The Importance of Metal Casting Sand and Its Availability for Sale
Metal casting is a crucial process in the manufacturing industry, allowing for the creation of intricate metal components used in various applications—from automotive parts to intricate machinery. One of the key elements in this process is the casting sand, which plays a vital role in shaping the molten metal into desired forms. This article explores the significance of metal casting sand, its types, and current availability for sale.
What is Metal Casting Sand?
Metal casting sand is a specially formulated material used in the casting process to create molds that hold molten metal. The primary function of casting sand is to provide a stable structure that can withstand high temperatures while allowing the escape of gases produced during metal solidification. The quality of the sand can significantly impact the final product, influencing the surface finish, dimensional accuracy, and overall strength of the cast metal.
Types of Metal Casting Sand
There are several types of metal casting sands available, each with distinct properties and uses
1. Silica Sand This is by far the most common type of casting sand. It is highly stable, has excellent thermal conductivity, and can withstand extreme temperatures. However, silica sand can produce harmful silica dust during processing, which requires appropriate safety measures.
2. Clay-Bonded Sand Often used for sand casting, this type blends sand with clay, which acts as a binder. This combination provides good mold strength and flexibility, making it suitable for intricate designs.
3. Resin-Bonded Sand This type involves a mixture of sand and resin, providing enhanced strength and lower moisture absorption. Resin-bonded sand molds are excellent for producing high-quality, smooth surface finishes.
4. Zircon Sand Known for its high melting point, zircon sand is often used when casting high-temperature metals and alloys. Its unique properties help in reducing the defects found in cast products.
metal casting sand for sale
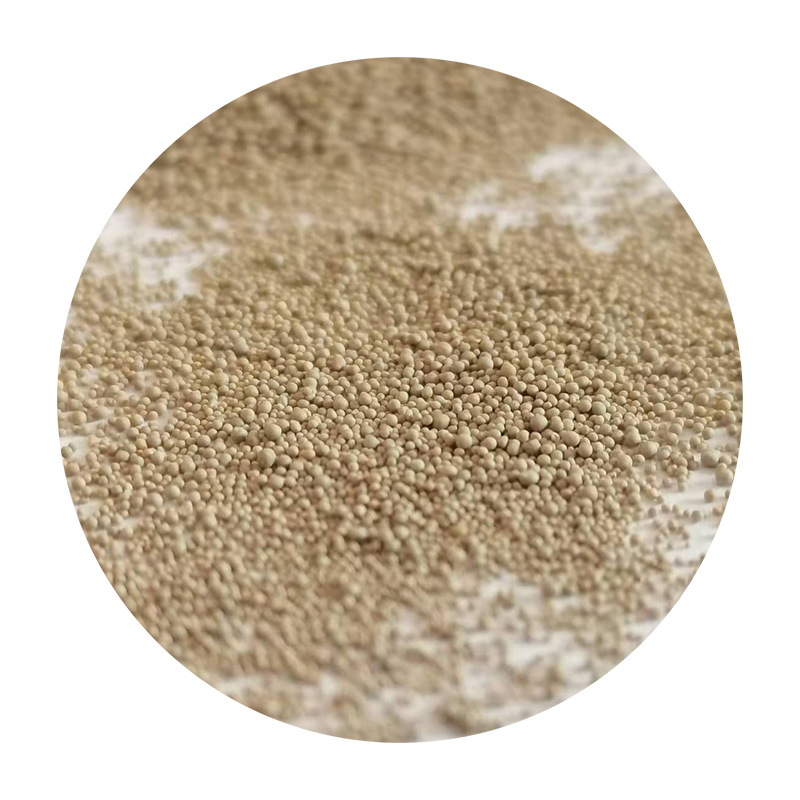
Availability of Metal Casting Sand for Sale
The demand for metal casting sand has consistently grown, thanks to the expansion of the manufacturing sector. Various suppliers and manufacturers offer different grades and types of casting sand tailored to specific needs. The availability of these sands is primarily dependent on geographical location, resource extraction processes, and market demand.
When looking for metal casting sand for sale, it’s crucial to consider several factors
- Quality and Specification Ensure the sand meets the required specifications for your casting process. High-quality sand can significantly reduce defects and improve the integrity of the final product.
- Supplier Reputation Opt for suppliers with a solid reputation in the foundry industry. Good suppliers often provide not only the product but also technical support and guidance on usage.
- Cost-Effectiveness While it may be tempting to go for the cheapest option, ensure that the casting sand offers a balance between cost and quality. Poor-quality sand can lead to higher rejection rates and increased costs in the long run.
- Sustainability With growing environmental concerns, consider suppliers who prioritize sustainable practices in their extraction and production processes.
Conclusion
In conclusion, metal casting sand is an indispensable component in the foundry industry, significantly impacting the quality and efficiency of the casting process. With various types of sand available for different applications, it is essential for manufacturers to choose wisely. As the demand for quality casting metals continues to rise, sourcing high-quality metal casting sand from reputable suppliers remains a priority for successful operations in the metal casting industry. Investing in the right type of sand not only enhances product quality but also streamlines production processes, ultimately leading to greater customer satisfaction and business success.
Post time:Jul . 26, 2024 07:03
Next:Exploring the Techniques and Benefits of Sand Casting in Modern Manufacturing Processes