3D Printer Sand Casting Revolutionizing Manufacturing
The advent of three-dimensional (3D) printing technology has significantly transformed various industries, particularly in manufacturing processes. One innovative application of 3D printing is in sand casting, a traditional method used for metal casting in which molten metal is poured into a mold made of sand. By integrating 3D printing into sand casting, manufacturers are experiencing a revolution that not only enhances efficiency but also improves design flexibility and reduces costs.
Understanding Sand Casting
Sand casting is one of the oldest and most versatile methods for producing metal parts. The process begins with creating a pattern that molds the shape of the desired component. Traditionally, this pattern is made from materials like wood or metal, which can be time-consuming and costly to produce. After the pattern is created, it is placed into sand to form a mold. Once the mold is prepared, molten metal is poured into it and allowed to cool, solidifying into the final product.
The Role of 3D Printing
3D printing, or additive manufacturing, builds objects layer by layer through computer-aided design (CAD) models. When combined with sand casting, 3D printing offers the capability to create complex molds directly from digital files. This not only reduces the lead time associated with pattern-making but also allows for intricate designs that may be difficult or impossible to achieve with traditional methods.
One of the most notable advantages of using 3D printing in sand casting is the ability to produce complex geometries. Manufacturers can design lightweight structures with complex internal channels for cooling or flow, which are essential for industries like automotive and aerospace. These advanced features can lead to enhanced product performance and significant weight savings.
Cost Efficiency
3d printer sand casting
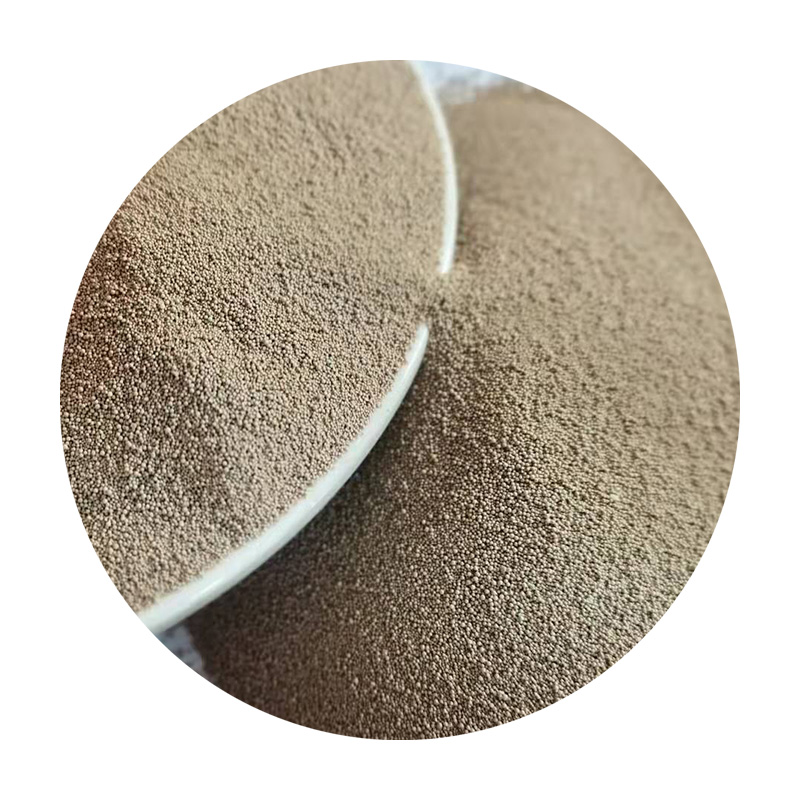
In addition to design benefits, 3D printing can substantially reduce costs associated with sand casting. The traditional method often requires extensive machining and secondary operations to achieve the desired finish and specifications. By leveraging 3D printing, manufacturers can minimize these additional processes, leading to considerable savings. The speed at which molds can be produced also shortens the production cycle, allowing businesses to respond more quickly to market demands.
Furthermore, 3D printing reduces material waste. Traditional sand casting involves the use of excess sand, often resulting in a significant amount of leftover material that must be disposed of. With 3D-printed molds, the precise layering of sand minimizes waste, making the process more environmentally friendly.
Industry Applications
Industries ranging from automotive to aerospace are increasingly adopting 3D printer sand casting techniques. In the automotive sector, companies can produce lightweight components that improve fuel efficiency while maintaining structural integrity. The aerospace industry benefits similarly, with the ability to develop parts that meet rigorous safety and performance standards while reducing weight.
Moreover, the medical field is also experiencing developments through this technology. Custom implants and prosthetics can be produced more rapidly, tailored specifically for individual patients, thus improving overall care and outcomes.
Conclusion
As technology continues to evolve, the fusion of 3D printing and sand casting represents a significant leap forward in manufacturing capabilities. The advantages of reduced lead times, enhanced design complexity, and improved cost-efficiency make this methodology a game-changer in the industry. As more manufacturers embrace these innovative solutions, the potential for 3D printer sand casting to shape the future of production is immense, paving the way for smarter, more efficient manufacturing processes. The integration of these technologies will undoubtedly play a crucial role in meeting the demands of an ever-evolving marketplace.
Post time:Aug . 11, 2024 22:42
Next:Understanding the Impact of Contamination in Foundry Sand on Metal Casting Quality and Performance