Sand Casting Alloys A Comprehensive Overview
Sand casting is one of the oldest and most versatile metal casting processes, which involves pouring molten metal into a sand mold to create a desired shape. The choice of alloy is critical in this process, as it directly influences the mechanical properties, surface finish, and overall quality of the final product. This article explores various alloys commonly used in sand casting, their properties, and application areas.
Aluminum Alloys
Aluminum alloys are among the most widely used materials in sand casting due to their excellent strength-to-weight ratio, corrosion resistance, and good thermal and electrical conductivity. Common aluminum alloys used in sand casting include 356.0, 319.0, and 413.0.
- 356.0 is known for its high fluidity, making it ideal for intricate designs. It is commonly used in automotive and aerospace applications. - 319.0 offers improved corrosion resistance and is often used in engine components, such as cylinder heads and engine blocks. - 413.0 is primarily utilized in applications requiring high strength and good wear resistance, making it suitable for heavy-duty machinery.
Iron Alloys
Iron alloys, particularly cast iron, hold a significant position in the sand casting industry. They are known for their excellent machinability, wear resistance, and good fluidity. The main types of cast iron include gray iron, ductile iron, and white iron.
- Gray Iron is the most common type and is characterized by its high carbon content, making it suitable for applications requiring good vibration dampening and thermal conductivity. It is often used in engine blocks, machine bases, and various automotive parts. - Ductile Iron (also known as spheroidal graphite iron) is recognized for its enhanced ductility and impact resistance, making it ideal for high-stress applications such as gears, pipes, and heavy machinery components. - White Iron is harder and more brittle than gray iron and is generally used in applications requiring high wear resistance, such as industrial molds and wear-resistant surfaces.
sand casting alloys
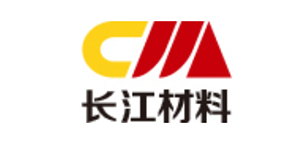
Copper Alloys
Copper alloys, particularly brass and bronze, are also utilized in sand casting, primarily for their excellent corrosion resistance and antimicrobial properties.
- Brass, an alloy of copper and zinc, is often cast into decorative items, plumbing fittings, and musical instruments due to its attractive yellow color and machinability. - Bronze, primarily composed of copper and tin, is known for its superior resistance to corrosion and is often used in marine hardware, sculptures, and bearings.
Magnesium Alloys
Magnesium alloys are gaining popularity in the sand casting process due to their lightweight and high strength. Common alloys include AZ91D and AM60B.
- AZ91D is often used in automotive applications and electronic housings due to its excellent strength-to-weight ratio and good castability. - AM60B provides better ductility and is ideal for applications where higher impact resistance is required.
Conclusion
In summary, the choice of alloy in sand casting is influenced by various factors, including mechanical properties, application requirements, and cost-effectiveness. Aluminum, iron, copper, and magnesium alloys each offer unique benefits that make them suitable for different industrial applications. Understanding these alloys and their characteristics is vital for engineers and manufacturers aiming to produce high-quality cast components that meet specific performance standards and customer expectations. The versatility and adaptability of sand casting, combined with the wide array of compatible alloys, make it a valuable process in modern manufacturing.
Post time:Aug . 12, 2024 14:12
Next:Exploring the Various Materials Used in Sand Casting for Optimal Results and Performance