Made by binding fine sand with a thermosetting resin, shell sand is used in the shell molding process. It allows for high detail and smooth finishes, making it ideal for complex shapes and intricate designs.
Properties of Molding Sand
The effectiveness of molding sand in casting applications depends on several key properties
molding sand for metal casting
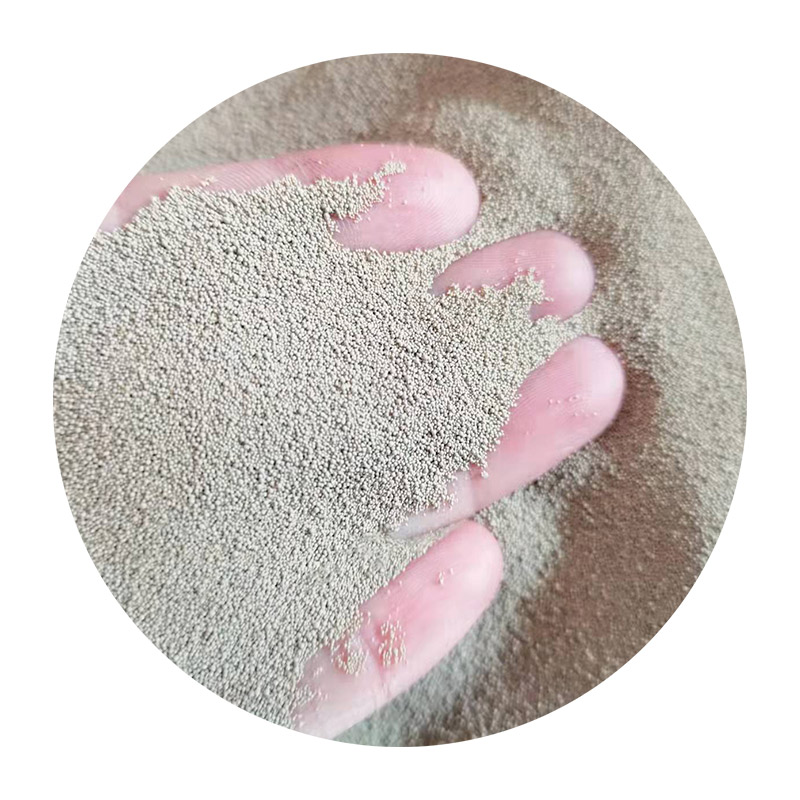
- Grain Size The size of the sand grains influences the surface finish and strength of the mold
. Fine grains provide smoother finishes, while coarser grains offer better strength.- Plasticity The ability of the sand to be molded and retain shape is crucial. Adequate plasticity ensures that the mold can be easily shaped and that it holds the form during metal pouring.
- Permeability The ability of the mold to allow gases to escape during casting is essential to prevent defects. Good permeability helps avoid blowholes and other casting imperfections.
- Thermal Stability Molding sand must be able to withstand the high temperatures associated with molten metals without breaking down or fusing with the metal.
Advantages of Molding Sand in Metal Casting
Using molding sand offers numerous advantages
- Cost-Effectiveness Molding sand is generally inexpensive and widely available, making it a preferred choice for many foundries.
- Versatility It can be used for a variety of metals and casting techniques, accommodating different shapes and sizes.
- Reusability Molding sand can often be reclaimed and reused, which reduces waste and associated costs.
- Ease of Use The preparation of molding sand is straightforward, allowing foundries to quickly adapt to different casting requirements.
In conclusion, molding sand is a pivotal material in the metal casting industry. Its various types, properties, and advantages make it an essential element in producing high-quality metal components. As technology advances, innovations in molding sand formulations continue to enhance the capabilities and efficiencies of metal casting processes.
Post time:Aug . 28, 2024 17:53
Next:Impression 3D de Sable - Transformez Votre Idée en Réalité