The Evolution and Importance of Sand Foundries in Modern Manufacturing
Sand foundries have played a pivotal role in the manufacturing landscape for centuries. As one of the oldest methods of metal casting, the process involves using sand to create molds into which molten metal is poured. This technique has evolved over the years, adapting to advancements in technology while maintaining its fundamental principles. The resurgence of interest in sand foundries is a testament to their enduring relevance and versatility in today’s industry.
At its core, the sand casting process is straightforward. Sand is mixed with a binder and shaped into a mold that captures the desired design. Once the mold is prepared, molten metal is poured into it, cooled, and eventually removed to reveal the final product. This method allows for the production of complex shapes and sizes, making it an attractive option for a wide range of applications, from automobile parts to intricate sculptures.
The Evolution and Importance of Sand Foundries in Modern Manufacturing
The versatility of sand foundries is another critical aspect of their enduring appeal. They can accommodate various types of metals, including iron, aluminum, and bronze, making it possible to produce a wide range of products. The ability to easily modify patterns and molds also means that manufacturers can rapidly adapt to changing market demands, allowing for custom designs and specialty products without significant delays.
sand foundry
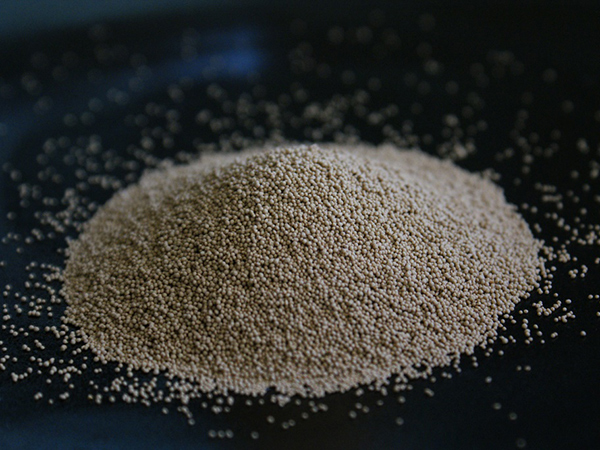
In recent years, sustainability has become an increasingly important concern for manufacturers worldwide. Sand foundries are not only capitalizing on this trend but are also leading the charge towards more eco-friendly practices. Many foundries have adopted sand reclamation processes, which involve recovering and reusing sand from previous casts. This not only reduces waste but also minimizes the need for virgin materials, aligning with global efforts towards sustainable manufacturing.
Technology has also transformed the landscape of sand foundries. Automation and computer-aided design (CAD) have streamlined the mold-making process, enhancing precision and reducing errors significantly. 3D printing technology is making its mark in the industry as well, allowing for rapid prototyping and the creation of complex molds that would be challenging to produce using traditional methods. These advancements are helping sand foundries stay competitive in an ever-evolving market.
Moreover, the significance of sand foundries extends beyond just production. They are vital in preserving traditional craftsmanship and knowledge. As many artisans continue to practice sand casting, they contribute to a heritage that combines art with industrial application. Their skills help maintain the quality and uniqueness of products, which are increasingly valued in a world dominated by mass production.
In conclusion, sand foundries remain an essential facet of modern manufacturing, bridging the gap between ancient techniques and contemporary requirements. Their cost-effectiveness, versatility, commitment to sustainability, and integration of technology ensure that they remain relevant in a competitive market. As industries continue to evolve, the traditional practices of sand foundries are poised to adapt, proving that sometimes, the old ways still have much to offer in shaping the future of manufacturing.
Post time:Jul . 20, 2024 11:49
Next:Reliable Sand Casting Suppliers for Quality Manufacturing and Precision Engineering Solutions