Sanding 3D Printed Parts Techniques and Best Practices
In the world of 3D printing, achieving a smooth, professional finish is often one of the biggest challenges faced by hobbyists and professionals alike. While 3D printing allows for incredible creativity and prototyping capabilities, the layer lines left by the printing process can detract from the aesthetic quality of the final object. This is where sanding comes into play. Sanding 3D printed parts is an essential skill that can elevate the quality of your prints significantly. In this article, we will explore the techniques, tools, and best practices for effectively sanding 3D printed components.
Understanding the Basics
Before diving into the sanding process, it’s important to understand the types of materials you’re working with. Most 3D printed objects are made from thermoplastics like PLA, ABS, and PETG. Each material has unique properties that affect its sandability. For example, PLA is rigid and brittle, which means it can chip if too much force is applied. On the other hand, ABS can be more forgiving due to its flexibility and heat resistance.
Choosing the Right Tools
The first step in the sanding process is selecting the right tools. Basic sanding blocks, foam pads, or even sandpaper wrapped around your finger can be used to smooth surfaces. For intricate designs, a set of needle files can be beneficial for reaching tight spaces. Sandpaper comes in various grits, which determine the roughness of the surface being sanded. Starting with a coarser grit (around 80-120) removes the significant layer lines, while finer grits (up to 2000) can be used to polish the surface to a high gloss finish.
The Sanding Process
1. Preparation Before you start sanding, ensure that your printed part is clean and free of any debris. If there are any supporting structures that need to be removed, do so carefully with pliers or a hobby knife.
sanding 3d printed
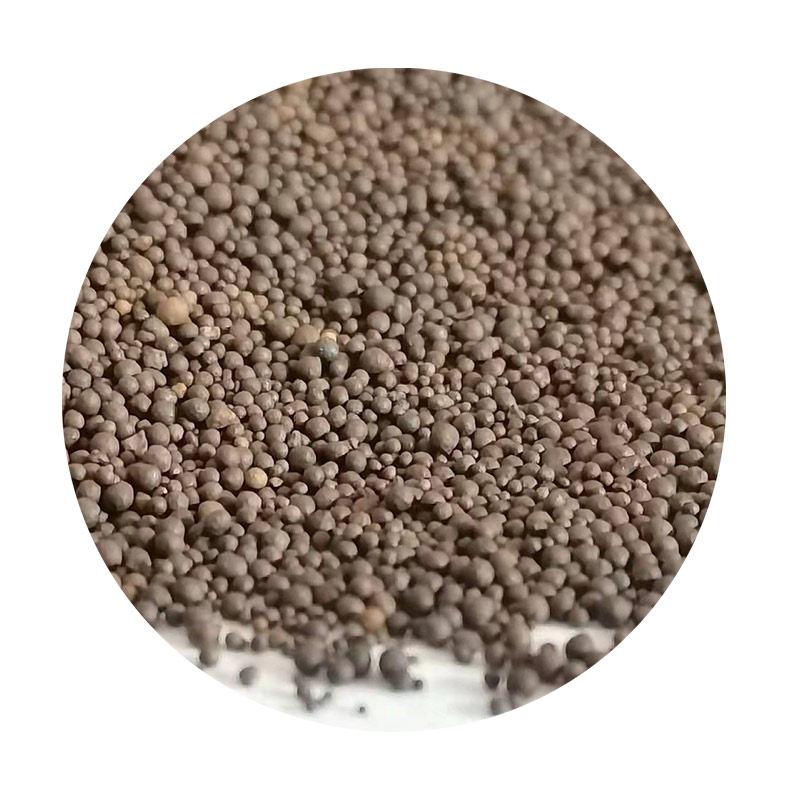
2. Dry Sanding Begin by using a coarse grit sandpaper, focusing on the areas where the layer lines are most pronounced. Use circular motions and apply even pressure to avoid creating flat spots. It’s crucial to be patient, as rushing through this stage may result in an uneven finish.
3. Wet Sanding Once you’ve achieved a relatively smooth surface with dry sanding, switch to finer grit sandpapers (around 400-600 grit). Wet sanding not only helps to reduce dust but also provides a smoother finish. Dip the sandpaper in water and sand in circular motions. This technique minimizes scratches and helps achieve a glossy surface.
4. Polishing After wet sanding, you may want to apply a polish or a clear coat to enhance the shine. Polishing compounds can be used for this purpose, providing a professional finish to your 3D printed part. Apply the polish with a soft cloth, and buff until you reach the desired sheen.
Best Practices and Tips
- Patience is Key Sanding can be time-consuming, but rushing through the process often leads to undesirable results. Take your time to ensure each stage is completed thoroughly. - Test on Scraps If you’re unsure about the sanding technique or grit to use, practice on scrap pieces or failed prints. This will help you gauge the right amount of pressure and technique to apply to your final product. - Protect Yourself Always wear a mask and goggles during sanding to protect against fine dust particles that can be harmful when inhaled or irritate the eyes.
Conclusion
Sanding 3D printed parts is an art form that can greatly enhance the quality and aesthetics of your prints. Whether you are creating functional prototypes or artistic models, mastering the sanding process will allow you to present your work in the best possible light. With patience, the right tools, and careful execution, you can transform a 3D printed object from a rough prototype into a smooth, professional-grade piece. Embrace the journey of sanding, and let your creativity shine through your finished prints!
Post time:Jul . 28, 2024 19:44
Next:Exploring the Current Trends and Prices of Ceramic Sand in the Market Today