Advantages and Disadvantages of Sand Casting Process
Sand casting is a widely used metal casting process that involves creating a mold from sand, which is then used to form metal components. This method has been around for centuries and continues to be a popular choice among manufacturers due to its unique set of advantages and disadvantages.
Advantages of Sand Casting
1. Versatility One of the greatest strengths of sand casting is its versatility. It can be used to cast a wide range of metals, including aluminum, bronze, iron, and steel, making it suitable for various applications across different industries. This adaptability allows manufacturers to create complex shapes and designs that might be challenging with other casting methods.
2. Cost-Effectiveness Sand casting is generally more cost-effective than other casting processes, especially for low to medium production volumes. The materials used, such as sand and binder, are relatively inexpensive, and the setup costs for molds are lower than other methods like investment casting or die casting.
3. Large Part Production The process can accommodate large metal parts, which is beneficial in industries such as automotive, aerospace, and construction. This capability allows for the production of hefty components without compromising quality.
4. Ease of Modification Making changes to the design or mold is relatively straightforward in sand casting. If adjustments are needed, manufacturers can modify the sand mold easily, making it a practical choice for prototypes or low-volume production runs.
5. Good Surface Finish Sand casting can achieve a good surface finish and fine detail, particularly when using finer grades of sand or adding additional finishing processes afterward. This allows for the creation of components that meet specific aesthetic and functional requirements.
advantages and disadvantages of sand casting process
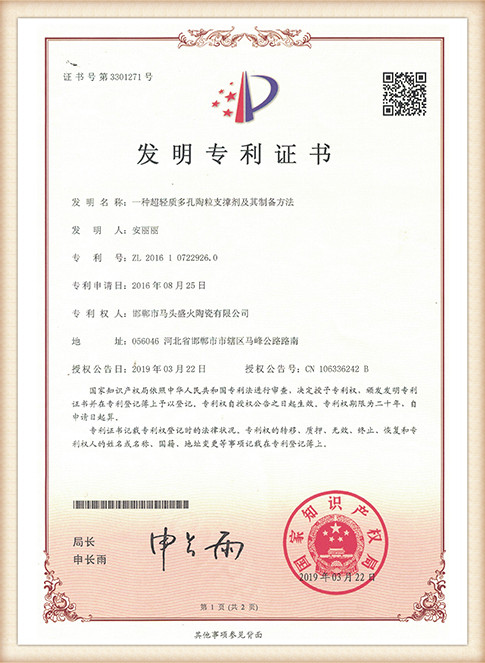
Disadvantages of Sand Casting
1. Surface Quality While sand casting can achieve a fair surface finish, it typically does not match the smoothness obtained through other casting methods, such as die casting. The rough texture of the surface may necessitate additional machining processes, thereby increasing the overall production cost and time.
2. Dimensional Tolerances The process may not provide the tight dimensional tolerances that can be achieved with other casting techniques. This limitation can lead to the necessity for secondary finishing operations, which may increase production time and costs.
3. Labor-Intensive Sand casting can be more labor-intensive than automated processes. The manual labor involved in creating molds, assembling cores, and handling molten metal can lead to higher labor costs and extended production timelines, particularly for larger projects.
4. Environmental Concerns The sand casting process generates a significant amount of waste material, including unused sand and other by-products. Additionally, the use of binders and other materials can lead to environmental concerns if not managed properly. The disposal of used sand and the emissions from molten metal can pose ecological challenges.
5. Limited Production Rate For high-volume production runs, sand casting may not be the most efficient method. The time required to create molds and cure the sand means it is often slower than other casting processes. Manufacturers requiring rapid production may find this aspect a considerable drawback.
Conclusion
In summary, while sand casting presents numerous advantages such as cost-effectiveness, versatility, and the ability to produce large parts, it also has notable disadvantages, including potential issues with surface finish and dimensional tolerances. Manufacturers must carefully assess their specific needs, production volume, and budget constraints when considering sand casting as a viable option for their metal component production. Despite its drawbacks, sand casting remains a crucial process in the manufacturing industry, thanks to its continuous evolution and adaptation to modern demands.
Post time:Aug . 14, 2024 06:11
Next:Benefits of Using Sand Casting Techniques in Manufacturing Processes and Product Development