The Intersection of 3D Printing and Sand Casting Revolutionizing Manufacturing
In recent years, the manufacturing industry has witnessed a notable transformation driven by technological advancements. Among these innovations, 3D printing and sand casting are two prolific methods that have emerged to redefine how products are made. When combined, these technologies offer unparalleled advantages in efficiency, precision, and versatility, posing significant implications for various sectors, from automotive to aerospace.
Understanding the Technologies
3D printing, also known as additive manufacturing, involves creating objects layer by layer from a digital model. This method allows for intricate designs and rapid prototyping, significantly reducing the lead time for product development. On the other hand, sand casting is a traditional manufacturing process where a sand mold is created to produce metal parts. It involves pouring liquid metal into the mold, which is then allowed to solidify and take the shape of the mold cavity.
While sand casting has been a staple in manufacturing for centuries due to its ability to produce complex geometries, it often demands significant time and labor to create the molds. This is where 3D printing shines. By leveraging 3D printing technology, manufacturers can produce sand molds and cores with unmatched precision and speed, enhancing the overall casting process.
The Benefits of Integrating 3D Printing and Sand Casting
Integrating 3D printing with sand casting presents numerous benefits that are transforming the landscape of manufacturing
1. Rapid Prototyping The production of sand molds traditionally takes considerable time; however, using 3D printing, companies can quickly generate complex molds, dramatically reducing the time from design to production. This capability enables faster iterations and encourages innovation.
3d printer sand casting
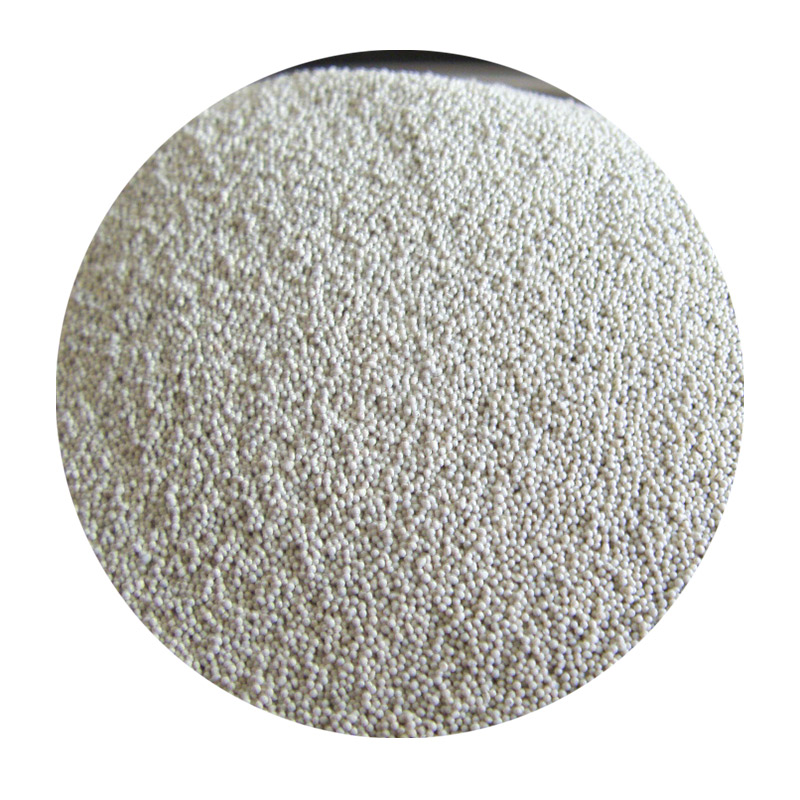
2. Cost-Effectiveness 3D printed sand molds often require less material than their traditional counterparts, which can lead to lower costs. Additionally, the reduction in lead time translates to cost savings in labor and overhead expenses.
3. Complex Geometries 3D printing allows for the creation of geometrically intricate designs that would be challenging, if not impossible, to achieve with conventional mold-making techniques. This capability facilitates the production of lightweight components and complex internal structures that enhance performance in applications such as aerospace parts or automotive components.
4. Sustainability The combination of these technologies can contribute to more sustainable manufacturing practices. 3D printing can reduce waste, as molds are produced with only the necessary material. Furthermore, it allows for the use of biodegradable binders in sand casting, aligning with the growing trend towards eco-friendly manufacturing.
5. Customization With 3D printing, customization becomes more accessible and cost-effective. Manufacturers can easily adjust designs to meet specific client requirements without needing to overhaul entire production lines. This flexibility is particularly valuable in industries where bespoke solutions are often demanded.
Future Implications
As the intersection of 3D printing and sand casting continues to evolve, we can anticipate significant impacts on manufacturing practices. Industries will be able to respond more swiftly to market demands, experiment with innovative designs, and enhance their production capabilities while reducing costs and material waste.
In conclusion, the fusion of 3D printing and sand casting represents a paradigm shift in manufacturing. By harnessing the strengths of both technologies, companies will be better equipped to meet the challenges of modern production demands, paving the way for a future characterized by innovation, efficiency, and sustainability. As this trend progresses, it will not only redefine manufacturing processes but also set new standards in product design and custom manufacturing.
Post time:Aug . 17, 2024 08:18
Next:Guide to Effectively Sanding Ceramic Surfaces for Best Results