Sand Casting Procedure An Overview
Sand casting, also known as sand molded casting, is one of the oldest and most versatile casting processes used in manufacturing today. It involves creating a mold from sand to produce metal parts. This method is particularly favored for its simplicity, low cost, and ability to produce complex geometries. In this article, we will explore the detailed procedure of sand casting, highlighting each step involved in the process.
1. Pattern Making
The first step in the sand casting process is the creation of a pattern. A pattern is a replica of the object to be cast and is typically made from materials such as wood, metal, or plastic. The design of the pattern includes additional features like draft angles and allowances for shrinkage. These features ensure that the metal can easily flow into the mold cavity and that the final product accurately reflects the desired dimensions after solidification.
2. Molding
The next step is molding, which involves creating a mold cavity in the sand. The most common sand used is a mixture of silica sand, clay, and water, which allows for good compaction and strength. The pattern is placed in a molding box, and sand is packed around it. This is done either manually or through mechanical methods. Once the pattern is covered with sand, it is compacted to ensure that it holds its shape once the pattern is removed. After compaction, the pattern is carefully removed, leaving behind a hollow mold chamber.
3. Core Making
In many cases, the design of the part requires internal features or hollow spaces. This is where cores come into play. Cores are made from sand and are inserted into the mold to create these internal cavities. Like patterns, cores must also be designed with considerations for shrinkage and removal. Cores can be made using similar techniques as molds, often using a mixture of sand and a binding agent.
sand casting procedure
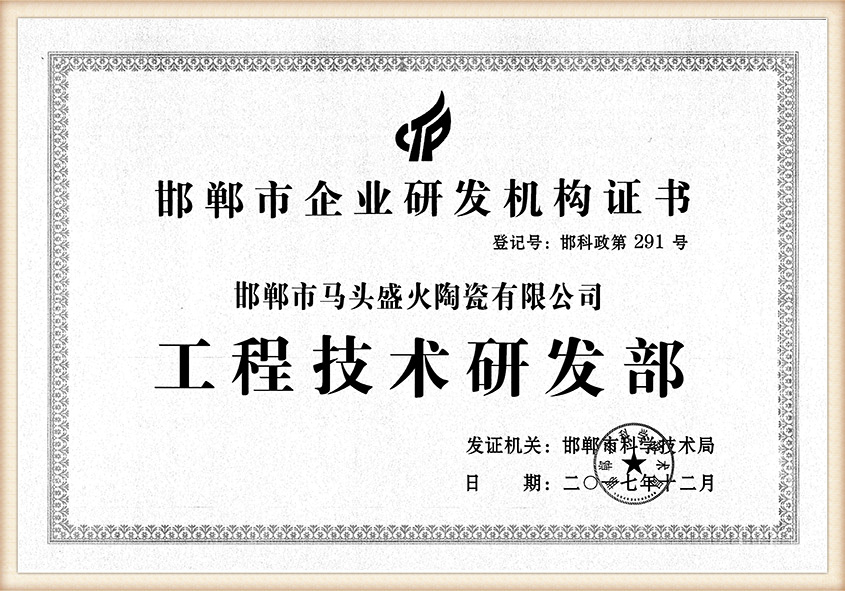
Once the mold and cores are prepared, it is time to melt the metal. The type of metal used will depend on the final application but often includes ferrous metals like iron and non-ferrous metals like aluminum. The metal is melted in a furnace, reaching temperatures that allow it to become liquid. Careful temperature control is crucial at this stage to avoid any contamination and ensure the metal is homogenous.
5. Pouring
The next step is pouring the molten metal into the mold cavity. This must be done carefully to avoid creating defects such as sand inclusions or air pockets. Pouring can be done manually or using automated systems, and it often involves techniques to control the flow rate and temperature of the molten metal.
6. Cooling and Solidification
After the metal is poured, it begins to cool and solidify. This process can take several hours or more, depending on the size and thickness of the casting. Proper cooling is essential to avoid defects such as warping or cracking.
7. Shakeout and Cleaning
Once the metal has fully solidified, the next step is to remove the mold and core, a process known as shakeout. The mold is typically broken apart to retrieve the casting. Following this, any extra sand, cores, or gating systems must be removed, and the casting may undergo additional processing, such as machining or surface finishing.
Conclusion
Sand casting is a critical manufacturing process that brings to life complex geometries and high-quality metal parts. From pattern making to the final cleaning, each step is integral to ensuring the success of the casting. Its relative simplicity, versatility, and affordability make sand casting a popular choice across various industries, from automotive to aerospace, showcasing the enduring relevance of this ancient technique in modern manufacturing.
Post time:Aug . 20, 2024 19:41
Next:Top Suppliers of Foundry Sand for Your Manufacturing Needs