Lost Foam Sand Casting A Comprehensive Overview
Lost foam sand casting is an innovative and highly efficient manufacturing process that combines the best aspects of traditional sand casting with the unique advantages of foam patterns. This technique has gained popularity in various industries, including automotive, aerospace, and artistic casting due to its ability to create complex shapes and reduce material waste.
At its core, lost foam casting involves creating a model (or pattern) out of expanded polystyrene (EPS) foam, which is then coated with a refractory material. Once the coating hardens, the foam pattern is placed in a mold box filled with sand. When molten metal is poured into the mold, the heat causes the foam to vaporize, leaving behind an impression that matches the desired final product. This technique can be particularly advantageous when making intricate designs or components that are difficult to achieve with conventional methods.
One of the primary benefits of lost foam sand casting is its ability to produce highly accurate and detailed castings. The foam pattern allows for the replication of fine details that would otherwise be lost in traditional methods. This makes it ideal for applications that require precise dimensions and intricate designs, such as engine components or decorative items.
Moreover, the lost foam process significantly reduces the need for secondary machining operations. Because the foam pattern is vaporized, it can create very exact tolerances, often reducing the post-casting machining by a substantial margin. This efficiency not only saves time but also lowers production costs, making it an attractive option for manufacturers looking to optimize their processes.
lost foam sand casting
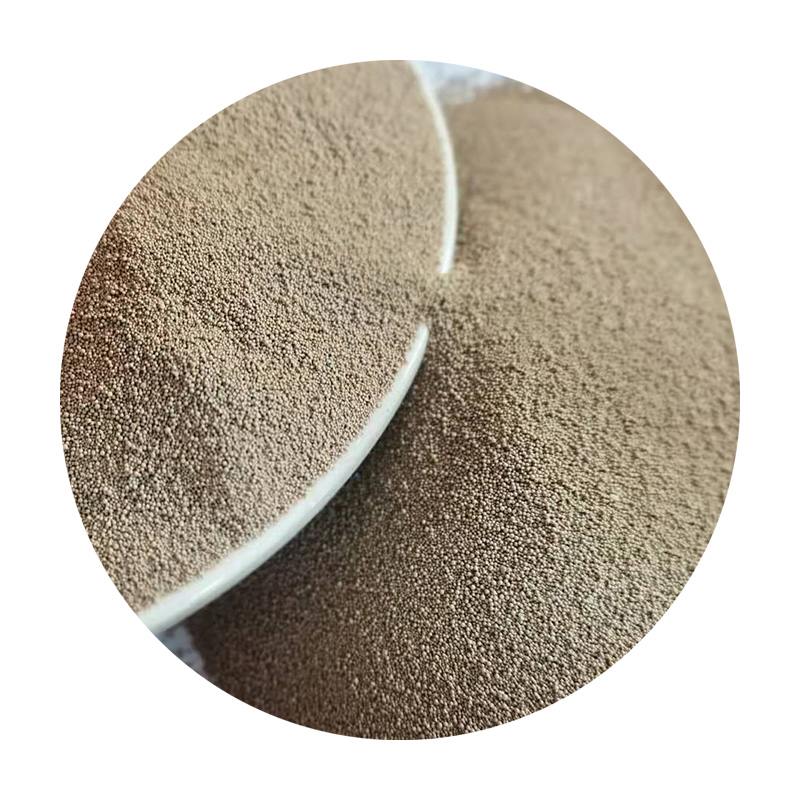
Another noteworthy advantage is the reduction of material waste. Traditional sand casting often requires additional metal to account for shrinkage and imperfections, leading to excess material that must be machined away. In contrast, lost foam sand casting allows for a more precise control over metal usage, minimizing scrap and contributing to a more sustainable manufacturing cycle.
In addition to its practical advantages, lost foam sand casting is often praised for its versatility. The method is suitable for a variety of metals, including aluminum, iron, and stainless steel, making it applicable to numerous industries. Its ability to accommodate different material types expands the possibilities for product development and innovation.
While the lost foam technique offers numerous benefits, it is not without its challenges. The initial setup costs for creating foam patterns and the necessary equipment can be significant. Furthermore, the process requires careful consideration of thermal management to ensure consistent results, as variations in temperature can affect the quality of the final casting.
In conclusion, lost foam sand casting represents a forward-thinking approach to manufacturing that combines environmental sustainability with precision and efficiency. Its ability to produce complex and detailed components with minimal waste makes it an appealing choice for modern industries. As technology continues to evolve, we can expect further innovations within the realm of lost foam casting, paving the way for even more advanced applications and continued growth in various sectors. Whether for mass production or bespoke creations, lost foam sand casting stands out as a method that embraces the challenges of today’s manufacturing landscape.
Post time:Aug . 16, 2024 20:21
Next:Procedure for Sand Casting Process Explained in Detailed Steps