Understanding the Cost of Sand Casting
Sand casting, a versatile and widely used manufacturing process, involves creating metal parts by pouring molten metal into a mold made from sand. This method is particularly favored for its efficiency and ability to produce complex shapes. However, one common question among manufacturers and businesses is How much does sand casting cost? The answer is multifaceted and depends on several factors.
1. Material Costs
The primary component of sand casting is the raw materials, which includes the metal being cast (like aluminum, iron, or brass) and the sand used for the mold. The cost of the metal can fluctuate significantly based on market demand, specific alloys, and the volume required for production. For instance, aluminum is often less expensive compared to specialty alloys of steel. Additionally, high-quality sand or additives to enhance sand properties can contribute to production costs.
2. Mold Creation
Creating the mold is a critical step in the sand casting process, and it can add considerably to the overall cost. Molds are typically created from a mixture of silica sand, clay, and water. The complexity of the part being cast affects the mold design, with intricate designs necessitating more detailed mold production. Tooling costs will increase with the intricacy and size of the mold, as more precise and larger molds are more expensive to produce.
The cost per unit in sand casting can vary greatly depending on the production volume. For larger quantities, the overall cost per unit tends to decrease due to economies of scale. Small batch production, on the other hand, can lead to higher per-unit costs because the initial setup and mold costs do not change significantly with lower volumes. Companies must consider their production requirements when estimating costs.
how much does sand casting cost
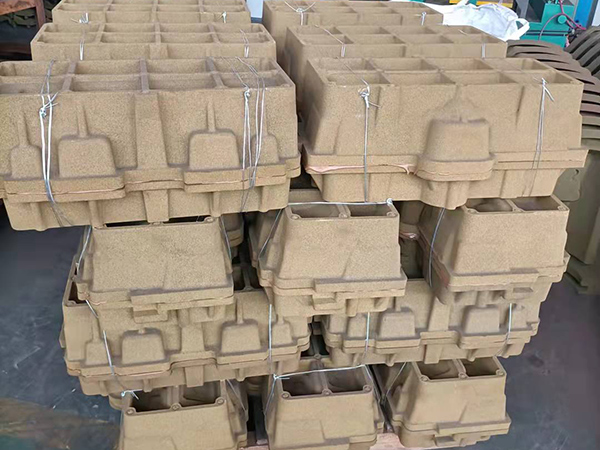
4. Labor Costs
Labor is another significant factor in the cost of sand casting. Skilled labor is required for the setup, operation of machinery, and quality control to ensure the cast parts meet specifications. Labor costs can vary by region, so businesses must take location into account when budgeting for sand casting projects.
5. Machining and Finishing
After the casting process, additional machining or finishing may be required to achieve the desired tolerances and surface quality. This can include processes like grinding, milling, or surface treatments, which all add to the total cost of production.
6. Quality Control and Testing
Ensuring the quality of the final product is crucial in manufacturing. Therefore, costs related to quality control, such as testing the integrity of the cast parts, can impact the overall expenditure. This is particularly true for industries such as aerospace and automotive, where precision and reliability are paramount.
Conclusion
In summary, the cost of sand casting is influenced by multiple factors, including material costs, mold creation complexity, production volume, labor, and post-processing requirements. On average, businesses might expect costs to range from a few dollars to several hundred dollars per unit, depending on specific requirements. For those considering sand casting, a detailed analysis of project needs and a clear understanding of all associated costs will foster informed decision-making and optimize budgeting.
Post time:Oct . 06, 2024 15:02
Next:sand casting benefits