Hard Sand Casting A Comprehensive Overview
Hard sand casting, also referred to as no-bake or air-set sand casting, is a well-established manufacturing process for producing complex metal parts with remarkable precision and surface quality. This method is distinguished from traditional green sand casting by utilizing a special binder that allows the sand to harden without the need for moisture. This article aims to provide a detailed understanding of hard sand casting, exploring its advantages, applications, and the overall process involved.
The Process of Hard Sand Casting
The hard sand casting process begins with the preparation of the sand mold. Silica sand is mixed with a chemical binder—often phenolic resin—which, when combined with a catalyst, sets the sand into a rigid form. The resulting mold is incredibly durable and can withstand the high temperatures associated with molten metals.
Once the mold is formulated, it is packed around a precision-engineered pattern, typically made from metal or wood. After the sand is compacted around the pattern, the binder is activated, causing the sand to harden. This creates a highly accurate mold cavity that replicates the dimensions of the desired final product.
After the mold has set, the pattern is removed, leaving behind a hollow cavity that perfectly outlines the part to be cast. The next step involves pouring the molten metal into the cavity. It's crucial to control the temperature and viscosity of the metal to ensure it flows seamlessly into the mold and fills all areas.
Once the metal has cooled and solidified, the mold is broken away, revealing the finished casting. This final product often requires minimal additional machining, thanks to the high precision achieved during the casting process.
Advantages of Hard Sand Casting
hard sand casting
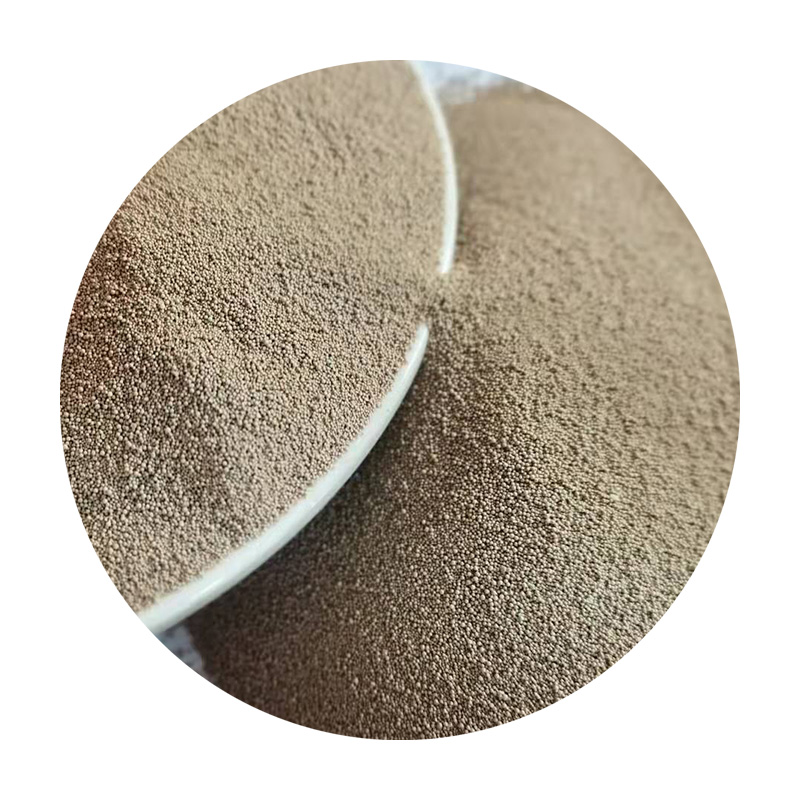
One significant advantage of hard sand casting is the exceptional surface finish it provides. The sand particles can produce a smoother surface compared to conventional sand casting methods. Additionally, the durability of the molds means they can be reused multiple times, helping to reduce production costs and waste.
Another benefit is the capability to create intricate shapes and features, which might be challenging to achieve through other manufacturing techniques. Hard sand casting is also suitable for producing larger parts, as the robust molds can withstand the stresses of heavier metals.
Applications of Hard Sand Casting
Hard sand casting is employed in various industries, each leveraging the unique benefits of this casting method. The automotive industry, for instance, uses it to create engine components, transmission housings, and other critical parts due to its precision and reliability. Similarly, the aerospace sector relies on hard sand casting for producing lightweight yet durable components that must endure extreme conditions.
Additionally, this method is popular in the production of industrial machinery and equipment. Companies require high-quality, complex components that must fit together seamlessly, making hard sand casting an ideal choice.
Conclusion
In summary, hard sand casting stands out as a versatile and efficient manufacturing technique capable of producing complex metal parts with high accuracy. Its advantages, including superior surface finish, mold durability, and the ability to create intricate designs, make it an essential process across various industries. As technology progresses, it is anticipated that hard sand casting will continue to evolve, further enhancing its application in modern manufacturing processes. By understanding this method, businesses can better leverage its capabilities to produce high-quality components that meet the demands of today's fast-paced industrial landscape.
Post time:Aug . 21, 2024 09:02
Next:Creating Unique Jewelry with Cerabead Techniques for Stunning Designs