The Importance of Metal Casting Sand in the Foundry Industry
Metal casting is a critical process in manufacturing, wherein molten metal is poured into a mold to create various components, from intricate parts to large machinery. One of the essential materials in this process is casting sand, which plays a vital role in ensuring the quality and efficiency of metal casting operations. In this article, we will delve into the significance of metal casting sand, its types, and its availability in the market.
What is Casting Sand?
Casting sand, often referred to as foundry sand, is a natural or synthetic material used to create molds for casting metals. The primary characteristic of casting sand is its ability to withstand high temperatures and provide the necessary strength and durability to maintain the shape of the mold during the casting process. The ideal casting sand has specific properties such as good flowability, thermal stability, permeability, and the ability to retain moisture without losing its shape.
Types of Casting Sand
There are several types of casting sand commonly used in the foundry industry
1. Silica Sand The most prevalent type of casting sand, silica sand is composed of silicon dioxide. It is favored for its availability, excellent thermal properties, and ability to withstand high temperatures. Silica sand is often coated with a resin or used in its natural form, depending on the casting process.
2. Clay-based Sand This type of sand contains fine clay particles that enhance the binding properties of the sand. Clay-based sand is known for its excellent mold strength and is often used for metalcasting applications requiring intricate patterns.
metal casting sand for sale
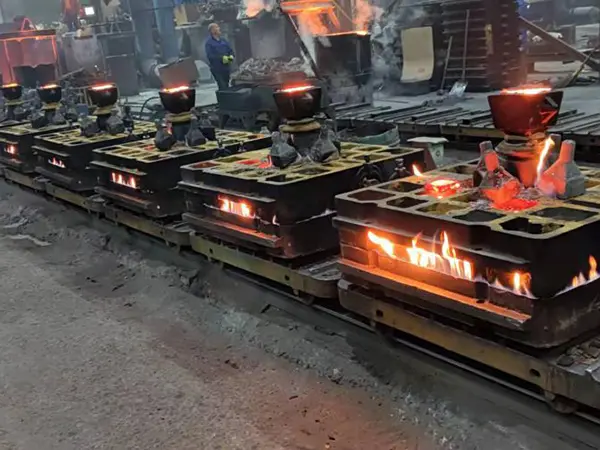
3. Green Sand Composed of silica sand mixed with a small amount of clay and water, green sand is prevalent in the foundry industry due to its recycling capability and cost-effectiveness. It is used for various metal casting processes, particularly in iron foundries.
4. Shell Sand This is a type of casting sand that is made up of fine grains and is coated with a thermosetting resin. When heated, the resin binds the sand together, creating a strong shell-like mold. Shell sand is particularly useful for high-precision casting requirements.
5. No-bake Sand As the name implies, no-bake sand does not require any baking or curing in the mold-making process. Instead, a chemical hardener is added to bond the sand. This type of sand allows for quicker mold production and is advantageous for large-scale casting operations.
The Market for Casting Sand
The production and sale of metal casting sand are integral to the foundry industry, which continues to evolve with advancements in technology and materials. Companies focusing on manufacturing and supplying high-quality casting sand are increasingly catering to the needs of foundries across the globe. With a growing emphasis on efficiency and reduced environmental impact, many suppliers are investing in innovative sand recycling and treatment methods.
Buyers looking for metal casting sand have access to various suppliers, both local and global. This availability allows foundries to select materials that best fit their specific casting needs. When purchasing casting sand, it’s essential to consider not just the price but also the quality and properties that will ensure successful casting outcomes.
Conclusion
Casting sand is an indispensable element of the metal casting process, significantly influencing the quality of the final products. Whether utilizing silica, clay-based, green, shell, or no-bake sand, foundries must choose the right type of casting sand to meet their operational requirements. As the demand for efficient and high-quality casting processes grows, the marketplace for metal casting sand continues to expand, providing foundries with various options to enhance their production capabilities. Investing in quality casting sand not only leads to better casting results but also contributes to the longevity and success of foundry operations.
Post time:Jul . 20, 2024 11:48
Next:Exploring the Key Benefits of Using Lost Foam Casting in Modern Manufacturing Processes