Materials Used in Sand Casting A Comprehensive Overview
Sand casting is one of the oldest and most widely used metal casting processes, celebrated for its versatility and cost-effectiveness. It involves creating a mold from sand and then pouring molten metal into the mold to form a desired shape. The choice of materials used in sand casting significantly influences both the quality of the final product and the efficiency of the casting process. This article will explore the primary materials used in sand casting, detailing their functions and importance in producing high-quality castings.
1. Sand
The most critical material in the sand casting process is sand itself. Typically, silica sand is used due to its excellent thermal and mechanical properties. Silica sand has a high melting point, allowing it to hold up against the temperatures of molten metal without breaking down. Moreover, the grain size of sand is essential; finer sands produce smoother surfaces, while coarser sands are better for rapid production and ease of molding. The sand used in casting is often mixed with a binder to enhance cohesion and improve mold strength.
2. Binders
Binders are materials added to sand to provide strength and hold the sand grains together. Common binders include clay, resin, and water. Clay is one of the most traditional and widely used binders, particularly in green sand casting, where a mixture of sand, clay, and moisture is used to form molds. Resin-bonded sand, on the other hand, uses a synthetic resin that is activated by heat or chemical agents, providing superior strength and surface finish. The choice of binder plays a vital role in determining the mold's permeability, strength, and collapsibility.
3. Additives
materials used in sand casting
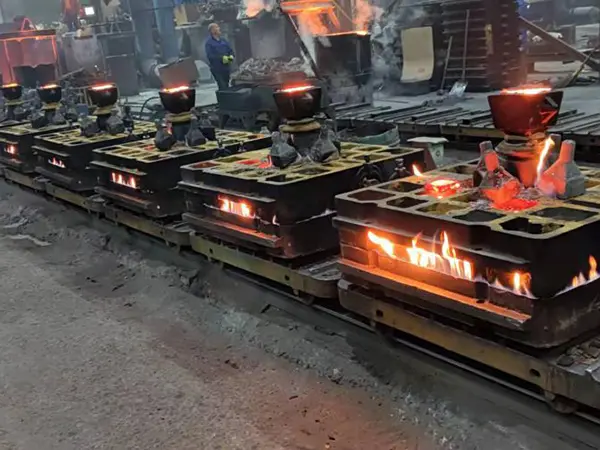
Various additives can be included in the sand mixture to improve certain properties. For instance, coal dust or graphite powder can be added to enhance the mold’s ability to withstand thermal stress. Other additives may reduce permeability or affect the surface finish of the casting. The careful formulation of sand mixtures with additives can significantly impact not just the casting process but also the quality of the final product.
4. Metals
The type of metal used for casting is equally crucial. Sand casting accommodates a wide range of metals, including ferrous and non-ferrous alloys. Commonly cast materials include aluminum, iron, brass, and bronze. Each metal has unique properties and suitability for different applications. For example, aluminum alloys are favored for their lightweight and corrosion-resistant characteristics, making them ideal for automotive and aerospace applications. Iron, particularly cast iron, is extensively used for its durability and excellent fluidity in molten form, making it ideal for creating intricate designs.
5. Core Materials
In many sand casting applications, cores made from sand mixtures are used to create internal cavities in the cast part. Core materials can include sand mixtures that are bound with materials like resin or oil. The core is placed in the mold before pouring in the molten metal, allowing for complex geometries that include hollow sections, undercuts, or tubular forms. Proper selection of core materials is essential to ensure they can withstand the molten metal's heat and maintain the desired dimensions.
Conclusion
Understanding the materials used in sand casting is fundamental to mastering this ancient yet innovative manufacturing technique. The interplay between sand, binders, additives, metals, and core materials can significantly impact the efficiency of the casting process and the quality of the final product. As technology continues to advance, the development of new materials and processes is likely to further enhance the capabilities of sand casting, ensuring its relevance in modern manufacturing. Sand casting's ability to produce complex shapes with excellent surface finishes at a relatively low cost will continue to make it a popular choice across various industries for years to come.
Post time:Aug . 10, 2024 08:10
Next:Exploring the Innovations and Techniques in China's Sand Casting Industry for Enhanced Manufacturing Efficiency