3D Printed Sand Casting Revolutionizing the Foundry Industry
In recent years, advancements in additive manufacturing have reshaped various industries, and foundry operations are no exception. Among these innovations, 3D printed sand casting has emerged as a transformative approach that addresses several longstanding challenges within traditional casting methods. By integrating 3D printing technologies into the sand casting process, manufacturers can improve efficiency, reduce costs, and produce complex geometries that were once deemed impossible.
Traditionally, sand casting has been a staple manufacturing process for metal components. It involves creating a mold from sand, which is then used to produce the desired metal part. This method, while effective, often suffers from several limitations, such as lengthy lead times for mold production, the need for intensive manual labor, and constraints related to mold geometry. The introduction of 3D printing into this process offers significant improvements.
3D Printed Sand Casting Revolutionizing the Foundry Industry
Furthermore, the design flexibility afforded by 3D printing enables the production of complex geometries that are otherwise difficult or impossible to achieve with traditional casting methods. Conventional mold-making techniques often require the creation of multiple components that fit together, leading to increased assembly time and potential for error. In contrast, 3D printed molds can incorporate intricate features, enabling the casting of parts with complex internal structures, undercuts, or lightweight designs that reduce material usage. This flexibility allows engineers to innovate, creating lightweight components that maintain strength and functionality.
3d printed sand casting
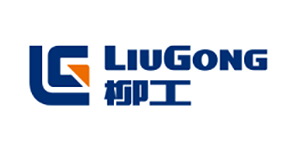
Cost efficiency is another critical benefit of 3D printed sand casting. The process typically utilizes a binder jetting technique, where powdered sand is fused together with a binding agent, creating a mold that can be easily produced. By minimizing material waste and reducing the need for expensive tooling typically associated with traditional casting, manufacturers can achieve significant cost savings. Moreover, because 3D printing allows for on-demand production, companies can reduce their inventory costs by producing molds as needed, rather than maintaining large stockpiles.
The sustainability aspect of 3D printed sand casting also speaks to its growing relevance in today’s manufacturing landscape. Traditional casting often leads to considerable waste, both in terms of materials and energy consumption. 3D printing, with its additive nature, generates less waste, and efforts are underway to use recycled materials in the process. By adopting more sustainable practices, manufacturers can not only meet regulatory requirements but also appeal to environmentally conscious consumers.
While 3D printed sand casting is not without limitations—such as current technology costs and material properties—it is clear that it represents a significant step toward the modernization of the foundry industry. As the technology continues to evolve and become more accessible, it holds the potential to enhance creativity in design, streamline production processes, and ultimately lead to a more sustainable future for manufacturing.
In conclusion, 3D printed sand casting is more than a mere technological trend; it is a paradigm shift that enables manufacturers to overcome traditional constraints. By harnessing the power of this innovative approach, the foundry industry can not only improve efficiency and reduce costs but also embrace a new era of design possibilities and sustainability. As adoption increases, the future of metal component manufacturing looks brighter, driven by the capabilities of 3D printing.
Post time:Aug . 08, 2024 15:50
Next:Exploring the Unique Properties and Applications of Sand-Based Resin Composites in Modern Industry