An Overview of Cast Iron Sand Casting
Cast iron sand casting is a vital manufacturing process used to create complex metal components in various industries, including automotive, aerospace, and machinery. This method combines the traditional sand casting technique with the unique properties of cast iron, making it an effective choice for producing high-quality, durable parts.
The Process of Cast Iron Sand Casting
The sand casting process involves several essential steps. First, a mold is created using a mixture of sand and a binding agent, typically clay. This mixture is shaped into a mold cavity that will define the final shape of the cast part. The molds can be made using either green sand, which is moistened with water, or resin-bonded sand, which provides greater precision and can withstand higher temperatures.
Once the mold is prepared, molten cast iron is poured into the cavity. The casting temperature for cast iron generally ranges between 1200°C to 1450°C (2192°F to 2642°F), which ensures that the iron flows smoothly into the mold, filling all intricate details. After the iron cools and solidifies, the mold is removed, and the cast part is retrieved. This is often followed by additional finishing processes, such as grinding or machining, to achieve the desired surface finish and dimensions.
Advantages of Cast Iron in Sand Casting
Cast iron is an alloy of iron with carbon and other elements, usually silicon. This composition gives cast iron a range of beneficial properties, making it an excellent material for sand casting. One of the primary advantages of using cast iron is its excellent castability, meaning it can flow well into complex mold designs and retain fine details. Furthermore, cast iron exhibits good wear resistance, making it ideal for parts subjected to high stress and abrasion.
Another significant advantage is the ability to achieve a high degree of dimensional accuracy. With advances in sand casting techniques, manufacturers can produce parts with tighter tolerances than ever before. This is crucial in applications where precision is paramount, such as in engine blocks or industrial machinery.
cast iron sand casting
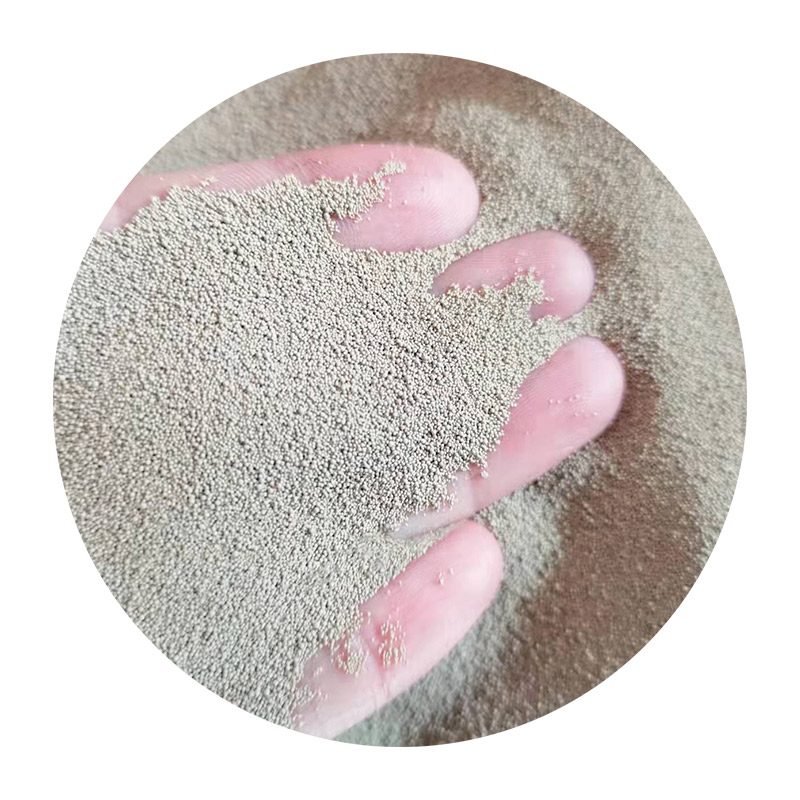
Applications of Cast Iron Sand Casting
The versatility of cast iron sand casting allows for a wide variety of applications across different sectors. In the automotive industry, cast iron is commonly used in the production of engine blocks, cylinder heads, and exhaust manifolds due to its strength and thermal conductivity. In the construction and machinery sectors, cast iron components like pump casings, machine bases, and various fittings are prevalent.
Moreover, cast iron sand casting has been effectively used in the production of artistic and architectural elements, including sculptures, railings, and decorative grills. The aesthetic appeal of cast iron, combined with its durability, makes it a popular choice for both functional and ornamental applications.
Environmental Considerations
As industries increasingly focus on sustainability, the environmental impact of manufacturing processes comes under scrutiny. Fortunately, cast iron sand casting can be adapted to be more eco-friendly. The use of reclaimed sand for mold making reduces waste, and advancements in recycling technologies enable the reuse of scrap metal, minimizing the environmental footprint of the overall process.
Conclusion
In summary, cast iron sand casting is a crucial manufacturing process that combines tradition with modern technology to produce high-quality, durable metal components. Its unique advantages make it a popular choice in various industries, while ongoing advancements promise to enhance its efficiency and sustainability. As the demand for intricate and resilient parts continues to grow, cast iron sand casting remains at the forefront of metal manufacturing solutions.
Post time:Aug . 13, 2024 08:16
Next:Different Techniques and Methods Used in Sand Casting Processes and Their Applications