Steps in Sand Casting
Sand casting is one of the oldest and most versatile metal casting processes used in various industries today. It involves creating a mold from a sand mixture to pour molten metal into, resulting in a final product that can be finely detailed and produced in large quantities. The process of sand casting consists of several key steps, which are crucial for achieving high-quality castings. This article will outline these steps in detail.
1. Pattern Making
The first step in the sand casting process is creating a pattern. A pattern is a replica of the object to be cast and is typically made from materials such as wood, metal, or plastic. Patterns can be either solid or split into two halves, depending on the complexity of the design. In addition to the actual dimensions of the final product, patterns also require consideration for allowances, which account for the shrinkage of the metal as it cools and solidifies.
2. Molding
Once the pattern is ready, the next step is to create the mold. This process involves placing the pattern in a flask, which is a box-like structure that holds the sand mixture. The sand used in molding is typically a mixture of silica sand, clay, and water, which provides the necessary binding properties. The sand is packed tightly around the pattern to form a mold cavity. After the pattern is removed, the mold is left with an impression that will shape the final casting. It’s essential that the mold is free of defects since any imperfections will be transferred to the final product.
3
. Core MakingIn cases where the casting requires internal cavities or complex geometry, cores are needed. Cores are made from a similar sand mixture and are placed within the mold to create hollow sections in the casting. The size and shape of the core must be carefully designed to fit within the mold and maintain its position throughout the pouring process.
4. Pouring
steps in sand casting
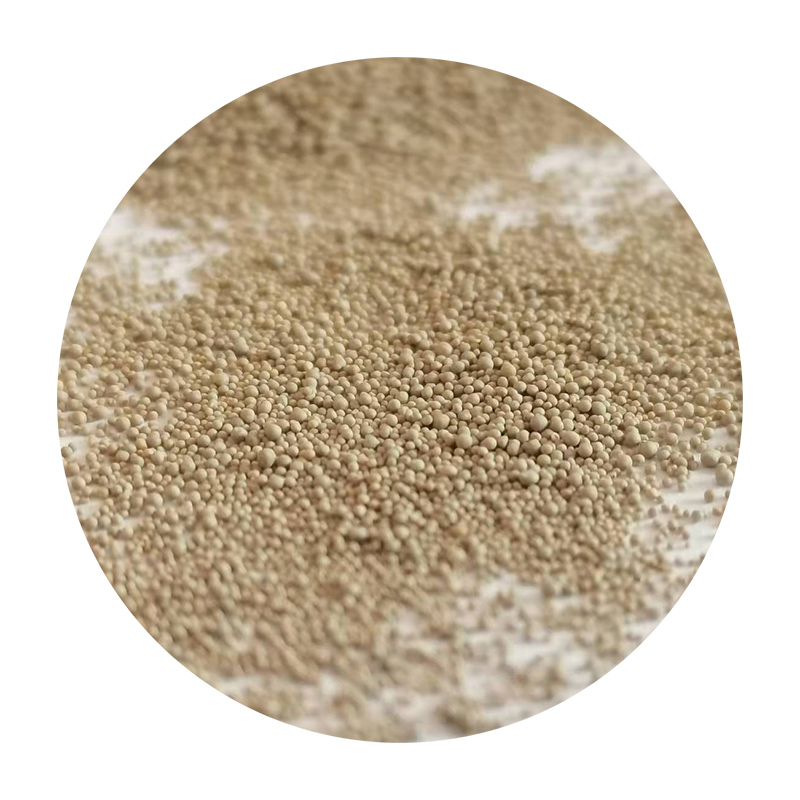
Once the mold and cores are prepared, the next step is pouring the molten metal. The metal is melted in a furnace and heated to a specific temperature, depending on the material being used. Pouring the molten metal into the mold must be done carefully to avoid any turbulence that could introduce defects. The metal fills the mold cavity and surrounds the core, if one is used.
5. Cooling
After pouring, the molten metal must cool and solidify. The cooling rate is essential as it affects the final mechanical properties of the casting. Depending on the size and thickness of the casting, this process can take anywhere from a few minutes to several hours. It's crucial to allow the metal to cool completely before proceeding to the next step to avoid cracking or warping.
6. Shakeout
Once the casting has cooled, the next step is shakeout, where the mold is broken apart to retrieve the casting. This is often done using mechanical devices, especially for larger castings. During this process, sand can be reclaimed and reused for future molds, making sand casting an efficient choice in terms of material usage.
7. Finishing
The final step in the sand casting process is finishing. This involves careful inspection of the castings to identify any defects, such as sand inclusions or surface irregularities. Castings often require additional machining, grinding, or polishing to achieve the desired surface finish and dimensional accuracy. Depending on the application, further post-casting treatments, such as heat treatment or coating, may also be applied.
In conclusion, sand casting is a comprehensive process that combines art and engineering. The careful execution of each step, from pattern making to finishing, is crucial in producing high-quality castings that meet specific tolerances and applications. Its versatility and cost-effectiveness continue to make sand casting a favored choice in many manufacturing sectors today.
Post time:Aug . 01, 2024 06:46
Next:A Step-by-Step Guide to Effectively Sanding Resin for a Smooth Finish