Open Sand Casting An Overview of the Process and Its Applications
Open sand casting is a widely used metal casting process that is notable for its simplicity and versatility. This method involves creating a mold for molten metal by packing sand around a pattern, usually made of metal or another durable material. As one of the oldest and most established casting techniques, open sand casting finds its application in various industries, from automotive to aerospace and even art.
The Process of Open Sand Casting
The open sand casting process begins with the creation of a pattern that reflects the shape of the desired final product. This pattern can be made from various materials, including wood, metal, or plastic, and is often slightly larger than the finished part to account for metal shrinkage during cooling. Once the pattern is prepared, a mixture of sand and binder is packed tightly around it to form a mold.
The sand used in the casting process is typically a mixture of silica sand and clay, which gives it the necessary binding properties. The quality of the sand is crucial, as it needs to be fine enough to produce a smooth surface but coarse enough to allow for proper airflow during metal pouring. After the sand is packed around the pattern, the mold is carefully removed, leaving a negative impression of the part.
At this stage, the two halves of the mold are reassembled, and any necessary venting or gating systems are added to facilitate the flow of molten metal. Once prepared, the mold is heated to a certain temperature, and molten metal—usually aluminum, iron, or bronze—is poured into the cavity. The metal fills the mold and cools, solidifying into the shape of the original pattern. After a suitable cooling period, the mold is broken away, revealing the finished cast part.
Advantages of Open Sand Casting
open sand casting
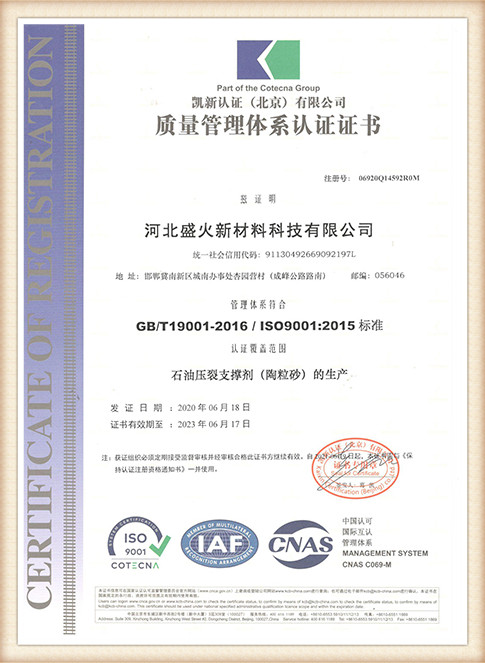
One of the primary advantages of open sand casting is its flexibility. The process can accommodate large and complex shapes that might be difficult to produce using other casting methods. Additionally, it allows for the production of a wide range of metal alloys, enhancing its versatility across different industries.
The cost-effectiveness of open sand casting is another significant benefit. The materials used in creating sand molds are relatively inexpensive, and the casting process can be scaled up or down to meet production needs. This makes it an attractive option for both small-scale operations and large manufacturing facilities.
Applications of Open Sand Casting
Open sand casting has a broad range of applications. In the automotive industry, it's commonly used to manufacture engine blocks, transmission cases, and various other components that require strength and durability. The aerospace sector also utilizes this method for producing parts where precise tolerances and material properties are critical.
Beyond industrial applications, open sand casting is also favored by artists and metalworkers. Many artisans employ this technique to create unique sculptures and decorative pieces, taking advantage of its ability to reproduce intricate details while offering the freedom to experiment with different metal alloys and finishes.
Conclusion
In conclusion, open sand casting stands as a fundamental method in the world of metal fabrication. Its simple yet effective process, combined with a wide range of applications and adaptability to various materials, ensures its continued relevance in modern manufacturing. Whether in industrial settings or creative endeavors, open sand casting remains a vital technique, highlighting the enduring legacy of this age-old method in shaping metal objects.
Post time:Aug . 06, 2024 16:01
Next:Is Sanding 3D Prints Necessary for Smooth Finishes and Improved Aesthetics in Your Projects