Lost Foam Casting An Innovative Manufacturing Technique
Lost foam casting (LFC) is a modern manufacturing technique that has revolutionized the way metal castings are produced. This process, which combines traditional casting methods with advanced technology, offers numerous advantages, including improved precision, reduced waste, and the ability to create complex shapes that would be difficult or impossible to achieve through other casting methods.
Process Overview
The lost foam casting process begins with the creation of a foam pattern, typically made from polystyrene. This pattern is an exact replica of the final casting and is coated with a thin layer of fine sand to create a mold. The key feature of lost foam casting is that this foam pattern is not removed from the mold after it has been created; instead, it is allowed to evaporate when molten metal is poured into the mold. As the liquid metal fills the cavity left by the evaporated foam, it solidifies and takes on the shape of the original foam pattern.
This method can be broken down into several steps
1. Pattern Creation The foam patterns are produced using computer-aided design (CAD) software, allowing for high precision and customization. 2. Mold Formation The foam patterns are coated with a refractory material to form a shell that can withstand the pouring of molten metal. 3. Metal Pouring Molten metal is poured into the mold, displacing the foam and creating the desired metal casting as the foam evaporates. 4. Cooling and Finishing Once the metal has cooled and solidified, the sand shell is removed, revealing the final casting that often requires minimal finishing.
Advantages of Lost Foam Casting
One of the primary advantages of lost foam casting is its ability to produce complex shapes and fine details. Traditional casting methods can struggle with intricate designs, often requiring additional machining processes to achieve the desired dimensions. In contrast, LFC allows manufacturers to create highly complex geometries without compromising on quality.
lost foam castings
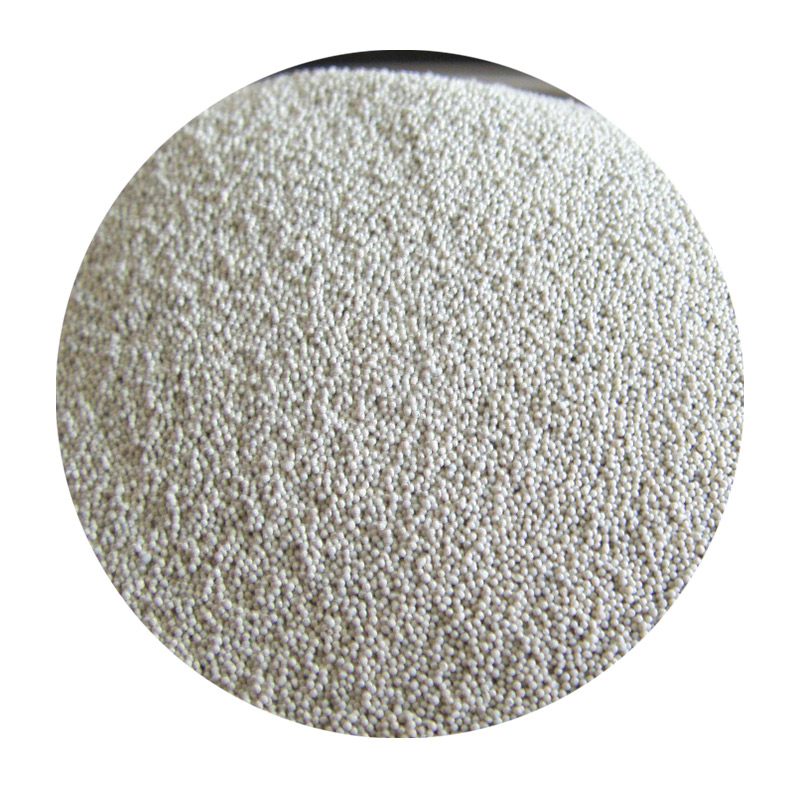
Another significant benefit is the reduction in waste material. Traditional casting usually involves machining away a significant amount of excess material to achieve the specified dimensions of the casting. In lost foam casting, the foam pattern evaporates, leaving little to no excess metal. This results in improved material utilization, which is not only cost-effective but also environmentally friendly.
Furthermore, lost foam casting can accommodate a wide range of materials, including ferrous and non-ferrous alloys. This versatility makes it an ideal choice for various industries, from automotive and aerospace to art and sculpture casting. Manufacturers can leverage LFC to meet specific engineering requirements, leading to innovative solutions across multiple sectors.
Applications of Lost Foam Casting
Lost foam casting has gained traction in several industries thanks to its adaptability and efficiency. In the automotive industry, LFC is used to manufacture engine components, exhaust manifolds, and transmission housings. These parts often require high precision and complex internal features, making lost foam casting an attractive option.
In aerospace, the ability to produce lightweight yet strong components is paramount. LFC facilitates the production of intricate parts that contribute to weight reduction while maintaining structural integrity, a crucial factor in aerospace engineering.
Additionally, artists and sculptors use lost foam casting to create detailed sculptures and artistic pieces. The ability to replicate fine details without the need for extensive finishing is a significant advantage in the art world.
Conclusion
Lost foam casting represents a significant advancement in casting technology, combining precision, efficiency, and versatility. By leveraging this innovative technique, manufacturers can produce high-quality metal castings that meet the demands of various industries, reduce waste, and foster creativity in artistic endeavors. As technology continues to evolve, the potential for lost foam casting to further impact manufacturing processes looks promising, paving the way for a new era of casting excellence.
Post time:Dec . 15, 2024 17:38
Next:Creating High-Quality Foundry Sand for Optimal Casting Performance