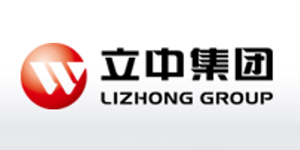
sand foundry. These workers are responsible for creating the molds, pouring the molten metal, and finishing the final product. They must have a keen eye for detail and a steady hand to ensure that each part meets the required specifications. While sand casting is a popular choice for many manufacturers, it does have some limitations. The process can be time-consuming, as the sand molds need time to dry and harden before the metal can be poured. Additionally, sand casting may not be suitable for parts that require very high precision or have thin walls. Despite these limitations, sand foundries continue to play a vital role in the manufacturing industry. They provide a cost-effective and efficient way to produce high-quality metal parts that are used in a wide range of products. As technology continues to evolve, sand foundries are also adapting to incorporate new techniques and materials to improve their processes and capabilities. In conclusion, sand foundries are essential for many industries that rely on metal parts for their products. Sand casting offers a versatile, cost-effective, and reliable method for creating complex metal components with high accuracy and surface finish. With skilled workers and advanced technology, sand foundries are well-equipped to meet the growing demand for quality metal parts in the manufacturing industry. Post time:Jul . 10, 2024 16:29
Next:3D Printing Applications in Sand Casting Optimization and Efficiency Improvement