Iron Sand Casting An Overview
Iron sand casting is a specialized method of casting utilizing iron-rich sand as the primary material. This process has roots that trace back centuries, yet it remains a vital part of modern metallurgy and manufacturing. By leveraging the unique properties of iron sand, this technique is crucial for producing a range of industrial components, from automotive parts to intricate sculptures.
What is Iron Sand?
Iron sand, also known as magnetite sand, is a type of sand that contains a high percentage of iron oxides. This naturally occurring material is usually sourced from beach or river deposits, where geological processes have concentrated the iron particles over time. The presence of iron in the sand can be as high as 30% to 50%, making it particularly suitable for casting applications. The magnetic properties of iron sand also allow for easy separation and refinement, which is beneficial in the casting process.
The Casting Process
The iron sand casting process generally involves several steps
1. Preparation of Molds Molds are created from a mixture of iron sand, clay, water, and other binding agents. This mixture is compacted around a pattern to form a cavity that will hold the molten iron.
2. Melting Once the molds are prepared, pig iron or scrap metal is melted in a furnace. The choice of furnace—whether it's an electric arc type, induction furnace, or cupola—depends on the scale of production and the specific properties needed in the final cast.
3. Pouring The molten iron is poured into the mold cavity. The temperature and composition must be carefully controlled to ensure the final product meets the required specifications.
4. Cooling and Solidification After pouring, the molten iron cools and solidifies, taking the shape of the mold. The cooling time can vary, affecting the mechanical properties of the final cast.
iron sand casting
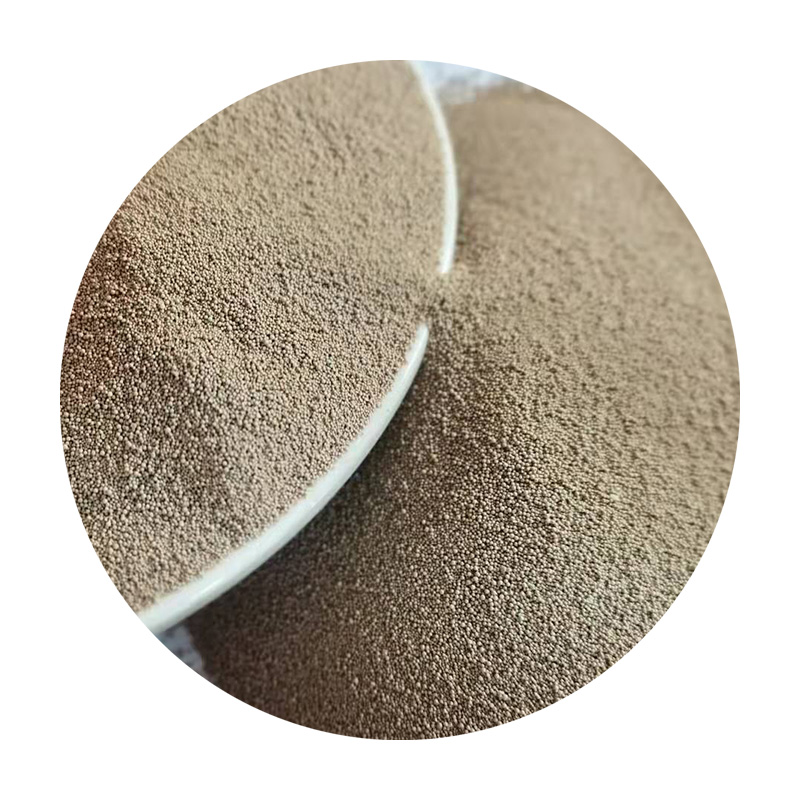
5. Finishing Once cooled, the mold is broken apart to retrieve the casting. This may require additional finishing processes, such as machining, sanding, or heat treatment, to achieve the desired surface finish and tolerances.
Advantages of Iron Sand Casting
Iron sand casting offers several potential advantages over traditional metal casting methods
- Cost-Effectiveness The use of readily available iron sand can significantly reduce material costs, especially in regions where it is abundant.
- Versatility Iron sand can be used to cast a wide variety of shapes and sizes, making this process suitable for numerous applications across different industries.
- Environmental Benefits Since iron sand can be sourced locally and is often a byproduct of other industrial processes, its use can reduce the carbon footprint associated with transporting conventional iron materials.
- Mechanical Properties Castings made from iron sand often exhibit superior mechanical strength and wear resistance, making them ideal for heavy-duty applications.
Challenges and Innovations
Despite its advantages, iron sand casting is not without its challenges. The quality of the final product can heavily depend on the purity and composition of the iron sand used. Contaminants can lead to defects in the casting, necessitating rigorous quality control measures. Furthermore, advancements in technology, such as 3D printing and digital modeling, are reshaping the landscape of casting processes, prompting traditional methods to adapt to stay competitive.
In conclusion, iron sand casting remains a vital method in modern manufacturing, balancing historical techniques with contemporary demands. As industries continue to evolve, the integration of innovative practices and materials promises to enhance the efficiency and effectiveness of this age-old craft, paving the way for exciting developments in the future.
Post time:Aug . 14, 2024 21:00
Next:Exploring Various Sand Types Used in Foundry Applications for Optimal Casting Performance