Open Sand Casting An Overview
Open sand casting is one of the oldest and most widely used casting processes in metallurgy and manufacturing. This method involves pouring molten metal into a mold made from a sand mixture, allowing for the creation of a variety of shapes and sizes. Its simplicity, low cost, and adaptability make it an appealing option for both small-scale and large-scale production.
The process of open sand casting begins with the preparation of a mold. The mold is typically composed of a mixture of sand and a binding agent, which helps to hold the sand particles together. A key aspect of open sand casting is that the mold is formed using two halves, known as the cope (top half) and the drag (bottom half). The sculpting of these halves requires a pattern, which is an exact replica of the desired final product. The pattern is usually made from materials like wood, metal, or plastic.
Once the mold is created, it is important to ensure it can withstand the heat of the molten metal and maintain its shape. The sand mix is compacted tightly around the pattern, and after the pattern is removed, a cavity is left in the shape of the desired object. Venting systems are also often included in the mold design to allow gases to escape while the metal is poured, ensuring a smoother casting process.
Heating the metal is the next crucial step. Depending on the alloy being used, different temperatures are maintained to achieve a proper flow and avoid oxidation. Once the metal reaches the desired temperature, it is carefully poured into the mold through a sprue – an opening that leads to a reservoir where the molten metal is held temporarily before it fills the mold cavity.
open sand casting
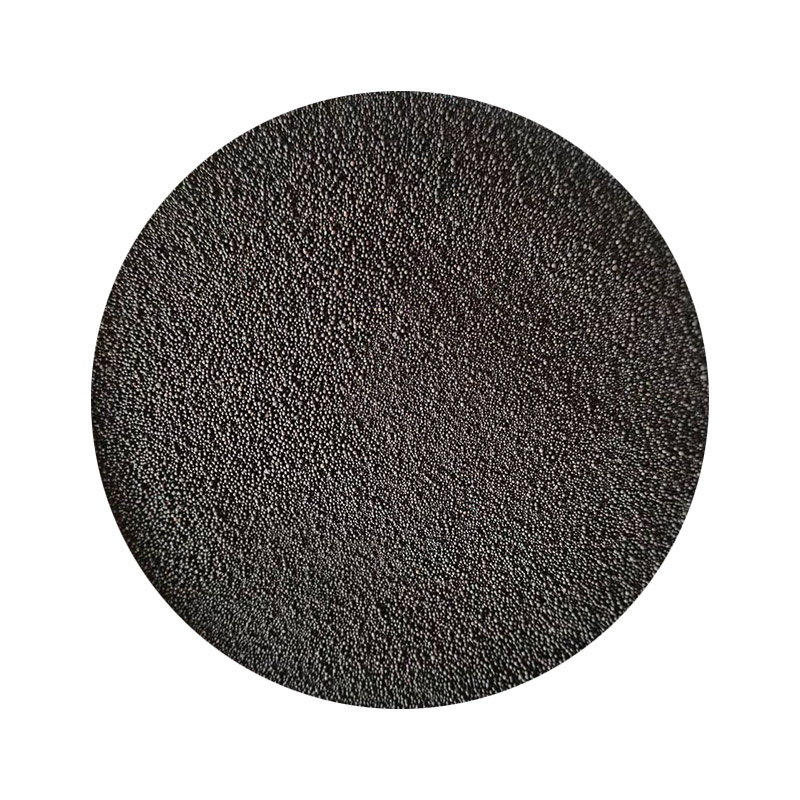
After the metal has cooled and solidified, the casting is removed from the mold. The sand mold, being relatively easy to break apart, allows for the quick extraction of the product. The final step involves cleaning and finishing the casting to remove any excess material, smooth out rough edges, and achieve the desired surface finish. This can involve processes such as sandblasting, grinding, or polishing.
Open sand casting has several advantages. It is highly versatile, allowing for the casting of large or heavy parts that may be difficult to produce using other methods. It can also accommodate a wide range of metals, including aluminum, bronze, cast iron, and steel. Additionally, setting up a sand casting operation can be done with relatively low investment compared to other casting techniques, such as die casting.
However, despite its benefits, open sand casting also has limitations. Surface finish and dimensional accuracy may not be as refined as other casting processes. There can also be issues with porosity and the formation of defects, such as gas inclusions if proper venting is not implemented. Moreover, the labor-intensive nature of creating molds and patterns can add to production times, especially in high-volume manufacturing.
In conclusion, open sand casting remains a fundamental process in the manufacturing sector. Its flexibility, ease of use, and economic practicality make it a popular choice for producing a diverse array of metal components. As industries continue to evolve, advancements in materials and technology may further enhance the effectiveness of this age-old method, ensuring its relevance in modern manufacturing.
Post time:Aug . 08, 2024 12:35
Next:Exploring the Benefits of Sand Casting in Modern Manufacturing Processes and Applications