Understanding Sand Casting A Comprehensive Overview
Sand casting is one of the oldest and most versatile foundry processes for manufacturing metal parts. It involves creating a mold from a mixture of sand, clay, and water, into which molten metal is poured to produce the desired shape. This method is widely used across various industries due to its cost-effectiveness and ability to produce complex geometries.
The Basics of Sand Casting
The sand casting process begins with the creation of a mold. This involves two main halves the cope (top half) and the drag (bottom half). The mold is created by packing sand around a pattern that is typically made from metal, plastic, or wood. The pattern defines the shape of the final product and is slightly larger than the actual component to account for the shrinkage that occurs during cooling.
Once the pattern is positioned within a frame, a mixture of sand, clay, and water, known as molding sand, is compacted around it. This mixture is essential for providing the necessary strength and flexibility to the mold. The sand grains are coated with clay and water, which helps bind them together. The preparation of the sand mixture can vary depending on the specific requirements of the casting process and the material being used.
The Mold Preparation Process
After the sand is packed around the pattern, the next step is to remove the pattern to reveal the mold cavity. This is done carefully to preserve the integrity of the mold. The mold halves are then cleaned and may be coated with a lubricant to facilitate the easy removal of the final cast.
In some cases, additional features such as cores may be added to create internal passages within the casting. Cores are made from sand and are placed in the mold before the two halves are joined. This allows for intricate designs and hollow sections that would be impossible to achieve with a solid pattern.
Pouring and Cooling
how sand casting works
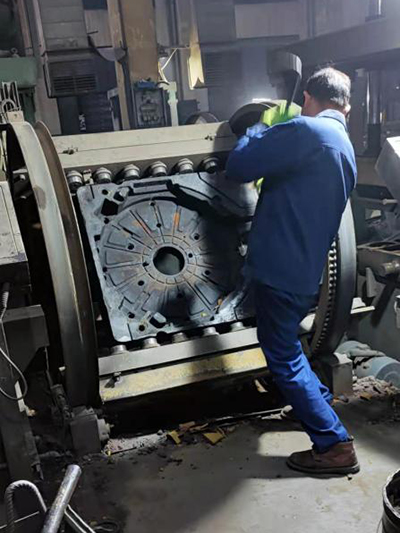
Once the mold is prepared, the next step is to pour molten metal into the cavity. The metal is typically heated to a temperature significantly above its melting point and is often done in a furnace. The metal is poured through a gating system, which directs its flow into the mold while managing any air that may need to escape.
After the molten metal is poured, it begins to cool and solidify. The cooling time can vary depending on the size of the casting and the material used. Once cooled, the sand mold is broken away, revealing the cast metal part. Care is taken during this phase to avoid damage to the newly formed component.
Finishing Touches
Once the casting is removed from the mold, it often requires finishing processes such as machining, grinding, or sanding to achieve the desired surface finish and dimensional accuracy. This step is critical, as castings typically have some roughness from the mold and may have extra material that needs to be trimmed or shaped.
Advantages of Sand Casting
Sand casting offers several benefits, making it a popular choice for manufacturers. Firstly, the process is relatively inexpensive, especially for low-volume production runs. The materials used (sand, clay, and water) are widely available and cost-effective. Additionally, sand molds can be reused multiple times, reducing waste and overall production costs.
Furthermore, sand casting allows for a high degree of design flexibility. Complex shapes can be created without the need for expensive tooling, making it ideal for prototypes and custom parts. It also accommodates a wide range of metals, including iron, aluminum, and bronze, making it suitable for diverse applications.
Conclusion
In summary, sand casting is a foundational technique in metalworking that combines traditional methods with modern applications. Its ability to produce intricate designs economically makes it indispensable in many manufacturing processes today. Whether for artistic sculptures or industrial components, sand casting remains a vital skill in the foundry industry.
Post time:Nov . 28, 2024 07:42
Next:Tips for Smoothing and Finishing Your 3D Printed Models