The Significance of Sand Casting in Modern Industries
Sand casting, often referred to as sand mold casting, is one of the most traditional and widely used manufacturing processes in the modern industry. This method involves creating a mold from sand and pouring molten metal into it to create desired components. Due to its simplicity, cost-effectiveness, and versatility, sand casting has found applications across various sectors, from automotive to aerospace and even art.
The Significance of Sand Casting in Modern Industries
Furthermore, sand casting is well-suited for large-scale production runs. The process allows for the manufacturing of both small and large components with equal efficiency. Industries such as automotive frequently utilize sand casting to produce engine blocks, crankshafts, and transmission cases, among other parts. Given the high demand and required volume of these components, sand casting stands out as a viable option due to its adaptability and cost benefits.
sand cast industries
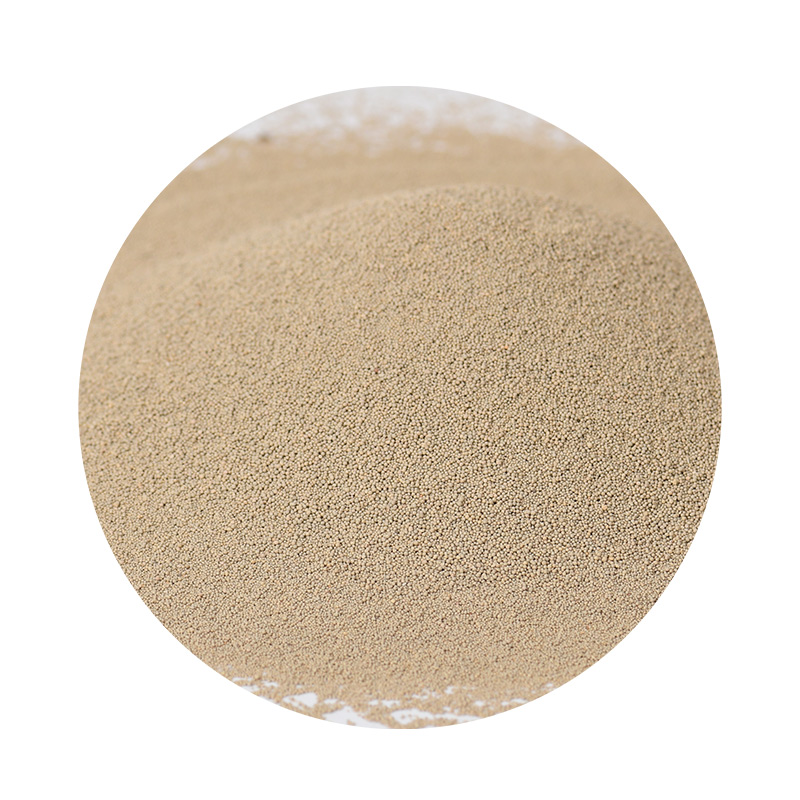
In terms of material versatility, sand casting can accommodate a wide range of metals and alloys, including iron, aluminum, brass, and steel. Each of these materials has specific properties that can be leveraged depending on the application of the end product. For instance, aluminum castings are lightweight and resistant to corrosion, making them ideal for aircraft components, whereas cast iron provides excellent wear resistance, making it suitable for engine blocks and other high-stress applications.
Another critical aspect of sand casting is its environmental impact and sustainability. Many foundries are now actively adopting green sand casting techniques, which use recycled sand and environmentally friendly binders to minimize waste. Additionally, advancements in technology have led to the development of 3D printing methods for creating sand molds, further reducing material waste and production time.
Despite its numerous advantages, sand casting is not without its challenges. One of the most significant drawbacks is the finishing requirements that often follow casting. Due to the inherent roughness of sand-cast surfaces, additional machining processes may be necessary to meet specific tolerance requirements, adding to the production costs and time. Additionally, the porosity inherent in sand-cast parts can lead to issues concerning the strength and durability of the finished product if not controlled correctly.
In conclusion, sand casting is a fundamental process in many industries, notable for its ability to produce complex geometries, accommodate various metal types, and cater to different scale production demands. As technology continues to evolve, so too will the methods and standards of sand casting, making it a continually relevant practice in modern manufacturing. Its balance of affordability, versatility, and effectiveness ensures that sand casting will remain a staple in industrial production for years to come. As manufacturers look for sustainable practices, innovations within sand casting may also help meet the rising demand for environmentally friendly and efficient manufacturing solutions.
Post time:Aug . 15, 2024 04:56
Next:Applications and Benefits of Sand Casting in Modern Manufacturing Processes and Industries