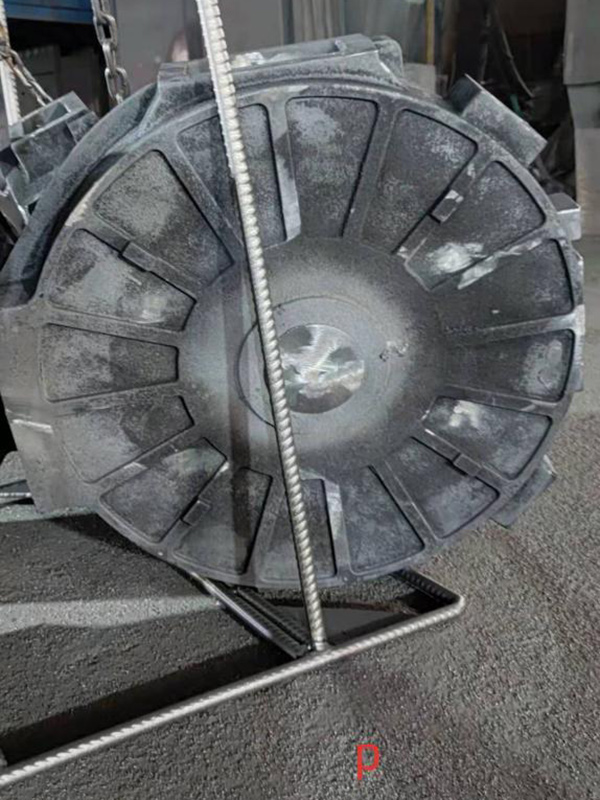
sand preparation in foundry. Foundry workers must carefully control the amount of water added to ensure that the sand is properly prepared for casting. After the sand is properly mixed with the binder and water, it is ready to be used to create molds for casting. The sand is packed around a pattern, which is a replica of the final casting, to create a cavity into which the molten metal will be poured. The sand mold is then dried and hardened to increase its strength and durability during casting. In some cases, foundries may use special treatments on the sand to improve its properties for casting. These treatments may include adding additives to the sand, such as coal dust or iron oxide, to increase its refractoriness and reduce expansion during casting. Foundries may also use sand reclamation processes to recycle used sand, reducing waste and costs in the foundry process. Overall, sand preparation is a crucial step in the foundry process that directly impacts the quality of the final castings. By carefully selecting the right type of sand, mixing it with the appropriate binder and water, and properly preparing the sand mold, foundries can ensure that their castings meet the highest quality standards. Effective sand preparation can improve casting efficiency, reduce defects, and ultimately lead to better final products for a wide range of industries. Post time:Jul . 10, 2024 20:25
Next:Super sands for endless fun and creativity with unique magical properties perfect for play.