3D Printed Sand Casting Patterns Revolutionizing the Foundry Industry
In recent years, the manufacturing sector has witnessed significant advancements due to the integration of additive manufacturing technologies. One particularly transformative development is the use of 3D printed sand casting patterns. This innovation is not only redefining traditional casting methods but is also offering solutions to long-standing challenges in the foundry industry.
Sand casting is one of the oldest and most widely used metal casting processes. It involves creating a mold from sand to shape molten metal, which then solidifies into the desired form. Traditionally, making molds is a labor-intensive process that requires considerable time and resources. The conventional method of creating patterns for these molds often involves the use of wood or metal, which can be expensive and time-consuming to produce, especially for complex designs.
3D Printed Sand Casting Patterns Revolutionizing the Foundry Industry
One of the most remarkable advantages of 3D printed sand casting patterns is the reduction in lead time. What traditionally took weeks can now be accomplished in a matter of days, allowing for faster production cycles and the ability to respond quickly to market demands. This agility is critical in industries where time-to-market is essential, such as automotive and aerospace. Manufacturers can innovate and iterate designs rapidly, testing new concepts before committing to traditional production methods.
3d printed sand casting patterns
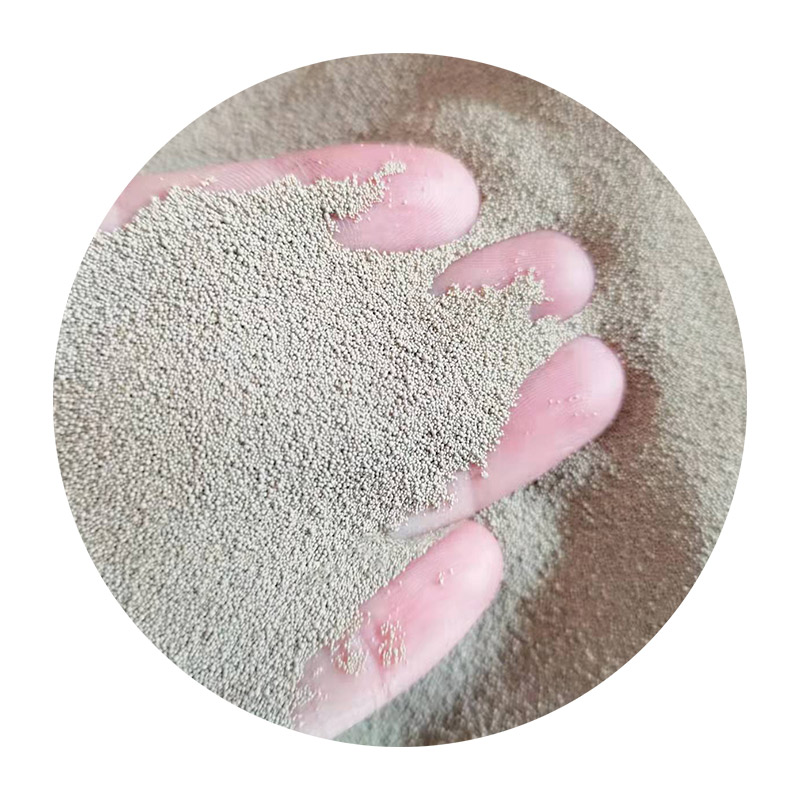
Moreover, 3D printing significantly reduces material waste. Traditional pattern-making often involves substantial waste, both from the raw materials used and from the machining processes required to achieve the final shape. In contrast, 3D printing allows for a near-net-shape production, minimizing excess material and optimizing the use of resources. This not only drives down costs but also enhances sustainability—an increasingly important consideration in modern manufacturing.
The use of 3D printed sand casting patterns also opens the door to customization. With the ability to produce bespoke patterns quickly and cost-effectively, manufacturers can cater to niche markets, creating unique products tailored to specific customer needs. This level of customization was previously impractical for many manufacturers, particularly those dealing with small batch sizes.
However, the transition to 3D printed patterns is not without challenges. The technology requires a skilled workforce capable of operating advanced printers and working with new materials. Additionally, the foundries must adapt their processes to integrate this disruptive technology effectively. Nonetheless, the advantages often outweigh these hurdles, prompting more companies to explore 3D printing as a viable pattern-making solution.
In conclusion, 3D printed sand casting patterns represent a revolutionary step forward in the foundry industry. By enhancing efficiency, reducing waste, and enabling customization, this technology is reshaping the landscape of metal casting. As innovations continue to emerge and the technology matures, we can expect to see even more transformative changes in manufacturing practices, paving the way for a more agile, sustainable, and efficient industry. The foundry of the future may very well be built layer by layer, with 3D printed sand casting patterns at the forefront of this evolution.
Post time:Aug . 12, 2024 15:32
Next:The Role of Sand in Enhancing the Durability of Ceramic Fire Bricks for High-Temperature Applications