Materials Used in Sand Casting
Sand casting, one of the oldest and most widely used metal casting processes, has been pivotal in manufacturing various metal components. The versatility and cost-effectiveness of this method make it a preferred choice in industries ranging from automotive to aerospace. The success of sand casting largely depends on the materials used in the process. This article will explore the key materials involved, focusing on sand, binders, metals, and additives that enhance the casting quality.
1. Sand
The primary material used in sand casting is, unsurprisingly, sand. Typically, silica sand is employed due to its high melting point and extensive availability. The grain size of the sand plays a crucial role in determining the quality of the final casting. Fine sand provides a smooth surface finish, while coarse sand is better for creating moulds that can withstand higher temperatures.
Sand casting molds are often made using a mixture of sand and a bonding agent that holds the sand grains together. The most common type of sand used is green sand, which contains silica sand, clay, and water. The clay acts as a binder, helping to create the necessary strength in the mold. Other variants include resin-bonded sands, which use synthetic resins that result in smoother surface finishes and improved dimensional accuracy of the castings.
2. Binders
Binders play an essential role in the sand casting process. They enhance the cohesiveness of the sand particles and allow for the creation of molds that can withstand pouring temperatures. Clay is the traditional binder, specifically sodium bentonite, which is often used in green sand formulations. The addition of water activates the clay, which helps in binding the sand grains together.
In modern sand casting, chemical binders such as phenolic resins and epoxy resins are increasingly popular. These binders improve the mold's integrity, reduce the moisture content required, and provide a better surface finish. Binders can be customized to match the specific requirements of the casting application, allowing for enhanced performance in various operational conditions.
what materials are used in sand casting
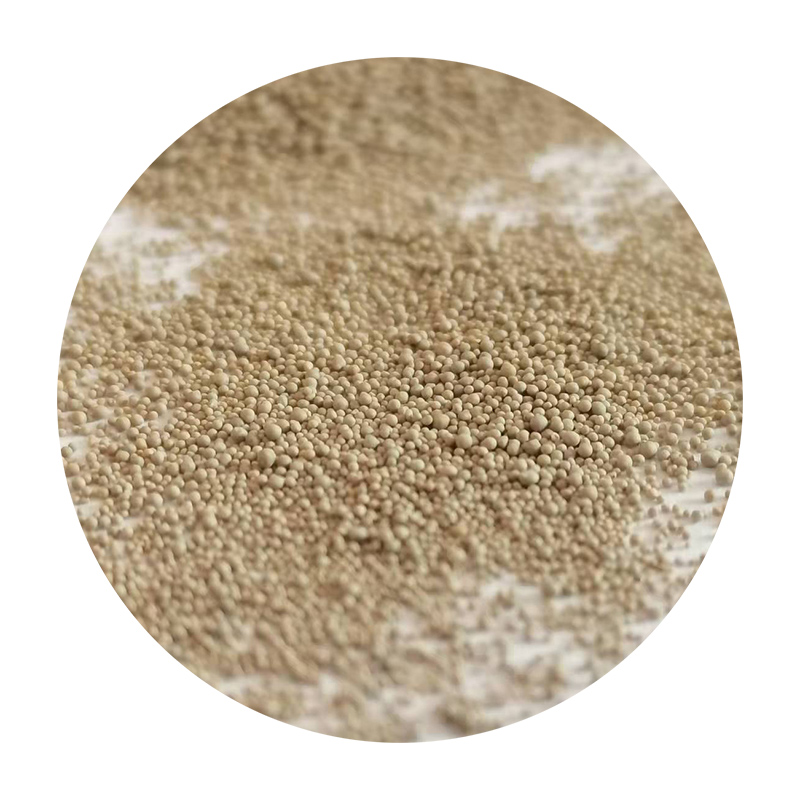
3. Metals
The choice of metal for casting is crucial, as it determines the mechanical properties and behavior of the final product. Ferrous metals like cast iron and steel are commonly used, owing to their excellent fluidity, strength, and cost-effectiveness. Non-ferrous metals, including aluminum, copper, and magnesium alloys, are also popular in sand casting applications. Aluminum, in particular, is favored in industries that require lightweight components with good corrosion resistance.
Each metal has its specific melting point, and understanding these characteristics is vital for successful casting. Proper temperature control during the melting phase is necessary to ensure that the metal flows smoothly into the mold and fills all cavities effectively.
4. Additives
To optimize the casting process and improve the quality of the final product, several additives can be introduced into the sand mixture. For example, oils, plasticizers, and surfactants can enhance the workability of the sand and improve the strength of the molds. Additionally, certain additives can mitigate defects such as gas porosity and shrinkage, which can undermine the integrity of the final casting.
Chemical additives may also be used to impart specific properties to the finished product, such as increased hardness or reduced brittleness. The selection of additives is typically tailored to the specifics of the casting application and the material being used.
Conclusion
In summary, the materials used in sand casting are fundamental to the process's success. From the choice of sand and binders to the selection of metals and additives, each material contributes significantly to the quality and functionality of the final product. By understanding and optimizing these materials, manufacturers can enhance their casting processes, improve production efficiency, and deliver high-quality components to various industries. With ongoing advancements in materials science, the future of sand casting looks promising, offering new opportunities for innovation and improvement.
Post time:Aug . 01, 2024 06:11
Next:An Overview of the Sand Casting Process and Its Key Steps in Metal Fabrication