Sand Used for Sand Casting An Essential Component in Metal Fabrication
Sand casting is one of the oldest and most widely utilized metal casting processes, revered for its ability to create complex shapes in a cost-effective manner. At the heart of this process is sand, but not just any sand; the type of sand used is crucial for achieving desired casting results. This article explores the properties, types, and importance of sand used in sand casting.
Properties of Casting Sand
The primary property of sand used in casting is its ability to form a compact mold while retaining the necessary porosity to allow gases produced during the casting process to escape. This characteristic prevents defects like gas holes in the finished product. Additionally, the sand must possess good thermal stability, which ensures the mold can withstand the high temperatures of molten metal without breaking down.
Moreover, the sand particles should be of a uniform size and shape, which facilitates better packing density and surface finish. Finer sands can reproduce intricate details but may require more binder and increase the risk of breaking, while coarser sands lend strength but may not capture fine details well.
Types of Sand Used in Sand Casting
1. Silica Sand This is the most commonly used type of sand in sand casting because of its high melting point and availability. Silica sand particles consist of silicon dioxide, making it chemically stable and resistant to heat. Various grades of silica sand are available, and the choice depends on the specific requirements of the casting process.
2. Chromite Sand Sourced from chromite ore, this sand has excellent heat resistance and is often used when casting high-temperature alloys. It provides a durability that is essential for intricate mold designs and intricate shapes that need high-definition detail.
sand used for sand casting
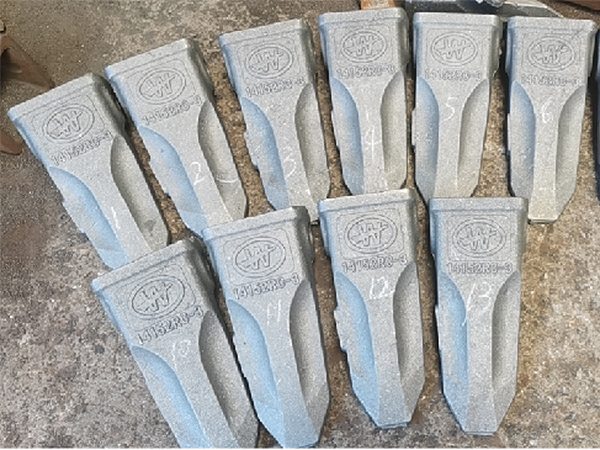
3. Zircon Sand This is a premium casting sand known for its high thermal stability and low thermal expansion. Zircon sand is often used for highly specialized applications where precision and surface finish are paramount.
4. Synthetic Sands These are engineered sands designed to provide specific properties, such as improved strength and reduced environmental impact. Synthetic sands can be tailored to meet specific casting needs, making them versatile for various applications.
Importance of Additives
To improve the performance of sand in casting, additives are often incorporated. These can include binders, which help to hold sand particles together, and other materials such as clay that enhance bonding capacity. The most common binder used is sodium silicate, which, when combined with sand, creates a strong and stable mold.
The proportion of clay and moisture in the sand is also a critical factor. Properly balanced sand mixture enhances mold strength and reduces shrinkage, allowing for a cleaner casting process.
Conclusion
The use of the right type of sand in the sand casting process is fundamental to producing high-quality metal components. With various properties offered by different types of sand, foundries must choose carefully based on the specific requirements of their casting needs. The combination of the correct sand type, appropriate additives, and optimal processing techniques is crucial for achieving precision, efficiency, and cost-effectiveness in sand casting. As technology advances and new materials are developed, the future of sand casting looks promising, heralding innovations that will further enhance this age-old practice in metal fabrication.
Post time:Aug . 02, 2024 14:31
Next:A Comprehensive Guide to Choosing and Using Ceramic Sanding Discs for Optimal Results