Components of Sand Casting
Sand casting is one of the oldest and most versatile manufacturing processes used to create metal parts with complex shapes. This method leverages the unique properties of sand, which provides both durability and flexibility, making it an ideal material for casting molds. Understanding the components of sand casting is crucial for anyone involved in manufacturing or metallurgy. This article will explore the primary components involved in the sand casting process.
1. Pattern
The pattern is a replica of the object to be cast, made from materials like wood, plastic, or metal. The creation of an accurate pattern is essential for ensuring the final cast product meets the desired specifications. Patterns can be categorized into several types solid patterns, split patterns, and complex patterns. Each type serves different purposes and can be customized based on the specific requirements of the casting project. Properly designed patterns take into account shrinkage allowances—metal contracts as it cools, and patterns must be oversized to compensate for this.
2. Mold Sand
Mold sand is a mixture of fine sand, clay, and water, which forms the mold into which molten metal is poured. The most commonly used sand is silica sand due to its excellent grain size and shape. The clay component acts as a binder, giving the sand its cohesive properties, while water helps to activate the clay, allowing for better molding and detail retention. Other additives might include chemicals that enhance the mold’s strength or improve its performance during the casting process.
Types of mold sand include green sand, which is moist and contains clay, and dry sand, which has been baked or heat-treated to improve its durability and strength. Each type has unique properties that make it suitable for different casting applications.
3. Core
components of sand casting
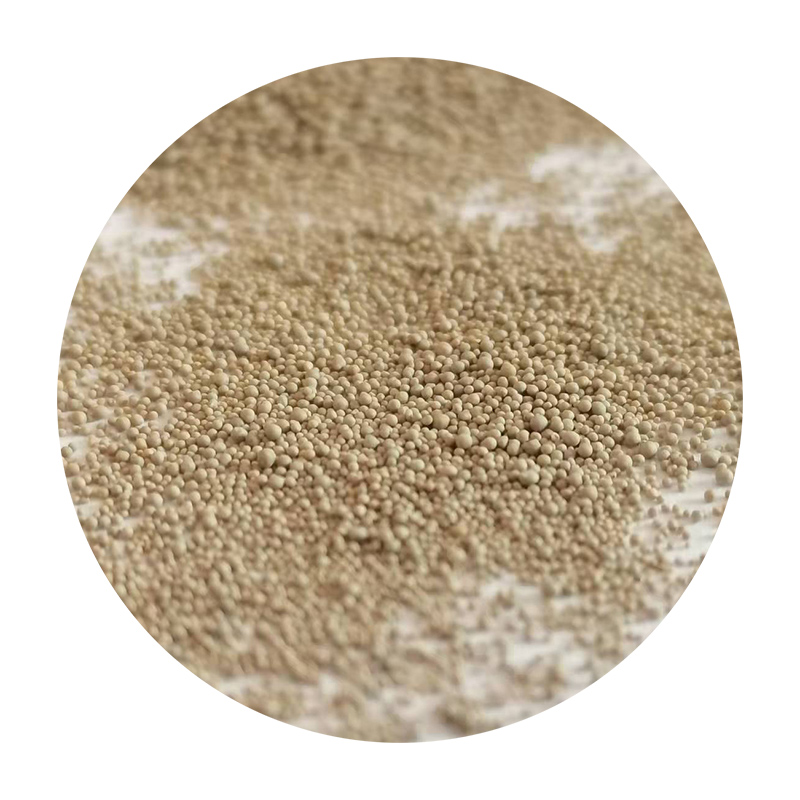
A core is used to create internal cavities and complex features in a casting. Cores are typically made from sand that is bonded together with a resin or other adhesive material. They can be placed inside the mold before the molten metal is poured, allowing for features that would otherwise be difficult to achieve. The design of cores must consider factors like strength, thermal stability, and ease of removal after the casting process. Additionally, cores can be produced using various techniques, including core blowing and core printing.
4. Melting Furnace
The melting furnace is where the metal is heated to its molten state before being poured into the mold. Various types of furnaces are used depending on the metal being cast, such as electric arc furnaces, induction furnaces, and cupola furnaces. The choice of furnace affects the efficiency of the casting process, the quality of the molten metal, and, ultimately, the properties of the finished product. Maintaining a consistent temperature is vital to avoid defects in the cast parts.
5. Pouring Equipment
Once the metal reaches the desired temperature, it is transferred to the mold. Pouring equipment can vary from simple ladles for manual pouring to sophisticated automatic pouring systems that minimize human error and improve efficiency. The pouring technique is also crucial; improper pouring can lead to issues like turbulence, which can introduce unwanted defects in the final casting.
Conclusion
In summary, the sand casting process comprises several key components, including patterns, mold sand, cores, melting furnaces, and pouring equipment. Each component plays a pivotal role in ensuring that the casting process produces high-quality, accurate parts. By understanding these components and their functions, manufacturers can optimize their casting processes, reduce production costs, and enhance the overall quality of their cast products. As industries continue to evolve, the principles of sand casting remain a cornerstone of metalworking, showcasing its enduring relevance in the manufacturing landscape.
Post time:Aug . 20, 2024 17:23
Next:Understanding the Characteristics and Applications of Resin Coated Sand in Industries