Materials Used for Sand Casting
Sand casting, one of the oldest and most versatile metal casting processes, relies on the use of specific materials to create molds that form intricate metal shapes upon solidification. This process has been pivotal in various industries, including automotive, aerospace, and machinery manufacturing. Understanding the materials used in sand casting is critical for optimizing the quality and efficiency of the casting process.
1. Base Sand
The primary material used in sand casting is base sand, which serves as the main component of the mold. The most commonly used base sand is silica sand due to its high melting point, availability, and ability to withstand thermal expansion. Silica sand is composed primarily of quartz, which provides strength to the mold. Different grades of silica sand can be selected based on the size and type of the cast being produced. Other types of sand, such as zircon sand or chromite sand, may be utilized for specific applications to enhance the mold's thermal properties or improve surface finish.
To hold the grains of sand together and form a solid mold, binding agents are added to the sand mixture. The most widely used binding agent is clay, specifically bentonite clay, which helps in providing the necessary strength and cohesiveness to the sand. The clay acts by absorbing moisture and creating a bond between the sand grains. In some cases, organic binders or chemical binders may be used to enhance the mold’s strength at various temperatures. These binders are particularly beneficial in applications where a high degree of mold precision is required.
3. Water
what materials are used for sand casting
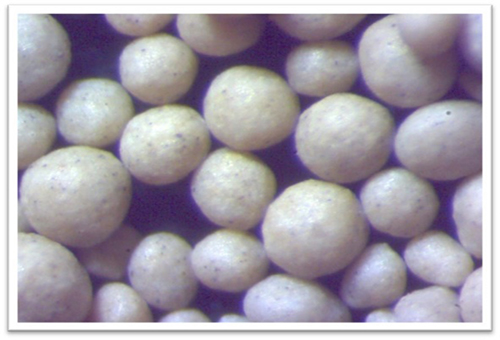
Water is a crucial ingredient in the sand casting process, as it activates the binding agents and helps in forming the mold. The amount of water added to the sand must be carefully controlled to maintain the desired consistency of the mold. Excess water can weaken the mold structure, while insufficient water can lead to cracking or incomplete forms. The proper balance ensures a high-quality mold that can accurately capture the details of the desired part.
4. Grain Finishing Agents
To improve the finish quality of the casted product, various grain finishing agents may be added to the sand mixture. These materials include graphite or sand additives that help reduce the friction between the sand and the molten metal, resulting in a smoother surface finish on the finished product. Such enhancements are crucial in applications where surface appearance is as important as structural integrity.
5. Release Agents
Release agents are often utilized to prevent the molten metal from sticking to the mold. These agents, generally applied to the mold surface, create a barrier that allows easy removal of the cast after solidification. Common release agents include oils or special chemical emulsions that do not adversely affect the casting quality. The use of effective release agents can significantly reduce the risk of mold damage and ensure the longevity of the sand molds.
Conclusion
In summary, the materials used in sand casting, including base sand, binding agents, water, grain finishing agents, and release agents, play vital roles in determining the success of the casting process. Each material must be chosen carefully depending on the specific requirements of the cast part, including its size, shape, and desired surface finish. As technology advances, innovations in these materials continue to enhance the efficiency and quality of sand casting, making it a preferred method for producing complex metal components in a cost-effective manner.
Post time:Aug . 11, 2024 11:50
Next:Top Sand Casting Manufacturers for High-Quality Custom Metal Parts and Components Production