Dry Sand Casting An Overview
Dry sand casting is a widely utilized metal casting process that leverages the unique properties of dry sand as a molding material. This technique, which has been around for centuries, plays a crucial role in producing intricate metal parts and components with excellent surface quality and dimensional accuracy. In this article, we will explore the intricacies of dry sand casting, its benefits, applications, and the process itself.
What is Dry Sand Casting?
In dry sand casting, the mold is created from a mixture of sand and a binding agent, specifically designed to hold its shape without the need for moisture. The sand is dried in an oven to remove any moisture content, resulting in a more stable and rigid mold. This method contrasts with green sand casting, where the mold is made with moist sand that contains clay as a binding agent.
The principal feature of dry sand casting is the use of high-strength, heat-resistant sand that allows for the production of high-quality castings with smooth surfaces. The dry sand mixture typically consists of silica sand and clay, which provides strength and improves the overall quality of the castings.
Advantages of Dry Sand Casting
Dry sand casting boasts several advantages over other casting methods
1. Superior Surface Finish The absence of moisture helps in achieving a finer surface finish, reducing the need for additional machining or finishing processes. 2. Dimensional Accuracy The rigid nature of dry sand molds minimizes dimensional changes during the casting process, ensuring high levels of accuracy in the finished product.
3. Flexible Design This method allows for the creation of complex shapes and intricate details, making it suitable for a wide range of applications.
5. Reduced Defects Dry sand casting tends to exhibit fewer defects such as sand inclusions or gas porosity, leading to robust castings.
dry sand casting
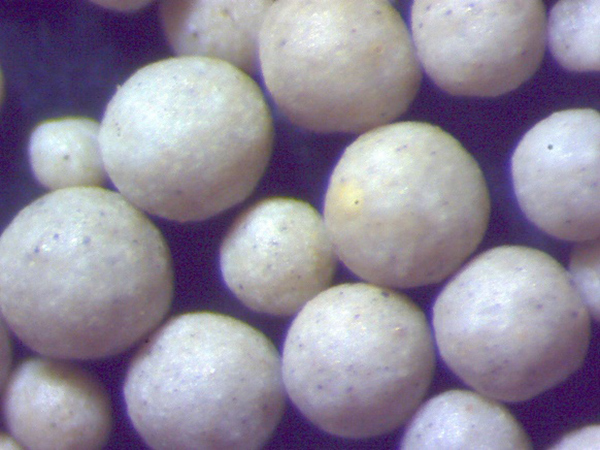
The Dry Sand Casting Process
The dry sand casting process involves several key steps
1. Pattern Preparation A pattern representing the desired final product is created, often from materials like metal, wood, or plastic.
2. Mold Making The dry sand mixture is compacted around the pattern to form a mold. This is typically done in two halves the cope (top half) and the drag (bottom half). After compaction, the mold is heated in an oven to eliminate any remaining moisture.
3. Core Creation If the casting requires internal features, cores made from dry sand are prepared and placed in the mold.
4. Pouring Once the mold is ready, molten metal is poured into the cavity created by the pattern. The heat from the molten metal solidifies the sand, forming a strong mold.
5. Cooling and Shakeout After the metal has solidified, the mold is allowed to cool. The mold is then opened, and the casting is removed.
6. Finishing The final step involves cleaning, machining, and finishing the casting to meet specific requirements.
Applications of Dry Sand Casting
Due to its versatility and quality, dry sand casting is employed in various industries, including automotive, aerospace, and manufacturing. Common applications include engine blocks, housings, components for machinery, and intricate parts for different devices.
In conclusion, dry sand casting represents a powerful technique in the field of metal casting. With its numerous advantages, ability to produce complex shapes, and high-quality outcomes, it remains a preferred method for manufacturers seeking reliability and precision in their casting processes. As technology continues to advance, further innovations in dry sand casting are likely to emerge, enhancing the capabilities and efficiencies of this time-tested method.
Post time:Aug . 13, 2024 22:47
Next:Understanding the Process and Techniques Involved in Sand Casting for Metal Fabrication