Materials Used in Sand Casting
Sand casting is a versatile and widely employed method for producing metal parts across various industries, including automotive, aerospace, and manufacturing. It is characterized by its simplicity, cost-effectiveness, and adaptability to different metal types. One of the key factors contributing to the efficiency and quality of the sand casting process is the choice of materials used in the mold, core, and the metal being cast. This article explores the primary materials used in sand casting and their significance in the casting process.
1. Sand
The primary material used in sand casting is, unsurprisingly, sand. The type of sand most commonly used is silica sand, which is favored for its high melting point, availability, and excellent flowability when mixed with bonding agents. Silica sand is combined with a binding agent, such as clay, to form a mold. The clay helps the sand particles adhere to each other, providing the necessary strength and durability to withstand the pouring of molten metal.
When creating a mold, the sand is typically mixed with water to create a damp mass, which enhances the mold's cohesiveness. The moisture content is crucial; too much water can lead to mold defects, while too little can result in a weak mold that cannot retain the shape during casting.
2. Binding Agents
In addition to sand, binding agents play an essential role in sand casting. Common binding agents include clay (bentonite), resin, and other organic compounds. Clay is primarily used in the green sand process, where it provides the necessary plasticity and strength to the mold. Resin-bonded sands are used in the no-bake sand casting process, where chemical curing agents are added to the sand mixture. This approach results in a more durable mold that can withstand higher temperatures and offers finer detail in the final product.
what materials are used in sand casting
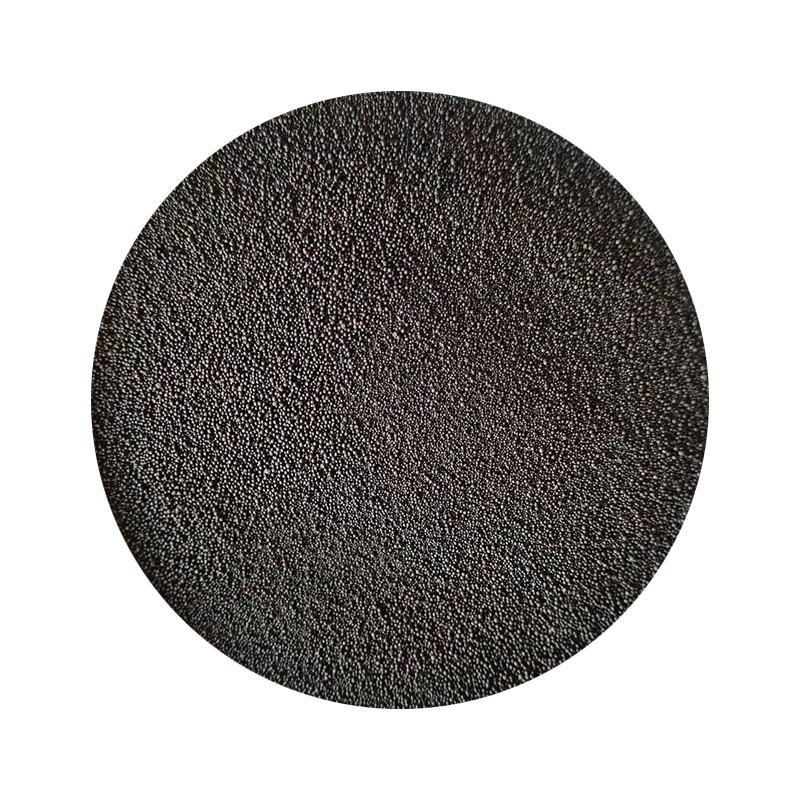
3. Metals
The choice of metal for casting also significantly influences the sand casting process. Ferrous metals, such as cast iron and steel, are commonly used due to their strength, durability, and ability to be cast into complex shapes. Cast iron, in particular, is favored for its excellent fluidity and capacity to fill intricate molds. Non-ferrous metals like aluminum, copper, and zinc are also popular choices in sand casting, often lauded for their lightweight properties and resistance to corrosion.
Each metal has specific requirements regarding pouring temperature, cooling rates, and shrinkage characteristics. For instance, aluminum has a lower melting point than iron, which allows for faster cooling and shorter cycle times, making it an attractive option for rapid production.
4. Additives and Coatings
To enhance performance and improve the quality of the casting, various additives and coatings are employed. For instance, sand additives may include materials like colorants or anti-bonding agents that prevent the molten metal from sticking to the mold. Coatings may also be applied to the sand molds to reduce metal penetration, facilitate easier mold release, and provide a smoother surface finish on the cast part.
Conclusion
In conclusion, the materials used in sand casting play a pivotal role in determining the process's efficiency and the quality of the final product. The primary components – sand, binding agents, and metals – work in conjunction to create a reliable and versatile method for producing high-quality metal components. By carefully selecting and optimizing these materials, manufacturers can achieve excellent cast quality, precise tolerances, and efficient production cycles, showcasing sand casting as a robust choice for a wide array of applications in today's industrial landscape.
Post time:Aug . 15, 2024 12:50
Next:Understanding the Importance of Metal Casting Sand in Manufacturing High-Quality Metal Products