Understanding Foundry Sand Specifications
Foundry sand plays a crucial role in the metal casting process, serving as a mold material that shapes molten metal into desired forms. The specifications for foundry sand are essential to ensure that the casting process yields high-quality metal products with minimal defects. In this article, we will explore the key specifications of foundry sand, focusing on its composition, properties, and the criteria that define its suitability for casting applications.
Composition of Foundry Sand
The primary component of foundry sand is silica (quartz), which comprises around 90-95% of the total material. The high silica content contributes to the thermal stability and strength of the mold. In addition to silica, foundry sand may contain other minerals, such as clay, feldspar, and oxides, which can influence its properties. For instance, clay content is critical because it helps bind the sand grains together, providing strength to the mold. The ideal foundry sand should be well-graded, meaning it must have a uniform distribution of particle sizes to enhance mold strength and reduce permeability.
Key Properties of Foundry Sand
The specifications for foundry sand include several key properties
1. Grain Size and Distribution The average grain size of foundry sand typically ranges from 0.1 to 0.6 mm. A well-graded sand mixture allows for better packing, resulting in a stronger mold. The uniformity coefficient, which measures the range of particle sizes, should ideally be between 1.5 and 2.0.
foundry sand specifications
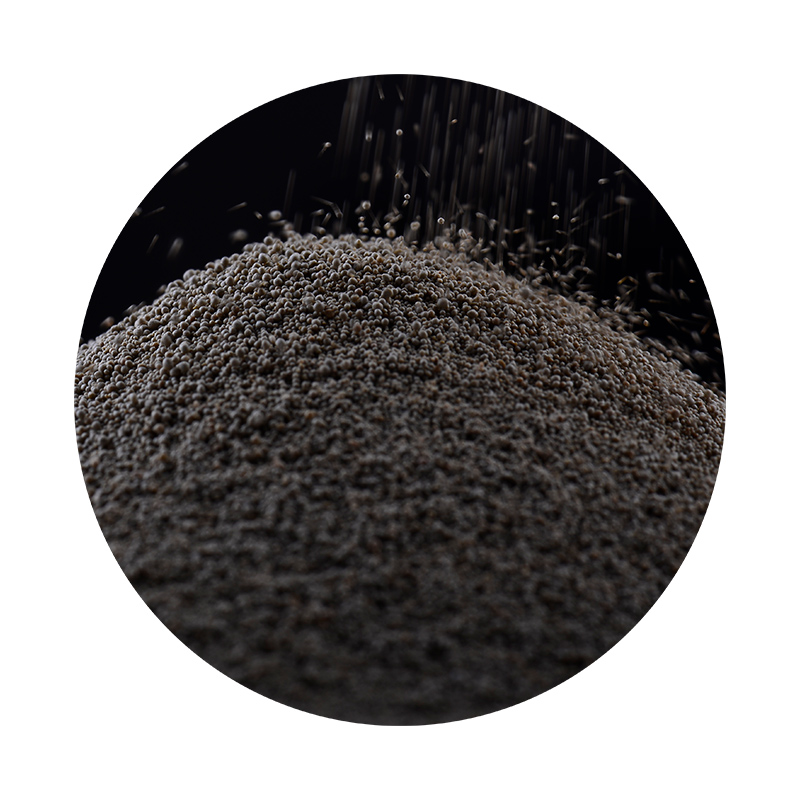
2. Permeability This property indicates the sand's ability to allow gases to escape during the casting process. High permeability is essential to prevent gas entrapment, which can lead to casting defects such as blowholes. Permeability is affected by grain shape, size, and the presence of fines.
3. Moisture Content The moisture content of foundry sand affects its bonding characteristics. A typical moisture content range is between 2% and 6%, with higher levels potentially leading to defects due to excessive steam generation during casting.
4. Clay Content The amount and type of clay influence the sand's bonding strength. Generally, a clay content of 5% to 15% is desirable, with bentonite clay being the most commonly used binder due to its excellent thermal and mechanical properties.
5. Thermal Stability Foundry sand must withstand high temperatures without breaking down or altering its structure. This ensures that the molds maintain their shape and integrity throughout the casting process.
Conclusion
In conclusion, foundry sand specifications are fundamental to the metal casting industry. Understanding the composition, properties, and acceptance criteria for foundry sand helps foundries achieve optimal casting quality and efficiency. By selecting the appropriate sand based on these specifications, manufacturers can minimize defects, improve mold strength, and ultimately enhance the performance of their metal products. As technology advances, ongoing research and development will continue to refine the understanding of foundry sand specifications, ensuring better quality and more sustainable practices in metal casting.
Post time:Aug . 28, 2024 12:18
Next:标题TitleSandCastingProsesi-TaalqivaQo'llanilishi