The Role of Industrial Sand Casting in Modern Manufacturing
Industrial sand casting, also known simply as sand casting, is a widely used method for producing metal parts and components across various industries. This process involves creating a mold from sand that is shaped to form the desired object, followed by pouring molten metal into the mold. Upon cooling and solidification, the mold is removed to reveal the final product. The importance of sand casting in modern manufacturing cannot be overstated, as it combines versatility, cost-effectiveness, and the ability to create complex geometries.
Versatility of Sand Casting
One of the most significant advantages of sand casting is its adaptability to a variety of metals, including ferrous and non-ferrous alloys. This allows manufacturers to tailor their products to specific requirements, whether they are producing iron, aluminum, brass, or steel components. This versatility extends beyond the materials used; sand casting is equally effective for producing small, intricate parts as well as large, heavy components, making it suitable for a wide range of applications—from automotive and aerospace to construction and art foundries.
Cost-Effectiveness
Sand casting is renowned for its cost-effectiveness, particularly for low to medium production runs. The materials required for sand casting—primarily sand, clay, and water—are relatively inexpensive compared to other forms of manufacturing. Moreover, the setup involved in creating a sand mold is less labor-intensive, allowing for quicker turnaround times from design to production. This makes sand casting an appealing option for startups and smaller businesses that may not have the capital for more expensive production methods.
industrial sand casting
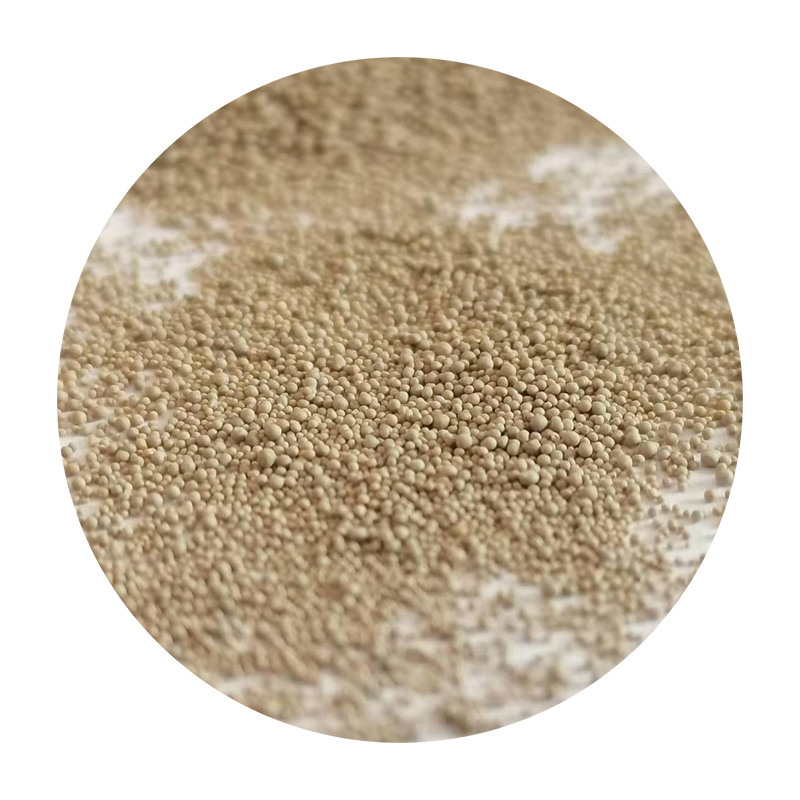
Complexity and Customization
Modern manufacturing often demands products that are not just functional but also exhibit unique designs and complex shapes. Sand casting shines in this area as it can accommodate intricate patterns, including undercuts and thin-walled geometries that may be challenging for other methods like die casting or injection molding. The flexibility in mold design means that manufacturers can easily alter specifications to accommodate specific customer requirements, or even innovate new products without the need for extensive retooling.
Environmental Considerations
As industries increasingly pivot towards sustainable practices, sand casting has demonstrated its adaptability in this regard as well. Traditional processes often create significant waste, but sand casting allows for the recycling of sand—many foundries can reuse the sand multiple times before disposal. Additionally, advancements in technology have led to innovations such as 3D printing of sand molds, which further reduces waste and enhances precision. By minimizing environmental impact, sand casting is becoming an even more compelling manufacturing option for eco-conscious companies.
Conclusion
In conclusion, industrial sand casting remains a cornerstone of modern manufacturing due to its unparalleled versatility, cost-effectiveness, ability to create complex geometries, and environmental benefits. As technologies evolve and industries seek to balance efficiency with sustainability, sand casting is likely to continue playing a critical role in the production of a diverse range of components. Businesses looking to leverage the advantages of this method can look forward to not only meeting current market demands but also adapting to future innovations in manufacturing. Whether for prototyping or mass production, sand casting proves to be an indispensable technique in the realm of manufacturing.
Post time:Jul . 25, 2024 14:20
Next:Exploring the Origins and Development of Sand Casting Techniques Through History and Innovation