The Application of Sand Casting Process
Sand casting, one of the oldest and most versatile manufacturing processes, has been utilized for centuries in various industries. This technique involves creating a mold from sand and pouring molten metal into it to produce a desired shape. The simplicity, cost-effectiveness, and flexibility of sand casting make it a highly desirable method for producing metal parts and components, especially in situations where complex geometries and large sizes are required.
Historical Overview
The origins of sand casting date back to ancient civilizations, where artisans used sand to create molds for bronze and iron artifacts. Over the years, the process has evolved significantly, incorporating advancements in technology and materials. While traditional hand molding methods are still used, modern sand casting has introduced the use of automation and computer-aided design (CAD) to enhance precision and efficiency.
Process Overview
The sand casting process consists of several key steps pattern making, molding, pouring, and finishing. Initially, a pattern, usually made of metal or plastic, is created to match the desired final product. This pattern is then pressed into a mixture of sand and binder to form a mold. The sand used is typically silica sand, which has excellent thermal properties, allowing it to withstand high temperatures during melting.
Once the mold is prepared, molten metal is poured into the cavity created by the pattern. After the metal cools and solidifies, the mold is broken apart, and the casting is removed. The final step involves finishing processes, such as machining, sandblasting, or polishing, to achieve the desired surface quality and dimensions.
Applications Across Industries
Sand casting is widely used across various industries, including automotive, aerospace, machinery, and art. In the automotive sector, sand casting is critical for producing engine blocks, cylinder heads, and other components that require strong and durable materials. The ability to create intricate designs and large parts makes sand casting an ideal choice for manufacturers looking to produce lightweight yet robust components.
application of sand casting process
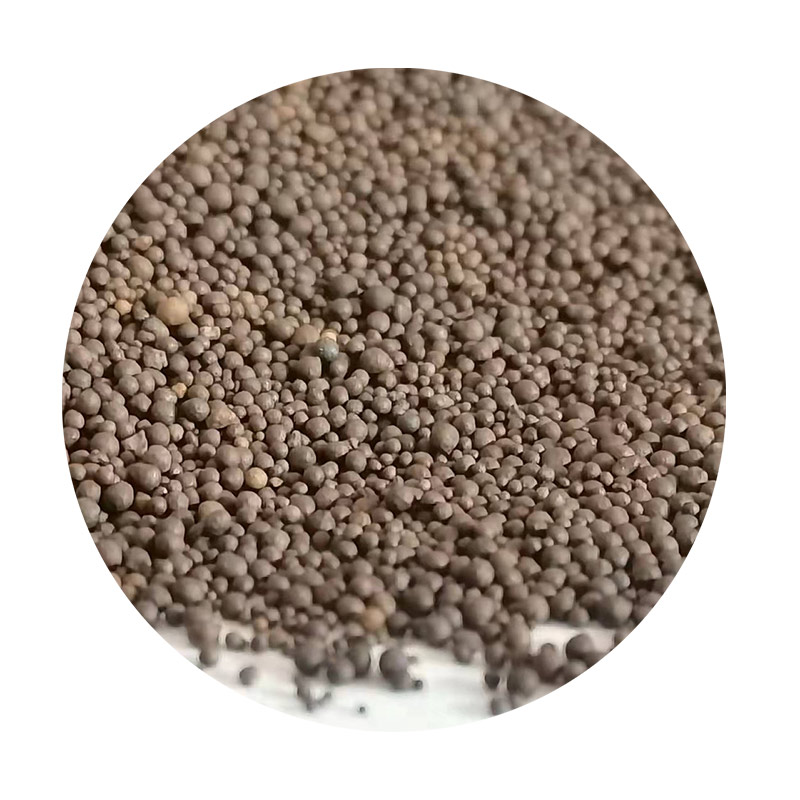
In the aerospace industry, sand casting is employed to create complex parts like turbine housings and structural components that must endure extreme conditions. The inherent flexibility of sand casting allows engineers to experiment with designs that optimize performance while maintaining weight efficiency.
Furthermore, sand casting is also prevalent in artistic applications, where sculptors and artisans create unique custom pieces. This practice not only enhances the aesthetic value of the artwork but also allows for the creation of one-of-a-kind sculptures that reflect individual creativity.
Advantages of Sand Casting
The sand casting process offers numerous advantages. Firstly, it is cost-effective, especially for low to medium production volumes. The materials used, mainly sand and metal, are relatively inexpensive, making this process accessible to small manufacturers and hobbyists alike.
Secondly, the sand casting process is highly adaptable. It can accommodate various metals, including iron, aluminum, and bronze, allowing manufacturers to choose the most suitable materials for their specific applications. Additionally, the sand mold can be reused multiple times, further enhancing its cost-effectiveness.
Thirdly, sand casting allows for the production of large parts, which is often difficult to achieve with other manufacturing techniques. This capability makes it a preferred choice for industries that require sizable components.
Conclusion
In conclusion, the application of the sand casting process is integral to many industrial sectors. Its historical significance, coupled with modern advancements, continues to make sand casting a popular choice for producing a wide range of metal components. The combination of cost-effectiveness, flexibility, and adaptability sets sand casting apart as a reliable and essential manufacturing technique in today's competitive market. As technology evolves, the sand casting process is likely to see further innovations, enhancing its role in the future of manufacturing.
Post time:Aug . 15, 2024 00:24
Next:Exploring Various Products and Applications Derived from Sand Casting Techniques in Manufacturing Industries