Understanding the Role of Sand in Casting Processes
The casting process is a fundamental manufacturing technique used to create complex metal parts and components. One of the critical materials used in this process is sand, particularly in sand casting, which is one of the most prevalent casting methods due to its versatility, cost-effectiveness, and ability to produce intricate shapes. This article delves into the significance of sand in casting, its characteristics, types, and the impact it has on the overall quality of cast products.
The Importance of Sand in Casting
Sand is the primary mold material used in sand casting, where molten metal is poured into a mold cavity to produce the desired shape. The unique properties of sand make it suitable for this application. One of the most important factors is the sand's ability to withstand high temperatures without deforming, enabling it to hold the shape of the mold. Additionally, sand can be easily manipulated and reused, making it an economical choice for both large and small production runs.
Properties of Casting Sand
The quality of sand used in casting directly affects the final product's properties. Key characteristics of casting sand include grain size, shape, and composition.
1. Grain Size The size of the sand grains influences the surface finish and dimensional accuracy of the cast part. Finer grains tend to provide a smoother surface but can create challenges in terms of strength and permeability. Conversely, coarser grains may enhance the mold's strength but might result in a rougher surface finish.
2. Grain Shape The shape of sand grains—whether they are angular or round—can also impact mold strength and collapsibility. Angular grains lock together better, providing superior strength, while spherical grains allow for easier flow and compaction.
3. Composition Commonly, silica sand is used due to its abundance and high melting point. However, other materials can be added to improve specific properties. For example, using clay as a binder can enhance the mold's ability to retain shape under the weight of molten metal, while additives like graphite can help boost thermal conductivity and improve surface finish.
sand in cast
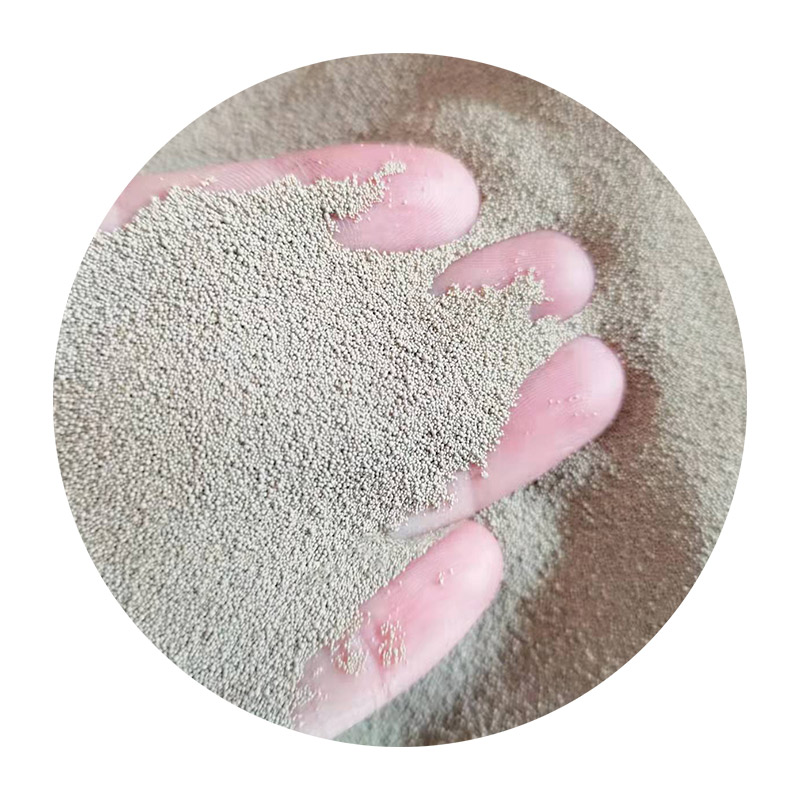
Types of Sand Used in Casting
Various types of sand are utilized in the casting process, each catering to different requirements and applications
1. Green Sand A traditional mixture of sand, clay, and water, green sand is widely used for its ease of use and ability to produce detailed features. It is typically employed in ferrous casting and offers good strength and collapsibility.
2. Dry Sand As the name suggests, dry sand is baked to remove moisture, resulting in a more rigid and strong mold. It is often used for high-precision work and produces a better surface finish.
3. Resin Sand This type of sand utilizes synthetic resin as a bonding agent. Resins cure through chemical reactions, providing high strength and excellent dimensional accuracy. Resin sand is best suited for production in small batches where high-quality finishes are paramount.
The Impact on Product Quality
The choice of sand and its preparation significantly impact the quality of the final product. Factors such as surface roughness, dimensional accuracy, and overall strength of the casting can be traced back to the characteristics of the sand used. Poor-quality sand can lead to defects like sand inclusions, porosity, and dimensional inaccuracies, ultimately affecting the performance and reliability of the finished product.
In conclusion, sand plays a crucial role in the casting process, providing the necessary properties to create molds capable of producing high-quality castings. As industries continue to evolve, advances in sand technology and casting techniques will undoubtedly enhance the efficiency and accuracy of this essential manufacturing process. Understanding the intricacies of sand in casting not only aids engineers and manufacturers in their craft but also ensures that the final products meet the ever-growing demands of modern engineering.
Post time:Jul . 31, 2024 00:53
Next:Exploring Various Applications and Advantages of Sand Casting in Modern Manufacturing Industries