Investment Casting Sand An Integral Component in Precision Metal Casting
Investment casting, also known as lost-wax casting, is a sophisticated manufacturing process widely used for creating complex metal parts with high precision and excellent surface finish. One crucial element of this process is the selection of the appropriate casting sand. This article delves into the various types of investment casting sand, its properties, and its importance in the investment casting process.
The Role of Sand in Investment Casting
In investment casting, the mold is created by coating a pattern, often made of wax or another material, with a refractory material that forms the mold cavity. While traditional sand casting employs sand as the primary mold material, investment casting often uses different materials due to the need for high-precision and intricate designs. However, sand still plays a vital role, especially in the initial pattern creation and coating processes.
Types of Investment Casting Sand
1. Silica Sand The most commonly used type of sand in various casting processes, silica sand is composed mainly of silicon dioxide and is inexpensive and readily available. However, its melting point is relatively high, which might limit its applications in certain high-temperature investment casting situations.
2. Zircon Sand This sand is derived from zirconium silicate and possesses excellent thermal stability, making it suitable for high-temperature applications. Zircon sand is also chemically inert, reducing the chances of contamination during casting, which is a critical factor in producing high-quality parts.
3. Chromite Sand Known for its high thermal conductivity and resistance to thermal shock, chromite sand is suitable for producing high-strength molds. Its use can be particularly beneficial when casting metals with high melting points like steel and high-alloy materials.
4. Ceramic Sand This type of sand is engineered from fine particles of ceramics. It has excellent high-temperature stability and can provide superb surface finishes. Ceramic sand is often used in investment casting for producing intricate designs and thin-walled sections, which require precise dimensional control.
investment casting sand
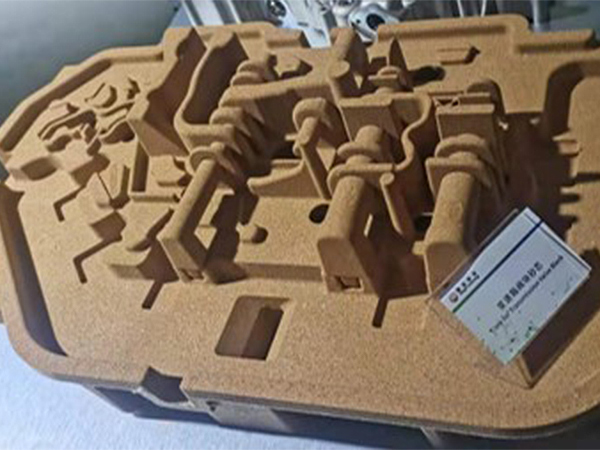
Properties of Ideal Investment Casting Sand
When selecting sand for investment casting, several properties must be considered to ensure optimal performance during the casting process
- Thermal Stability The sand must withstand high temperatures without breaking down or affecting the integrity of the mold.
- Refractoriness High refractoriness ensures that the sand does not melt or deform under the intense heat of molten metal.
- Grain Size and Shape The particle size and shape of the sand influence the mold's surface finish and the ease of mold removal after casting. Finer grains can provide better detail but may be more challenging to work with, while coarser grains are easier to handle but can result in a rougher surface finish.
- Chemical Purity The sand should be free of impurities that can react with the molten metal or affect the quality of the cast part. This is particularly crucial in investment casting, where even small impurities can lead to defects.
Importance of Investment Casting Sand
The selection of the right investment casting sand can significantly impact the overall casting process, influencing factors such as mold strength, thermal conductivity, and surface finish. High-quality sand contributes to the production of complex parts that require tight tolerances and a superior surface finish, making it essential in industries ranging from aerospace to medical device manufacturing.
In conclusion, while investment casting primarily utilizes refractory materials for creating molds, the choice of casting sand plays a significant role in the process. Understanding the types and properties of investment casting sand is vital for manufacturers aiming to produce high-quality parts efficiently. As the demand for precision-engineered components continues to grow, the importance of investing in the right materials, including casting sand, is more critical than ever.
Post time:Dec . 26, 2024 09:52
Next:3d printing for sand casting