Understanding Sand Casting and Its Benefits for Manufacturing
Sand casting, a time-honored method of metal fabrication, has played a pivotal role in industrial manufacturing for centuries. This versatile process involves creating metal parts by pouring molten metal into a sand mold. The popularity of sand casting stems from its simplicity, affordability, and the wide range of materials that can be utilized in the production of intricate shapes and sizes. In this article, we will explore the various aspects of sand casting and why it remains a preferred choice for many manufacturing companies.
The Process of Sand Casting
The sand casting process begins with the creation of a mold made from a mixture of sand, clay, and water. This mold is formed around a pattern, which is a replica of the desired final product. The pattern is typically made from metal, plastic, or wood, and its design often dictates the complexity of the final casting. Once the mold is ready, molten metal is poured into it, filling the void left by the pattern. After the metal cools and solidifies, the sand mold is broken away, revealing the finished part.
One of the remarkable advantages of sand casting is its ability to produce large and complex parts. This makes it especially valuable in industries such as automotive, aerospace, and machinery manufacturing, where components such as engine blocks, turbine housings, and large pump casings are common.
Advantages of Sand Casting
1. Cost-Effective Sand casting is often more economical than other metal forming processes. The materials used for molds are generally inexpensive, which is advantageous for both small batch production and high-volume manufacturing.
2. Flexibility in Design The sand casting process accommodates a wide range of designs, including intricate shapes that may be impossible to achieve with other methods. This flexibility allows designers and engineers to innovate without the constraints typically associated with different manufacturing processes.
sand casting company
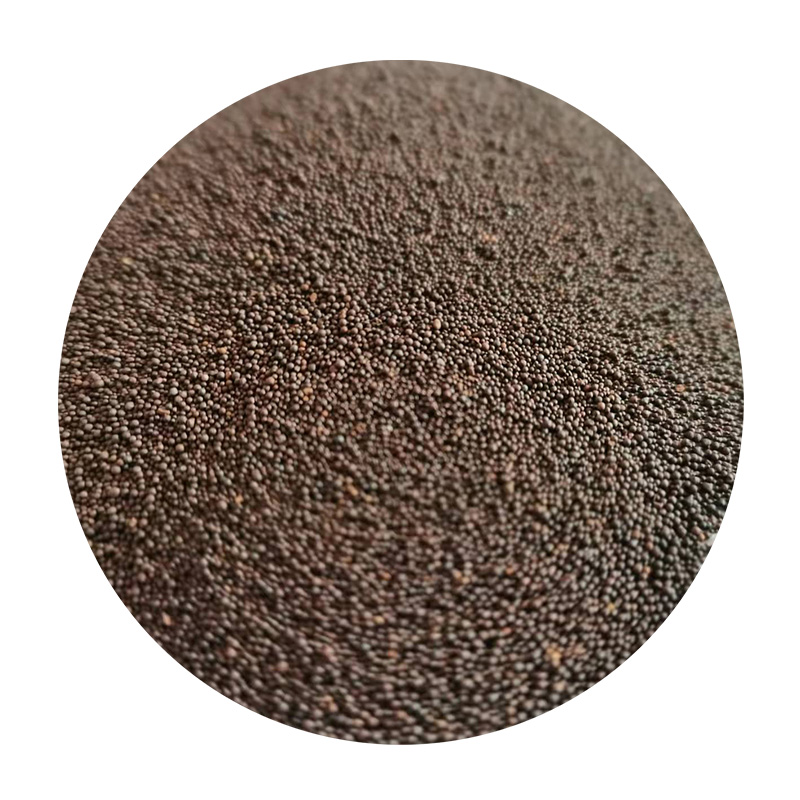
3. Material Variety Sand casting can be employed with various metals, including aluminum, iron, steel, and more. This versatility enables manufacturers to select the appropriate metal based on the performance characteristics required for the end product.
4. Size Capability Sand casting is uniquely suited to produce very large parts, making it indispensable for industries that require substantial components. Many other casting methods face limitations when it comes to size, but sand casting can accommodate much larger molds.
5. Ease of Modification The simple nature of sand molds allows for easy alterations. If a design change is needed, modifications can often be made without extensive reworking of the entire mold or production line.
Applications of Sand Casting
The applications of sand casting are vast and varied. In the automotive industry, it is commonly used to manufacture engine blocks, transmission cases, and various other components. The aerospace industry relies on sand casting for producing critical parts with complex geometries, such as turbine blades and housings. Additionally, manufacturers of industrial machinery, agricultural equipment, and even consumer goods utilize sand casting for producing their products.
Conclusion
In conclusion, sand casting continues to be a cornerstone of the manufacturing industry due to its cost-effectiveness, design flexibility, and capability to produce both small and large components. As technology advances, so too does the precision and efficiency of the sand casting process, enabling companies to meet the ever-evolving demands of modern manufacturing. By understanding the intricacies and advantages of sand casting, businesses can make informed decisions on their production methods, ensuring high-quality output that meets the needs of their customers. Whether for prototyping new designs or mass production of established parts, sand casting remains a reliable and effective solution.
Post time:Aug . 14, 2024 03:10
Next:Exploring the Benefits and Innovations of 3D Printed Sanding Machines for Enhanced Precision and Efficiency