The Advantages of Sand Casting in Modern Manufacturing
Sand casting, one of the oldest and most versatile manufacturing processes, continues to play a crucial role in the production of metal components across various industries. This method involves creating a mold from sand and then pouring molten metal into the mold cavity to create the desired shape. Despite the advent of advanced manufacturing techniques, sand casting remains popular due to its numerous advantages, making it an essential consideration for any sand casting company.
Cost-Effectiveness
One of the primary benefits of sand casting is its cost-effectiveness. The materials needed to produce sand molds, such as silica sand and binders, are inexpensive and readily available. This is especially advantageous for small to medium-sized production runs where the initial investment in molds for other casting processes, like die casting, may not be practical. For a sand casting company, this means greater flexibility in meeting diverse customer demands without prohibitive costs.
Design Versatility
Sand casting allows for remarkable design flexibility. The method can accommodate a wide range of sizes and geometries, from small intricate parts to large heavy components. Additionally, complex designs with internal features can be easily achieved by using cores made from sand. This versatility makes sand casting an ideal choice for industries such as automotive, aerospace, and construction where unique components are frequently required.
Material Variety
Another significant advantage of sand casting is the ability to use a wide range of materials. Various metals, including cast iron, aluminum, brass, and steel, can be cast using this method. This diversity allows manufacturers to select the most suitable material for their specific application, balancing factors such as strength, weight, and cost. A sand casting company that specializes in multiple alloys can cater to a broader client base, enhancing their marketability.
sand casting company
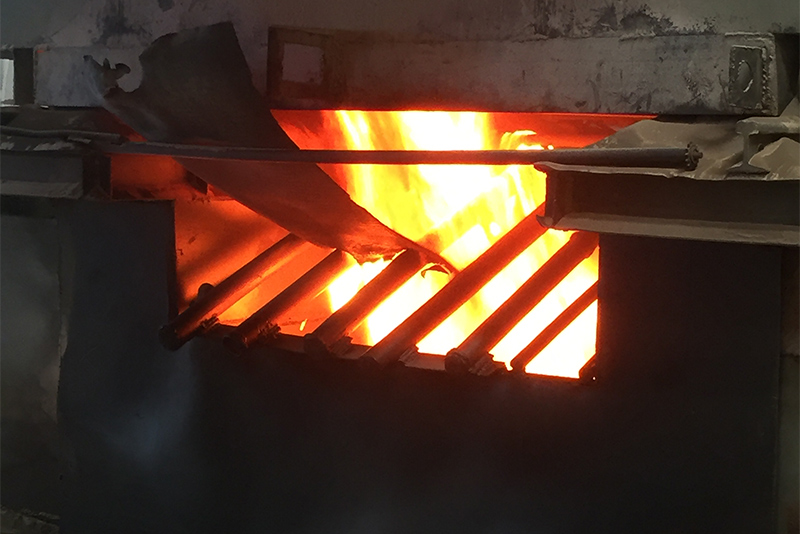
Minimal Waste
Sand casting is also beneficial from an environmental standpoint. The process generates minimal waste, as unused sand can be reclaimed and reused for future molds. Unlike some other manufacturing processes that may produce substantial scrap, sand casting can be very efficient in material usage. Moreover, with advancements in sand recycling technologies, companies are finding increasingly sustainable ways to operate within this framework.
Short Lead Times
In many cases, sand casting can offer shorter lead times compared to other methods. The preparation of the sand mold does not require extensive tooling, which can significantly reduce the time from design to production. For businesses requiring rapid prototyping or quick turnaround on orders, a sand casting company can be an ideal partner, providing efficient solutions that meet tight deadlines.
Skilled Workforce
Finally, the sand casting process requires a skilled workforce capable of handling the complexities involved in molding and pouring. The expertise of foundry workers is essential for ensuring high-quality outputs and consistent performance of the casting process. Companies that invest in training and developing their workforce often enjoy enhanced efficiency and product quality, reinforcing their reputation in the industry.
Conclusion
In conclusion, sand casting is an enduring manufacturing process that offers numerous benefits, including cost-effectiveness, design versatility, material variety, minimal waste, and short lead times. As industries continue to evolve, the flexibility and adaptability of sand casting ensure its relevance in modern manufacturing. Sand casting companies that harness these advantages can position themselves competitively in the market, meeting the diverse needs of their clients while contributing to sustainable manufacturing practices. With the right expertise and innovation, sand casting will undoubtedly continue to be a pillar of the manufacturing landscape for years to come.
Post time:Aug . 12, 2024 16:36
Next:Exploring the Benefits and Applications of Fine Casting Sand in Modern Foundry Techniques