Different Types of Sand Casting
Sand casting is one of the oldest and most versatile metal casting processes, used by manufacturers to create complex shapes and parts out of various metals. Its popularity is primarily due to its low cost, adaptability to different materials, and ability to produce intricate designs. This article explores the different types of sand casting methods and their respective advantages and applications.
1. Green Sand Casting
Green sand casting is the most common type of sand casting. The term “green” refers to the moisture content in the sand mixture rather than the color. This method utilizes a mixture of sand, clay, and water. The clay serves as a binder to hold the sand grains together. The mold is created using this mixture, making it easy to shape and form.
Advantages Green sand casting is known for its low cost and ease of use. It allows for quick production of molds, which is advantageous for large runs of parts. Moreover, it provides excellent surface finishes and good dimensional accuracy.
Applications This method is suitable for producing automotive parts, industrial equipment components, and various other items requiring mass production.
Unlike green sand casting, dry sand casting involves sand that has been baked in an oven to eliminate moisture. This heating process enhances the strength of the mold and makes it reusable. Dry sand molds can withstand higher temperatures, making them ideal for casting metals with higher melting points.
Advantages Dry sand casting offers improved dimensional accuracy and better surface quality when compared to green sand casting. The molds are also more durable and can be reused multiple times, reducing material costs in the long run.
Applications This method is particularly beneficial for producing high-performance parts such as those used in aerospace applications and other industries where precision and surface finish are crucial.
different types of sand casting
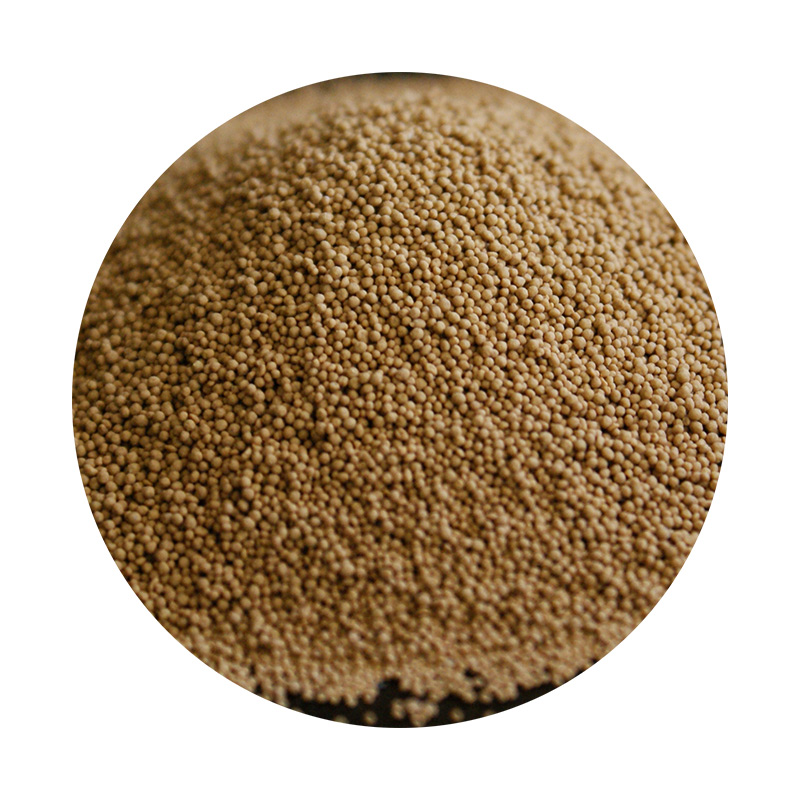
3. Shell Molding Casting
Shell molding casting is a more modern method that uses a thin shell of sand coated with resin instead of a thick sand mixture. This process involves heating a metal pattern and covering it with a mixture of sand and thermosetting resin. Once the resin hardens, the molds are assembled and filled with metal.
Advantages This casting method provides excellent dimensional accuracy and surface finish. The thin shell allows for intricate designs and reduces the amount of material needed. Shell molding also enhances the strength of the mold, allowing for more complex shapes.
Applications Shell molding is ideal for producing small to medium-sized components in industries such as automotive, aerospace, and heavy machinery, where precision is paramount.
4. Co2 Sand Casting
Co2 sand casting involves mixing sand with a chemical binder that hardens when exposed to carbon dioxide. This method creates a very strong mold that can last through multiple casting cycles. The molds are typically made in a two-part system that can be assembled before pouring the metal.
Advantages Co2 sand casting provides exceptional mold strength and dimensional accuracy, making it suitable for complicated designs. Additionally, the quick hardening process reduces the time needed to produce molds.
Applications This method is advantageous for producing highly detailed parts for industries like automotive and electronics, where intricacy and precision are required.
Conclusion
Each type of sand casting method offers unique advantages and is suitable for different applications. Green sand casting remains a staple in mass production due to its efficiency and low cost. In contrast, dry sand, shell molding, and Co2 sand casting provide enhanced accuracy and surface finish for specialized applications. Understanding these differences allows manufacturers to choose the right casting method to meet their specific needs, ultimately driving innovation and efficiency in production.
Post time:Jul . 30, 2024 00:42
Next:A Comprehensive Overview of Sand Casting Techniques and Their Applications in Modern Manufacturing