The Importance of Foundry Sand in Metal Casting
Foundry sand plays a crucial role in the metal casting industry, serving as one of the foundational materials in the production of various metal components. This specialized sand, primarily composed of silica, is used in the creation of molds and cores that shape molten metal into the desired specifications. The unique properties of foundry sand make it an indispensable resource for foundries, from large industrial operations to smaller artisan workshops.
One of the key characteristics of foundry sand is its ability to withstand high temperatures. When molten metal is poured into a mold, temperatures can reach extremes, often exceeding 1,500 degrees Fahrenheit. Foundry sand, particularly silica sand, can endure these conditions without degrading, making it suitable for the high-heat environment of metal casting. Its thermal stability ensures that the mold maintains its shape and structural integrity during the casting process, leading to precise and accurate metal parts.
Another important attribute of foundry sand is its grain shape and size distribution. Well-graded sand with uniform particle size allows for better mold compaction and minimizes the presence of voids. This compaction is vital for creating molds that can resist the pressure of molten metal. Additionally, the shape of the sand grains influences the flowability and packing density, affecting the overall quality of the castings produced. Foundry sand is often used in combination with various binders, such as clay or resin, to enhance its properties and improve mold strength.
Recycling foundry sand has become a significant trend in the industry, driven by sustainability initiatives and the need for cost-effective solutions. After the casting process, unused or spent sand is often recovered and processed for reuse. This not only reduces waste but also lowers the demand for new raw materials, leading to multiple environmental benefits. Many studies show that recycled foundry sand can be used effectively in construction projects, land reclamation, and even as a substitute for fine aggregate in concrete.
foundry sand
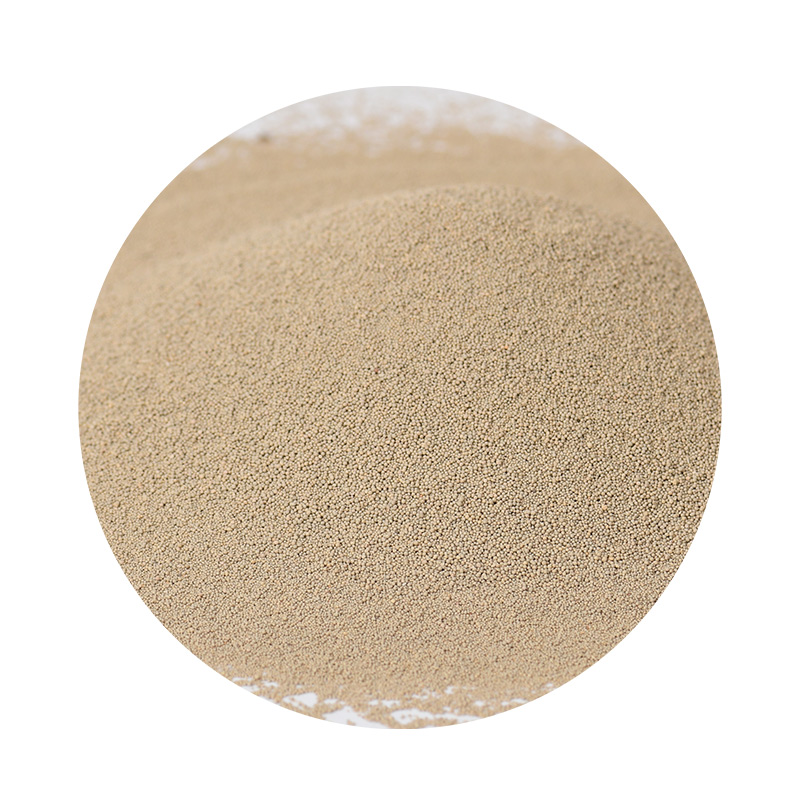
Despite the advantages, foundry sand management poses challenges. The need for consistent quality and performance can be demanding, and the recycling process requires careful handling to ensure that contaminants are removed. Furthermore, regulatory standards often necessitate that foundry sand, when repurposed, meets specific environmental requirements to minimize negative impacts.
The casting process itself is complex and involves several stages, where foundry sand plays a pivotal role. First, patterns are created to form the mold cavity; then, sand is packed around these patterns to create a mold. The pattern is removed, and the cavity is left behind. Once the mold is ready, molten metal is poured into the cavity, filling it entirely, and allowed to cool and solidify. After cooling, the mold is broken apart to retrieve the cast component, demonstrating the effective transformation of raw materials into usable parts.
Furthermore, the global demand for metal parts continues to grow, driven by industries such as automotive, aerospace, and machinery manufacturing. This increase in demand places added pressure on foundry operations to innovate and optimize their processes, further highlighting the importance of foundry sand as a critical resource. Trends such as 3D printing and advanced molding techniques are also emerging, providing new ways to utilize foundry sand and improve casting efficiency.
In conclusion, foundry sand is not only a vital component in the metal casting industry but also an area of ongoing innovation and sustainability efforts. Its unique properties, combined with effective recycling practices, help foundries reduce costs, minimize environmental impact, and produce high-quality metal castings. As the industry evolves, the role of foundry sand will continue to be significant, underscoring the material's importance in shaping the future of metal production.
Post time:Nov . 06, 2024 04:59
Next:what is a sand casting