3D Printing and Sand Casting Revolutionizing Manufacturing Processes
In recent years, the integration of additive manufacturing technologies, particularly 3D printing, with traditional manufacturing techniques has heralded a new era in various industries. One such innovative synergy is the combination of 3D printing with sand casting, a method that has been utilized for centuries to produce metal parts for a variety of applications. This convergence not only enhances efficiency and accuracy but also paves the way for more sustainable production methods.
The Basics of Sand Casting
Sand casting is a casting process that involves creating a mold from sand, into which molten metal is poured. This ancient technique allows for the production of complex shapes, making it a popular choice for industries such as automotive, aerospace, and art. The process typically involves several steps creating the pattern, preparing the sand mold, pouring the metal, and finally, cleaning and finishing the cast part. However, traditional sand casting comes with its set of challenges, including longer lead times, high material waste, and limitations in design flexibility.
The Role of 3D Printing
3D printing, or additive manufacturing, has transformed how products are designed and produced. This technology allows for the layer-by-layer construction of objects from a digital model, offering unprecedented design freedom and rapid prototyping capabilities. The marriage of 3D printing with sand casting primarily manifests in the creation of sand molds and cores directly using 3D printing technologies.
Enhancing Sand Casting with 3D Printing
The integration of 3D printing into the sand casting process yields numerous advantages
1. Rapid Prototyping Traditional mold-making techniques can take weeks to finalize. With 3D printing, sand molds can be generated in days, significantly reducing lead times and accelerating product development cycles.
3d printing sand casting
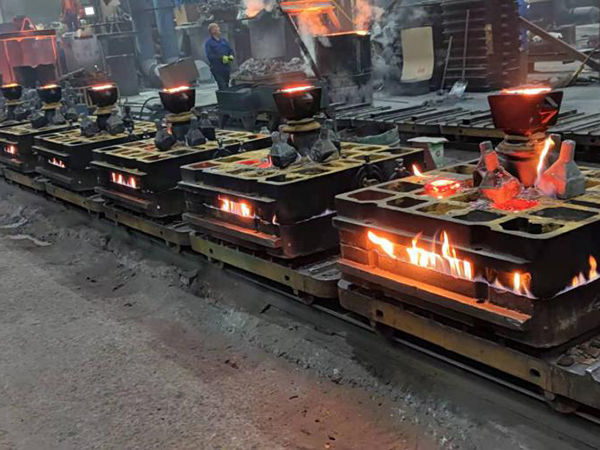
2. Design Flexibility 3D printing enables designers to create highly complex and intricate patterns that would be impossible or prohibitively expensive to achieve with conventional methods. This flexibility opens the door to innovative designs, optimizing performance in applications such as lightweighting in the aerospace industry.
3. Reduced Material Waste Traditional sand casting often leads to a substantial amount of wasted material. By using 3D-printed sand molds, manufacturers can minimize waste, as the process allows for just-in-time production and more efficient use of materials.
4. Cost Efficiency While the initial investment in 3D printing technology can be significant, the long-term savings from reduced material costs, faster production times, and lower labor expenses can greatly enhance overall profitability.
5. Customization With the ability to quickly change digital designs, manufacturers can easily cater to custom orders without the need for extensive re-tooling, making small batch productions or bespoke items more feasible.
Challenges and Future Prospects
Despite the numerous benefits, the integration of 3D printing in sand casting is not without its challenges. Issues such as the strength of printed materials and the required heat resistance for molten metal remain critical areas for development. Additionally, the industry must address quality control and standardization of 3D-printed molds to ensure reliability.
Looking ahead, as technologies advance and the adoption of 3D printing continues to rise, the traditional landscape of sand casting is likely to evolve significantly. Research and development will focus on improving printing materials and methods while developing new applications across various sectors, from automotive to medical devices.
In conclusion, the fusion of 3D printing and sand casting represents a groundbreaking advancement in manufacturing, offering increased efficiency, enhanced design capabilities, and a pathway to more sustainable practices. As these technologies mature, they will undoubtedly reshape the future of production, driving innovation and competitiveness in an increasingly complex global market.
Post time:Aug . 13, 2024 03:24
Next:Exploring the Benefits and Applications of Resin Bound Sand for Sustainable Landscaping Solutions