The Difference Between Sand Casting and Investment Casting
Casting is a pivotal manufacturing process that allows for the creation of complex metal parts. Two of the most common casting methods are sand casting and investment casting. Each of these methods has its unique attributes, benefits, and applications, which make them suitable for different production scenarios. Understanding the differences between sand casting and investment casting can help manufacturers choose the most appropriate technique for their needs.
Sand Casting
Sand casting is one of the oldest and most widely used casting methods. It involves creating a mold from a mixture of sand and a binding agent, usually clay. The process begins with forming a two-part mold. The pattern of the object to be cast is pressed into the sand to create a cavity. After the mold halves are assembled, molten metal is poured into the cavity to create the final part. Once the metal cools and solidifies, the sand mold is broken away to reveal the cast object.
One of the key advantages of sand casting is its versatility. It can accommodate a wide range of metal alloys, including aluminum, iron, and bronze, making it suitable for various applications across industries. Sand casting is also cost-effective for low to medium production volumes, as the patterns can be made from less expensive materials. Additionally, sand molds can be reused, further reducing costs over time.
However, sand casting does have its limitations. The finish of sand-cast parts tends to be rough, which may require additional machining to achieve a smoother surface. The accuracy and detail of the casts are also lower compared to other methods. For intricate designs or components requiring high dimensional accuracy, sand casting may not be the best choice.
difference between sand casting and investment casting
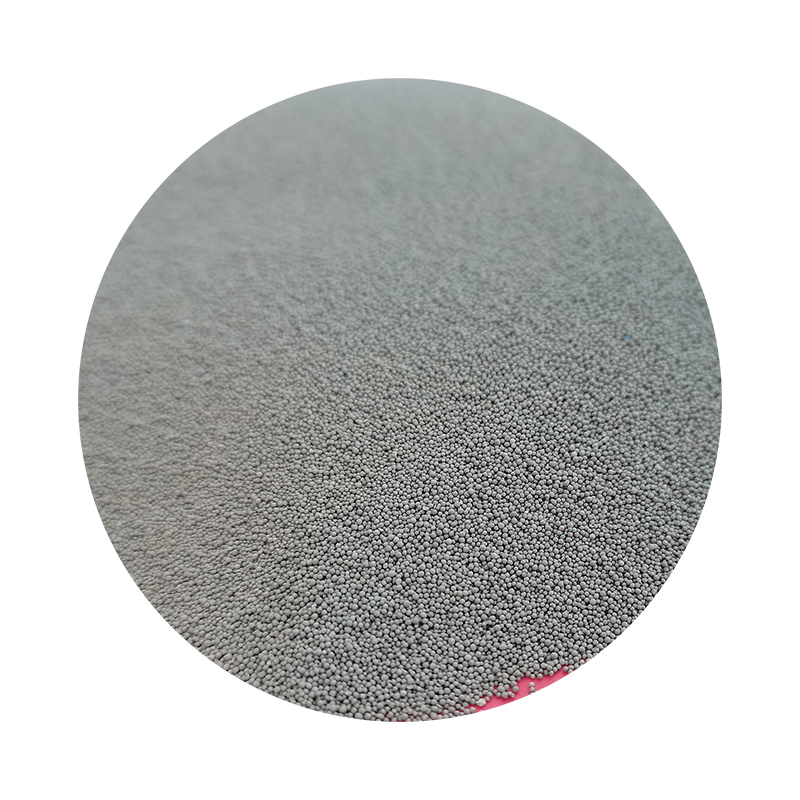
Investment Casting
Investment casting, often referred to as lost-wax casting, is a more precise method used to create complex shapes and fine details. The process starts with a pattern made from wax or a similar material. This pattern is coated in a ceramic shell, which is then heated to harden the shell and melt away the wax, leaving a precise mold cavity. Once the mold is ready, molten metal is poured in to produce the desired part.
One of the major advantages of investment casting is its ability to produce parts with high precision and excellent surface finishes. This method is particularly beneficial for applications that require intricate designs, such as aerospace components, medical devices, and jewelry. Investment casting also allows for the production of thinner walls and complex geometries that would be challenging with sand casting.
However, investment casting is generally more expensive than sand casting due to the intricate mold-making process and the materials involved. It’s most economical for high-volume production runs, and the initial setup costs can be prohibitive for smaller batches. Additionally, the time required for producing the ceramic molds can extend the overall lead time compared to sand casting.
Conclusion
In summary, both sand casting and investment casting play crucial roles in the manufacturing industry, each serving distinct purposes based on their characteristics. Sand casting is ideal for larger, simpler parts and is cost-effective for lower volumes, whereas investment casting excels in precision and complexity, making it suitable for high-value applications. When choosing between the two methods, manufacturers must consider factors such as production volume, material requirements, design complexity, and cost-effectiveness to determine which casting process aligns best with their project goals. Ultimately, the choice between sand casting and investment casting will depend on the specific requirements of the application and the desired outcomes.
Post time:Aug . 09, 2024 20:20
Next:Innovative Techniques in Sand Casting for Enhanced Foundry Efficiency and Product Quality