3D Printing for Sand Casting Revolutionizing the Foundry Industry
In recent years, 3D printing technology has made significant strides in various industries, including aerospace, automotive, and medical fields. One area where its impact is particularly noteworthy is sand casting. Traditionally a labor-intensive and time-consuming process, sand casting is essential in producing metal parts and components. The integration of 3D printing into this process is revolutionizing the foundry industry by enhancing efficiency, flexibility, and the overall quality of castings.
The Traditional Sand Casting Process
Sand casting involves the creation of a mold from a pattern, typically made of metal or wood. This pattern is used to shape the sand mixture, allowing molten metal to be poured into the cavity and solidify into the desired shape. While effective, traditional methods can be cumbersome. Patterns can take a long time to create, require significant resources, and are subject to wear and damage over time. Additionally, limitations in design and material choices often hinder the production of complex geometries.
The Advent of 3D Printing
The introduction of 3D printing in sand casting offers a groundbreaking alternative to traditional molding techniques. By using additive manufacturing, patterns and molds can be created directly from digital files, allowing for extreme precision and customization. 3D printing allows for the production of complex shapes and intricate details that would be difficult, if not impossible, to achieve using conventional methods.
One significant advantage of 3D printing in sand casting is the reduction in lead time. With traditional processes, creating a mold can take days or even weeks. In contrast, 3D printing can produce molds within hours, drastically accelerating the production timeline. This speed is critical in industries where time-to-market is a vital competitive factor.
Reducing Material Waste and Costs
3d printing for sand casting
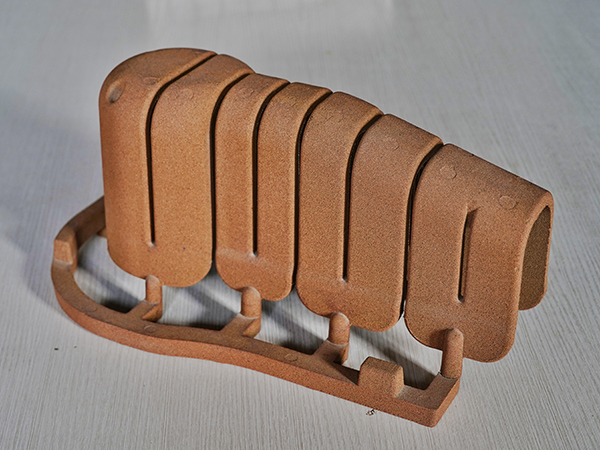
3D printing also contributes to sustainability in the foundry sector. Traditional sand casting often leads to significant material waste as excess sand must be cleaned and disposed of. In comparison, 3D printing employs a more efficient use of materials, minimizing waste and reducing overall costs. Since it allows for printing only the required geometry, manufacturers can optimize designs without the fear of excessive scrap material.
Customization and Flexibility
The ability to easily customize designs is another considerable benefit of incorporating 3D printing into sand casting. This flexibility is essential in industries such as aerospace and automotive, where specialized components are often required. Manufacturers can rapidly iterate designs based on specific performance or aesthetic requirements, accommodating client needs with unparalleled agility. Furthermore, 3D printing can enable the production of low-volume, high-complexity parts, making it ideal for prototype development.
Enhancing Quality and Performance
The precision offered by 3D printing also translates into enhanced quality of the final castings. Traditional patterns may lead to slight variances or imperfections, which can affect the integrity and performance of the cast product. In contrast, 3D printing ensures that the molds are crafted with exact dimensions, leading to higher accuracy in the final cast. As a result, components produced through this method often exhibit superior mechanical properties and surface finishes.
Conclusion
The integration of 3D printing technology into the sand casting process is reshaping the foundry industry by streamlining workflows, reducing costs, and enhancing the quality of castings. As manufacturers continue to explore the potential of additive manufacturing, we can expect further innovations that will push the boundaries of design and production capabilities. By embracing 3D printing, the foundry sector is not only improving its efficiency but also paving the way for a more sustainable future, reinforcing the critical role of advanced manufacturing technologies in today’s economy.
Post time:Aug . 06, 2024 11:51
Next:Best Places to Purchase Quality Foundry Sand for Your Casting Needs and Projects