Sand Casting Foundries An Essential Element in Modern Manufacturing
Sand casting, a process that has been around for centuries, continues to play a crucial role in the manufacturing industry today. This method involves creating a mold out of sand to form metal parts, which can be used in a variety of applications, from automotive to aerospace industries. Sand casting foundries are specialized facilities that focus on this production technique, and understanding their operations and advantages can shed light on their importance in modern manufacturing.
The Process of Sand Casting
The sand casting process begins with the creation of a mold. The first step involves the design and manufacture of a pattern, which is an exact replica of the final product. This pattern is usually made from materials like wood, metal, or plastic. Once the pattern is made, it is placed in a box, and sand mixed with a binding agent is packed around it. The binder helps the sand retain its shape once the pattern is removed. After this, the pattern is extracted, leaving a hollow space that mirrors the shape of the desired part.
Next, molten metal is poured into the mold cavity. The type of metal used will depend on the application but often includes aluminum, iron, or bronze. Once the metal cools and solidifies, the mold is broken away, revealing the cast part. This part can then be further processed through machining, polishing, or other finishing techniques to meet specific quality and dimensional standards.
Benefits of Sand Casting
One of the primary advantages of sand casting is its versatility. It is capable of producing a wide range of parts of varying sizes and complexities. Whether an intricately designed component or a large heavy part, sand casting can accommodate different specifications effectively. Moreover, the materials used can be varied, allowing foundries to cater to diverse client needs.
sand casting foundries
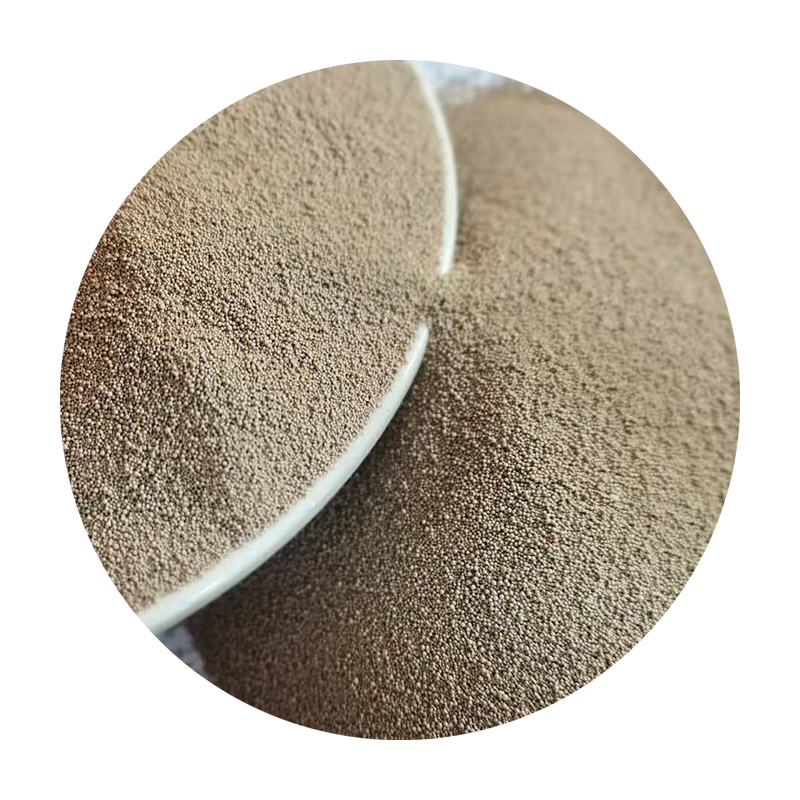
Additionally, sand casting is cost-effective, especially for small production runs. Since the molds are made from sand, they can be created relatively quickly, reducing setup times and costs associated with more complex processes such as die casting. This is particularly beneficial for industries that require rapid prototyping or low-volume production.
Sand casting also generates minimal waste, making it an environmentally friendly option compared to other casting methods. The sand used in the molds can typically be reclaimed and reused multiple times, reducing the need for new materials. This sustainability aspect aligns with the growing emphasis on eco-friendly manufacturing practices within the industry.
Challenges and Innovations
Despite its many benefits, sand casting does come with challenges. The surface finish of sand-cast products is generally not as smooth as those produced through other casting methods, leading to additional finishing processes. Variability in sand quality can also impact the final product's integrity, necessitating careful quality control at foundries.
Innovations in sand casting technology have been paving the way for improvements. Advances such as the use of computer-aided design (CAD) and computer-aided manufacturing (CAM) allow for more precise mold designs and enhanced simulation of the casting process. Additionally, developments in binder technology have improved mold strength and reduced environmental impacts.
Conclusion
Sand casting foundries remain an integral part of contemporary manufacturing, providing essential services for various industries. Their ability to create complex parts at a cost-effective rate, along with advancements in technology, ensures their relevance in the evolving landscape of production. As industries continue to demand high-quality, precise components in a sustainable manner, sand casting will undoubtedly continue to adapt and thrive, proving its enduring importance in the world of manufacturing.
Post time:Aug . 14, 2024 11:02
Next:An Overview of the Sand Casting Process and Its Applications in Metalworking Techniques